Ⅰ. Основная концепция термообработки.
A. Основная концепция термообработки.
Основные элементы и функциитермическая обработка:
1. Выживание
Цель состоит в том, чтобы получить равномерную и тонкую структуру аустенита.
2. удержание
Цель состоит в том, чтобы гарантировать, что заготовка тщательно нагревается и предотвращает декарбуризацию и окисление.
3. Охлаждение
Цель состоит в том, чтобы преобразовать аустенит в разные микроструктуры.
Микроструктуры после термообработки
Во время процесса охлаждения после нагрева и удержания аустенит превращается в различные микроструктуры в зависимости от скорости охлаждения. Различные микроструктуры демонстрируют разные свойства.
B. Основная концепция термообработки.
Классификация на основе методов нагрева и охлаждения, а также микроструктуры и свойств стали
1. Контракциозная термообработка (общая термообработка): отжигание, отжиг, нормализация, гашение
2. Поверхностная термообработка: гашение поверхности, индукционная нагревательная гашение поверхности, гашение поверхности огня, электрическое контактное нагревание поверхности.
3. Химическая термообработка: карбивизионная, ниотричинка, карбонирирование.
4. Другие теплообразные обработки: контролируемая термообработка атмосферы, тепловая обработка вакуума, тепловая обработка деформации.
С. Критическая температура сталей
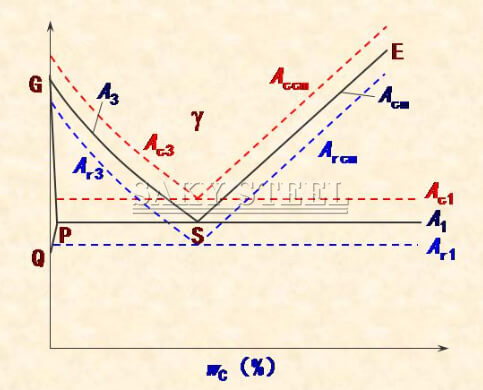
Критическая температура преобразования стали является важной основой для определения процессов нагрева, удержания и охлаждения во время термической обработки. Это определяется с диаграммой железной углеродной фазы.
Ключевой вывод:Фактическая температура критического преобразования стали всегда отстает от теоретической температуры критического преобразования. Это означает, что во время охлаждения требуется перегрев, а во время охлаждения необходимо перегрев.
Ⅱ. Анналирование и нормализация стали
1. Определение отжига
Отжиг включает нагревание стали до температуры выше или ниже критической точки, удерживающей ее при этой температуре, а затем медленно охлаждение ее, обычно в печи, чтобы достичь структуры, близкой к равновесию.
2. Цель отжига
①Дускую жесткость для обработки: достижение механической твердости в диапазоне HB170 ~ 230.
② Повторная остаточная стресс: предотвращает деформацию или растрескивание во время последующих процессов.
③Refine зерновая структура: улучшает микроструктуру.
Preparation для окончательной термообработки: получает гранулированный (сфероидированный) перлит для последующего гашения и отпуска.
3. Сфероидация отжига
Технические характеристики процесса: температура нагрева находится вблизи точки AC₁.
Цель: сфероидизации цементита или карбидов в стали, что приводит к гранулированному (сфероидированному) жемчужину.
Применимый диапазон: используется для сталей с эвтектоидными и гипертектоидными композициями.
4. Обожание отжига (гомогенизирующий отжиг)
Технические характеристики процесса: Температура нагрева немного ниже линии Solvus на фазовой диаграмме.
Цель: устранить сегрегацию.
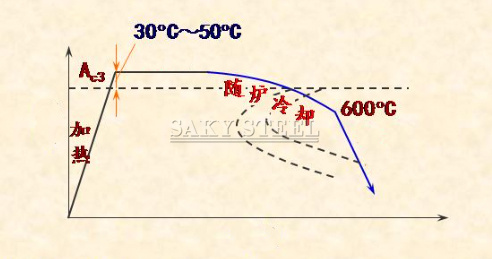
① Для низкого-углеродистая стальПри содержании углерода менее 0,25%нормализация предпочтительнее отжига в качестве подготовительной термообработки.
② Для средней углеродной стали с содержанием углерода между 0,25% до 0,50%, отжига или нормализации может использоваться в качестве подготовительной термообработки.
