1. Značky povrchovej stupnice
Hlavné vlastnosti: Nesprávne spracovanie matricevýhradaspôsobí hrubé povrchy a značky na stupnici rýb. Takéto drsné značky na stupnici rýb sa ľahko vyrábajú, keď kovanie austenitickej a martenzitickej nehrdzavejúcej ocele.
Príčina: Lokálna sliznica spôsobená nerovnomerným mazaním alebo nesprávnym výberom mazania a zlej kvality mazacieho oleja.
2. Defekty chýb
Hlavné vlastnosti: Horná časť kovania matríc je nesprávne zarovnaná vzhľadom na spodnú časť pozdĺž rozlúčkovej plochy.
Príčina: Na kovaniach nie je žiadny vyvážený zámok vyváženia, alebo kovanie matrice nie je správne inštalované alebo medzera medzi hlavou kladiva a vodiacou koľajnicou je príliš veľká.
3. Nedostatočné defekty na kovanie
Hlavné vlastnosti: Veľkosť kŕmenia matrice sa zvyšuje v smere kolmom na rozlúčkovú plochu. Ak veľkosť presahuje veľkosť určenú pri výkrese, dôjde k nedostatočnému kovaniam.
Príčina: Veľká veľkosť, nízka teplota kovania, nadmerné opotrebenie dutiny matrice atď. Povedie k nedostatočnému tlaku alebo nadmernému odporu bleskového mosta, nedostatočnej tonáže zariadenia a nadmernému objemu sochorov.
4. Nedostatočná miestna výplň
Hlavné črty: Vyskytujú sa hlavne v rebrách, konvexných mŕtvych rohov atď. Výkovky matrice a horná časť výplňovej časti alebo rohy výlovu nie sú dostatočne vyplnené, takže obrys výkrikov nie je jasný
Dôvod: Návrh dutiny preformulovania a dutiny s medzerami je neprimeraný, tonáž zariadenia je malá, prázdne miesto nie je dostatočne zahrievané a kovová plynulosť je zlá, čo môže spôsobiť tento defekt.
5. Zvyšky štruktúry liatia
Hlavné črty: Ak existuje štruktúra zvyškovej odliatku, predĺženie a únava sily výkovkov sú často nekvalifikované. Pretože pri testovacom kuse s nízkym zväčšením nie sú zrejmé prúdenie blokovanej časti zvyškového odlievania a je možné vidieť dokonca aj dendritické výrobky, ktoré sa objavujú hlavne u výkrikov pomocou oceľových ingotov ako medzery.
Dôvod: Z dôvodu nedostatočného pomeru kovania alebo nesprávnej metódy kovania. Táto defekt znižuje výkon výkoviek, najmä na húževnatosť a vlastnosti únavy.
6. Nehomogenita zrna
Hlavné vlastnosti: Zrná v niektorých častiachvýhradasú obzvlášť hrubé, zatiaľ čo zrná v iných častiach sú menšie a vytvárajú nerovnomerné zrná. Vysokoteplotné zliatiny a ocele odolné voči teplom sú obzvlášť citlivé na nehomogenitu zŕn.
Príčina: Nízka konečná teplota kovania spôsobuje kalenie miestnej práce so sídlom zliatiny s vysokou teplotou. Počas procesu ochladzovania a zahrievania niektoré zrná rastú vážne alebo počiatočná teplota kovania je príliš vysoká a deformácia nie je dostatočná, čo spôsobuje, že miera deformácie miestnej oblasti spadá do kritickej deformácie. Nerovnomernosť zŕn môže ľahko viesť k zníženiu únavovej výkonnosti a trvanlivosti.
7. Skladacie chyby
Hlavné vlastnosti: Zvieratá sú ohnuté v záhyboch vzorky s nízkym zväzom a záhyby majú podobný vzhľad ako praskliny. Ak ide o trhlinu, prúdia sa vyrezávajú dvakrát. Na vzorke s vysokým zväčšením, na rozdiel od spodnej časti trhliny sú obe strany vážne oxidované a spodná časť je tupá.
Príčina: Je to hlavne spôsobené príliš malým kŕmením, príliš veľkým redukciou alebo príliš malým polomerom kovadlého filé počas procesu výkresu výkresov tyčiniek a výkoviek kľukového hriadeľa. Skladovacie defekty spôsobujú, že oxidovaný povrchový kov sa počas procesu kovania spoja.
8. Nesprávne kovanie
Hlavné funkcie: Streamline turbulencie, ako je prúdový reflux, vírivý prúd, odpojenie a konvekcia, sa vyskytuje, keď kovanie je nízky výkon.
Príčina: Nesprávny dizajn, nesprávny výber metódy kovania, neprimeraný tvar a veľkosť sochory.
9. Banded štruktúra
Hlavné vlastnosti: Štruktúra, v ktorej sú v pásmoch distribuované iné štruktúry alebo feritové fázy vo výškách. Existuje hlavne v austeniticko-ferritickej nehrdzavejúcej oceli, polotartenzitickej oceli a eutektoidnej oceli.
Príčina: Je to spôsobené kovaním deformácie, keď koexistujú dve sady častí. Znižuje index priečnej plasticity materiálu a je náchylný k prasknutiu pozdĺž feritovej zóny alebo hranice medzi týmito dvoma fázami.
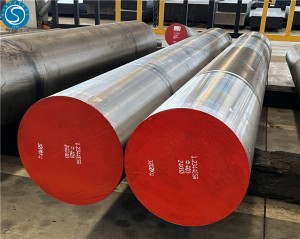
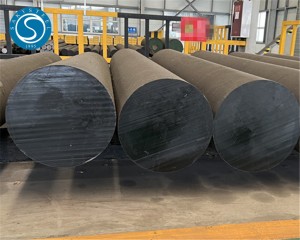
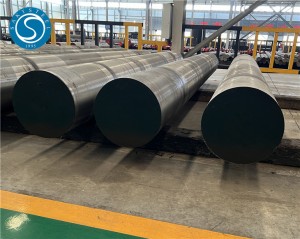
Čas príspevku: 13. júna-2024