③ Для средней до высокоуглеродной стали с содержанием углерода от 0,50% до 0,75% рекомендуется полный отжиг.
④ Для высокого-углеродистая стальС содержанием углерода более 0,75%, нормализация сначала используется для устранения сети FE₃C, за которым следует сфероидизм отжига.
Ⅲ. Кормирование и отпуск стали
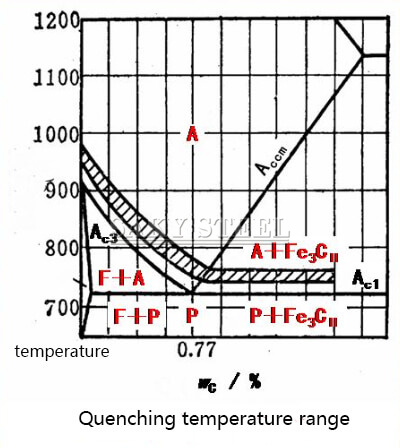
A.quenching
1. Определение гашения: гашение включает нагревание стали до определенной температуры над точкой AC₃ или AC₁, удерживая ее при этой температуре, а затем охлаждение ее со скоростью, превышающей критическую скорость охлаждения, образуя мартенсит.
2. Цель гашения: основная цель - получить мартенсит (или иногда более низкий байнит) для увеличения твердости и износостойкости стали. Угашение является одним из наиболее важных процессов термообработки для стали.
3. определение температуры гашения для разных типов стали
Гипоэвтэктоидная сталь: ac₃ + 30 ° C до 50 ° C
Эвтектоидная и гиперэтэктоидная сталь: AC₁ + 30 ° C до 50 ° C
Сплав Сталь: от 50 ° С до 100 ° С выше критической температуры
4. Охлаждающие характеристики идеальной гашения:
Медленное охлаждение до «носа» температуры: чтобы достаточно уменьшить тепловое напряжение.
Высокая способность охлаждения вблизи «носа» температуры: чтобы избежать образования нертенситных конструкций.
Медленное охлаждение вблизи M₅ точка: чтобы минимизировать напряжение, вызванное мартенситным преобразованием.
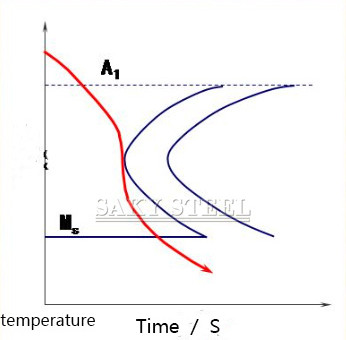
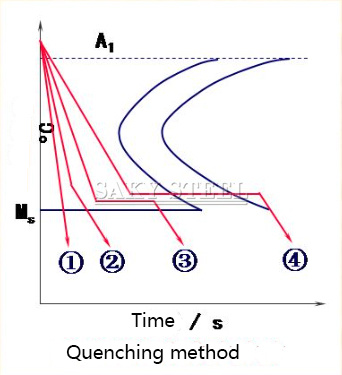
5. Кормирование методов и их характеристики:
① Стоимость гашения: Легко работать и подходит для небольших, простых в форме заготовков. Полученной микроструктурой является мартенсит (м).
Adubule гашение: более сложный и трудный для контроля, используется для сложной формы высокого уровня углеродной стали и более крупных сплавных стали. Полученной микроструктурой является мартенсит (м).
③ Изъян гашетка: более сложный процесс, используемый для крупных сложных сплавных стальных заготовков. Полученной микроструктурой является мартенсит (м).
④ Изотермальный закал: используется для небольших сложных заготовков с высокими требованиями. Полученная микроструктура ниже Bainite (B).
6. Факторы, влияющие на устойчивость
Уровень закаляемости зависит от стабильности аустенита из переохлаждения в стали. Чем выше стабильность сверху прохладного аустенита, тем лучше укрепление и наоборот.
Факторы, влияющие на стабильность аустенита из переохлаждения:
Положение C-кривой: если C-кривая сдвигается вправо, критическая скорость охлаждения для гашения уменьшается, улучшает закаленность.
Ключевой вывод:
Любой фактор, который сдвигает C-кривую вправо, увеличивает укрепление стали.
Основной фактор:
Химический состав: за исключением кобальта (CO), все легирующие элементы, растворенные в аустените, увеличивают укрепление.
Чем ближе содержание углерода к эвтэктоидной составе в углеродистой стали, тем больше C-кривая смещается вправо, а тем выше укрепление.
7. Определение и представление отвердоспособности
①end Тест на закал в закал.
②critical Diage Diameter Метод: Диаметр критического характера (D₀) представляет максимальный диаметр стали, который может быть полностью закален в определенной среде для гашения.
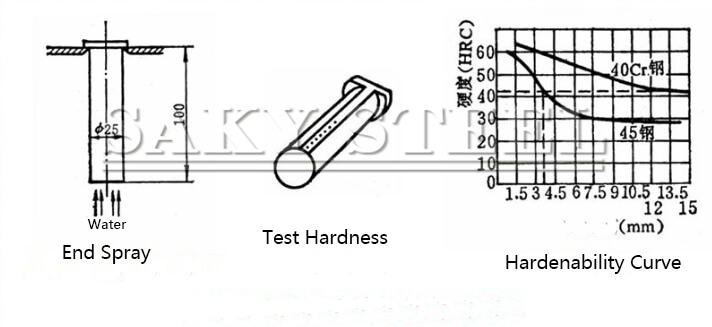
Б. Цель
1. Определение отказа
Удерживание - это процесс термообработки, при котором сталь гашена разогревается до температуры ниже точки A₁, удерживаемой при этой температуре, а затем охлаждается до комнатной температуры.
2. Цель отмены
Уменьшить или устранить остаточное напряжение: предотвращает деформацию или растрескивание заготовки.
Уменьшите или устраните остаточный аустенит: стабилизирует размеры заготовки.
Устранение хрупкости гашной стали: корректирует микроструктуру и свойства в соответствии с требованиями заготовки.
Важное примечание: сталь должна быть смягчена незамедлительно после гашения.
3. Процессы Tempering
1. Показ
Цель: чтобы уменьшить утомительное напряжение, улучшить жесткость заготовки и достичь высокой твердости и износостойкости.
Температура: 150 ° C ~ 250 ° C.
Производительность: Твердость: HRC 58 ~ 64. Высокая твердость и стойкость к износу.
Применение: инструменты, формы, подшипники, изготовленные детали и поверхностные компоненты.
2. Высокий отпуск
Цель: достичь высокой прочности наряду с достаточной силой и твердостью.
Температура: 500 ° C ~ 600 ° C.
Производительность: Твердость: HRC 25 ~ 35. Хорошие общие механические свойства.
Приложения: валы, шестерни, шатуны и т. Д.
Тепловое уточнение
Определение: гашение с последующим высокотемпературным отпуском называется термическим переработкой или просто отпуска. Сталь, обработанная этим процессом, имеет отличную общую производительность и широко используется.
Ⅳ. Поверхностная термообработка стали
А. Пострадание сталей стали
1. Определение упрочнения поверхности
Поверхностное затвердевание - это процесс термообработки, предназначенный для укрепления поверхностного слоя заготовки путем быстрого нагревания его, чтобы превратить поверхностный слой в аустенит, а затем быстро охладить его. Этот процесс проводится без изменения химического состава стали или основной структуры материала.
2. Материалы, используемые для упрочнения поверхности и пост-хардирования
Материалы, используемые для упрочнения поверхности
Типичные материалы: средняя углеродистая сталь и сталь средней углеродной сплавы.
Предварительная обработка: Типичный процесс: отпуск. Если основные свойства не являются критическими, вместо этого можно использовать нормализацию.
Структура пост-хардирования
Структура поверхности: поверхностный слой обычно образует закаленную структуру, такую как мартенсит или байнит, который обеспечивает высокую твердость и износ.
Структура ядра: ядро стали, как правило, сохраняет свою исходную структуру, такую как жемчужное или измеренное состояние, в зависимости от процесса предварительной обработки и свойств базового материала. Это гарантирует, что ядро поддерживает хорошую прочность и силу.
B.характеристика индукционной поверхностной затвердевания
1. Высокая температура нагрева и быстрое повышение температуры: индукционная поверхностная упрочнение обычно включает высокую температуру нагрева и быстрые скорости нагрева, что позволяет быстро нагревать в течение короткого времени.
2. Структура зерна аустенита в поверхностном слое: во время быстрого нагрева и последующего процесса гашения поверхностный слой образует тонкие зерна аустенита. После гашения поверхность в основном состоит из тонкого мартенсита, с твердостью, как правило, на 2-3 HRC выше, чем обычное гашение.
3. Хорошее качество поверхности: из-за короткого времени нагрева поверхность заготовки менее подвержена окислению и декарбурению, а деформация, вызванная гасимостью, сведена к минимуму, обеспечивая хорошее качество поверхности.
4. Высокая сила усталости: трансформация мартенситной фазы в поверхностном слое создает сжатие, что увеличивает усталостную силу заготовки.
5. Высокая эффективность производства: индукционное усиление поверхности подходит для массового производства, что обеспечивает высокую эксплуатационную эффективность.
C. Классификация химической термообработки
Карбинизация, карбинизация, карбинизация, хромизирование, кремнизация, кремнизация, силиконизирование, карбонирирование, борокарбуризация
Д. ГАС Карбуризируется
Газовая карбинизация - это процесс, в котором заготовка помещается в герметичную газовую печь и нагревается до температуры, которая превращает сталь в аустенит. Затем в печи капают атмосферу, или вводится атмосфера, позволяющая атомам углерода диффундировать в поверхностный слой заготовки. Этот процесс увеличивает содержание углерода (WC%) на поверхности заготовки.
√carburizing Agents:
• Богатые углерода газы: такие как угольный газ, нефтяной нефтяной газ (СНГ) и т. Д.
• Органические жидкости: такие как керосин, метанол, бензол и т. Д.
√carburizing Параметры процесса:
• ТЕМПЛАТА СЛУЧАЯ: 920 ~ 950 ° C.
• Время, связанное с карбинизацией: зависит от желаемой глубины изготовленного слоя и температуры с карбибинейностью.
Е.
Сталь должна подвергаться термической обработке после карбинизации.
Процесс термической обработки после карбинизации:
√quenching + низкотемпературный отпуск
1. Хотовивание сдачи после предварительного охлаждения + низкотемпературное отпуск: заготовка предварительно охлаждается от температуры карбинизации до чуть выше температуры AR₁ ядра, а затем сразу же утолкнут, а затем низкотемпературное отпуск при 160 ~ 180 ° C.
2. Стоимость гашения после предварительного охлаждения + низкотемпературное отпуск: после карбинизации заготовка медленно охлаждается до комнатной температуры, а затем разогревается для гашения и низкотемпературного отпуска.
3. Хотовивание по гамбе после предварительного охлаждения + низкотемпературное отпуск: после карбибинизации и медленного охлаждения заготовка подвергается двум стадиям нагрева и гасительнее, за которым следует низкотемпературный отпуск.
Ⅴ. Химическая термообработка сталей
1. Определение химической термообработки
Химическая термообработка - это процесс термообработки, в котором стальная заготовка помещается в определенную активную среду, нагревается и удерживается при температуре, позволяя активным атомам в среде диффундировать на поверхность заготовки. Это изменяет химический состав и микроструктуру поверхности заготовки, тем самым изменяя ее свойства.
2. Базический процесс химической термообработки
Разложение: во время нагрева активная среда разлагается, высвобождая активные атомы.
Поглощение: активные атомы адсорбируются поверхностью стали и растворяются в твердом растворе стали.
Диффузия: активные атомы поглощаются и растворяются на поверхности стали, мигрируют во внутреннюю часть.
Типы индукционной поверхностной упрочнения
A. ВЫГОДНОЕ ВОЗВРАЖЕНИЕ Индукционное отопление
Частота тока: 250 ~ 300 кГц.
Затвердевшая глубина слоя: 0,5 ~ 2,0 мм.
Приложения: средние и маленькие шестерни модуля и малые до средних валов.
B. Медиевая частота индукционного нагрева
Частота тока: 2500 ~ 8000 кГц.
Затвердевшая глубина слоя: 2 ~ 10 мм.
Приложения: большие валы и передачи для больших и средних модулей.
C. Добростого индукционного нагрева
Частота тока: 50 Гц.
Затвердевшая глубина слоя: 10 ~ 15 мм.
Приложения: заготовки, требующие очень глубокого закаленного слоя.
3. Индукционная поверхностная затвердевание
Основной принцип индукционной поверхностной упрочнения
Эффект кожи:
Когда чередование тока в индукционной катушке вызывает ток на поверхности заготовки, большая часть индуцированного тока концентрируется вблизи поверхности, в то время как почти ни один ток проходит через внутреннюю часть заготовки. Это явление известно как эффект кожи.
Принцип индукционной поверхности затвердевания:
Основываясь на эффекте кожи, поверхность заготовки быстро нагревается до аустенизирующей температуры (поднимаясь до 800 ~ 1000 ° C за несколько секунд), в то время как внутренняя часть заготовки остается практически без отдыха. Затем заготовка охлаждается при распылении воды, достигая усиления поверхности.
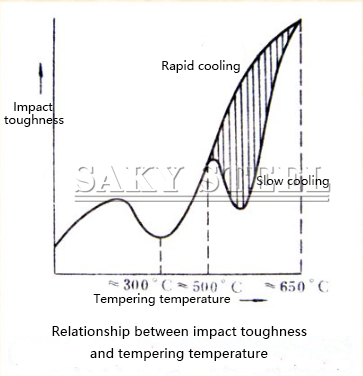
4. Темпер Бриттлис
Смягчающая хрупкость в гашенной стали
Удерживание хрупкости относится к явлению, когда ударная вязкость уточенной стали значительно уменьшается при закале при определенных температурах.
Первый тип хранения
Диапазон температуры: от 250 ° C до 350 ° C.
Характеристики: если сталь закалена в пределах этого температурного диапазона, она, вероятно, разработает этот тип отпуска, который не может быть устранен.
Решение: избегайте утоленной стали в этом диапазоне температуры.
Первый тип сдавшейся хрупкости также известен как низкотемпературная хрупкость или необратимая хрупкость.
Ⅵ.tempering
1. Темпл - это окончательный процесс термообработки, который следует за гашением.
Зачем утомить стали, нуждается в отпуске?
Микроструктура после гашения: после гашения микроструктура стали обычно состоит из мартенсита и остаточного аустенита. Оба являются метастабильными фазами и будут трансформироваться при определенных условиях.
Свойства Martensite: Martensite характеризуется высокой твердостью, но также высокой хрупкой (особенно в высокоуглеродном игорном мартенсите), который не соответствует требованиям к производительности для многих приложений.
Характеристики мартенситной трансформации: трансформация в мартенсит происходит очень быстро. После гашения заготовка имеет остаточные внутренние напряжения, которые могут привести к деформации или растрескиванию.
Вывод: заготовка не может быть использована непосредственно после гашения! Умерение необходимо для уменьшения внутренних напряжений и повышения жесткости заготовки, что делает его подходящим для использования.
2. Разница между упространенностью и устойчивой способностью:
Закаленность:
Утвердимость относится к способности стали достигать определенной глубины затверждения (глубины закаленного слоя) после гашения. Это зависит от композиции и структуры стали, особенно ее легирующих элементов и типа стали. Утвердимость - это мера того, насколько хорошо сталь может затвердеть на протяжении всей его толщины во время процесса гашения.
Твердость (упрочнение емкости):
Твердость, или упрочнение, относится к максимальной твердости, которая может быть достигнута в стали после гашения. На него во многом влияет содержание углерода в стали. Более высокое содержание углерода обычно приводит к более высокой потенциальной твердости, но это может быть ограничено легирующими элементами стали и эффективностью процесса гашения.
3. Характеризуемость стали
√concept of Hustderability
Утвердимость относится к способности стали достигать определенной глубины мартенситного упрочнения после гашения от аустенизирующей температуры. Проще говоря, это способность стали образовывать мартенсит во время гашения.
Измерение закаленности
Размер затвердования обозначается глубиной закаленного слоя, полученного в указанных условиях после гашения.
Глубина закаленного слоя: это глубина от поверхности заготовки до области, где структура наполовину мартенсит.
Обыкновенное утоление средств массовой информации:
•Вода
Характеристики: Экономичные с сильной способностью охлаждения, но имеют высокую скорость охлаждения вблизи точки кипения, что может привести к чрезмерному охлаждению.
Применение: обычно используется для углеродных стали.
Соленая вода: раствор соли или щелочи в воде, который имеет более высокую охлаждающую способность при высоких температурах по сравнению с водой, что делает его подходящим для углеродных стали.
•Масло
Характеристики: обеспечивает более медленную скорость охлаждения при низких температурах (вблизи точки кипения), что эффективно снижает тенденцию к деформации и растрескиванию, но имеет более низкую способность охлаждения при высоких температурах.
Приложение: подходит для сплавных сталей.
Типы: включает в себя гашение масла, машинного масла и дизельного топлива.
Время отопления
Время нагрева состоит как из скорости нагрева (время, необходимое для достижения желаемой температуры), так и времени удержания (время, которое поддерживается при целевой температуре).
Принципы для определения времени нагрева: обеспечить равномерное распределение температуры по всей заготовке, как внутри, так и снаружи.
Обеспечить полную аустенизацию и что образованный аустенит является равномерным и мелким.
Основа для определения времени нагрева: обычно оценивается с использованием эмпирических формул или определяется посредством экспериментов.
Утомить СМИ
Два ключевых аспекта:
А.
B. Резидуальное напряжение: более высокая скорость охлаждения увеличивает остаточное напряжение, что может привести к большей тенденции к деформации и растрескиванию на заготовке.
Ⅶ. Нормализующий
1. Определение нормализации
Нормализация-это процесс термической обработки, при котором сталь нагревается до температуры от 30 ° C до 50 ° C выше температуры AC3, удерживаемой при этой температуре, а затем с воздушным охлаждением, чтобы получить микроструктуру, близкую к состоянию равновесия. По сравнению с отжигом, нормализация имеет более высокую скорость охлаждения, что приводит к более тонкой структуре перлит (P) и более высокой прочности и твердости.
2. Цель нормализации
Цель нормализации аналогична цели отжига.
3. Приложения нормализации
• Устранение сетевого вторичного цемента.
• Служить в качестве конечной термообработки для деталей с более низкими требованиями.
• Выступайте в качестве преодолевающей термообработки для низкой и средней конструкционной стали углерода для улучшения механизма.
4.types отжига
Первый тип отжига:
Цель и функция: цель состоит не в том, чтобы вызвать фазовое преобразование, а перевести сталь из несбалансированного состояния в сбалансированное состояние.
Типы:
• Отжиг диффузии: стремится гомогенизировать композицию путем устранения сегрегации.
• Отжиг перекристаллизации: восстанавливает пластичность, устраняя последствия укрепления работы.
• Отжиг снятия стресса: уменьшает внутренние напряжения без изменения микроструктуры.
Второй тип отжига:
Цель и функция: стремится изменить микроструктуру и свойства, достигнув микроструктуры, в которой доминируют жемчужины. Этот тип также гарантирует, что распределение и морфология перлит, ферритов и карбидов отвечало конкретным требованиям.
Типы:
• Полный отжиг: нагревает сталь над температурой AC3, а затем медленно охлаждает ее, чтобы получить равномерную перлит -структуру.
• Неполное отжиг: нагревает сталь между температурами AC1 и AC3, чтобы частично трансформировать структуру.
• Изотермический отжиг: нагревает сталь выше AC3, затем быстрое охлаждение до изотермической температуры и удержание для достижения желаемой структуры.
• Сфероидация отжига: создает сфероидальную карбидную структуру, улучшение механизма и выносливости.
Ⅷ.1. Определение термообработки
Тепловая обработка относится к процессу, в котором металл нагревается, удерживается при определенной температуре, а затем охлаждается в твердом состоянии, чтобы изменить его внутреннюю структуру и микроструктуру, тем самым достигая желаемых свойств.
2. Шарактеристики термообработки
Тепловая обработка не меняет форму заготовки; Вместо этого он изменяет внутреннюю структуру и микроструктуру стали, которая, в свою очередь, меняет свойства стали.
3. Наличие термообработки
Целью термообработки является улучшение механических или обработчивых свойств стали (или заготовки), полностью использовать потенциал стали, повысить качество заготовки и продлить срок службы.
4. КЛЮЧ
Можно ли улучшить свойства материала с помощью термообработки, зависит от того, существуют ли изменения в его микроструктуре и структуре во время процесса нагрева и охлаждения.
Время сообщения: 19-2024 августа