Ⅰ. Conceptul de bază al tratamentului termic.
A. Conceptul de bază al tratamentului termic.
Elementele și funcțiile de bază aleTratament termic:
1. încălzire
Scopul este obținerea unei structuri austenite uniforme și fine.
2. Deținerea
Scopul este de a se asigura că piesa de lucru este complet încălzită și de a preveni decarburizarea și oxidarea.
3.cooling
Obiectivul este de a transforma austenita în microstructuri diferite.
Microstructuri după tratamentul termic
În timpul procesului de răcire după încălzire și menținere, austenita se transformă în microstructuri diferite, în funcție de viteza de răcire. Microstructuri diferite prezintă proprietăți diferite.
B. Conceptul de bază al tratamentului termic.
Clasificare bazată pe metode de încălzire și răcire, precum și microstructura și proprietățile oțelului
1. Tratamentul termic convențional (tratament la căldură generală): temperare, recoacere, normalizare, stingere
2. Tratarea termică a suprafeței: stingerea suprafeței, stingerea suprafeței de încălzire a inducției, stingerea suprafeței de încălzire a flăcării, stingerea suprafeței de încălzire electrică de încălzire.
3. Tratamentul termic chimic: carburizare, nitring, carbonitring.
4. Alte tratamente termice: tratament termic al atmosferei controlate, tratament termic cu vid, tratament termic de deformare.
C. Temperatura critică a oțelurilor
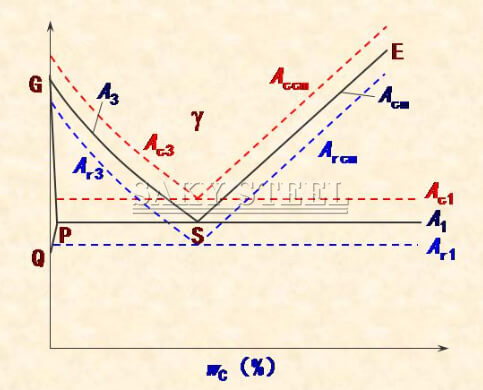
Temperatura critică de transformare a oțelului este o bază importantă pentru determinarea proceselor de încălzire, menținere și răcire în timpul tratamentului termic. Este determinată de diagrama fazei de fier-carbon.
Concluzie cheie:Temperatura de transformare critică reală a oțelului rămâne întotdeauna în urma temperaturii teoretice de transformare critică. Acest lucru înseamnă că supraîncălzirea este necesară în timpul încălzirii, iar subcoolarea este necesară în timpul răcirii.
Ⅱ.Aninerea și normalizarea oțelului
1. Definiția recoacerii
Recuperarea implică încălzirea oțelului la o temperatură deasupra sau sub punctul critic care îl ține la temperatura respectivă, apoi răcirea lentă, de obicei în interiorul cuptorului, pentru a obține o structură apropiată de echilibru.
2. Scopul recoacerii
① Aadjust Duritatea pentru prelucrare: Realizarea durității mașinabile în gama HB170 ~ 230.
Stress Stress rezidual: previne deformarea sau fisurarea în timpul proceselor ulterioare.
Structura rezidului cerealelor: îmbunătățește microstructura.
④ Preparation pentru tratamentul termic final: obține perle granular (sferoidizat) pentru stingerea și temperarea ulterioară.
3. Recuperare aferoidizantă
Specificații ale procesului: Temperatura de încălzire este aproape de punctul AC₁.
Scopul: sferoidizarea cimentului sau carburilor din oțel, rezultând perle granulare (sferoidizate).
Interval aplicabil: utilizat pentru oțeluri cu compoziții eutectoide și hipereutetectoide.
4. Difuzarea recoacerii (omogenizarea recoacerii)
Specificații ale procesului: Temperatura de încălzire este puțin sub linia Solvus din diagrama de fază.
Scop: eliminarea segregării.
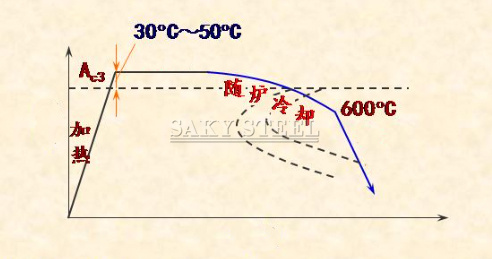
① Pentru scăzutOțel de carbonCu un conținut de carbon mai mic de 0,25%, normalizarea este preferată față de recoacere ca tratament termic pregătitor.
②Pentru oțelul cu carbon mediu cu conținut de carbon între 0,25% și 0,50%, recoacere sau normalizare poate fi utilizată ca tratament termic pregătitor.
③Pentru oțel mediu până la ridicat de carbon, cu conținut de carbon între 0,50% și 0,75%, se recomandă o recoacere completă.
④PentruOțel de carbonCu conținutul de carbon mai mare de 0,75%, normalizarea este utilizată pentru prima dată pentru a elimina rețeaua FE₃C, urmată de recoacere sferoidizantă.
Ⅲ.
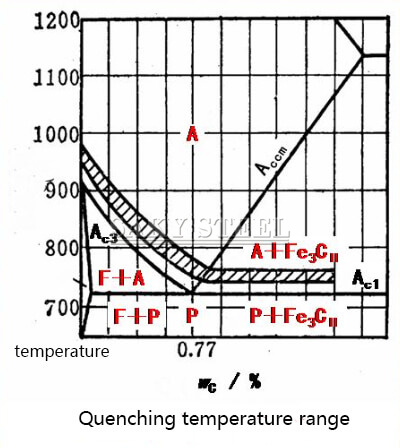
A.quenching
1. Definiția stingerii: stingerea implică încălzirea oțelului la o anumită temperatură peste punctul AC₃ sau AC₁, ținându -l la acea temperatură și apoi răcirea acesteia la o viteză mai mare decât rata de răcire critică pentru a forma martensite.
2. Scopul stingerii: Scopul principal este obținerea martensitei (sau uneori bainitul inferior) pentru a crește duritatea și rezistența la uzură a oțelului. Schemarea este unul dintre cele mai importante procese de tratare termică pentru oțel.
3. Determinarea temperaturilor de stingere pentru diferite tipuri de oțel
Oțel hipoeutectoid: AC₃ + 30 ° C până la 50 ° C
Oțel eutectoid și hipereutectoid: AC₁ + 30 ° C până la 50 ° C
Oțel din aliaj: 50 ° C până la 100 ° C peste temperatura critică
4. Caracteristicile de acoperire a unui mediu de stingere ideal:
Răcire lentă înainte de temperatura „nasului”: pentru a reduce suficient stresul termic.
Capacitate ridicată de răcire în apropierea temperaturii „nasului”: pentru a evita formarea de structuri non-marțitene.
Răcire lentă în apropierea punctului m₅: pentru a minimiza stresul indus de transformarea martensitică.
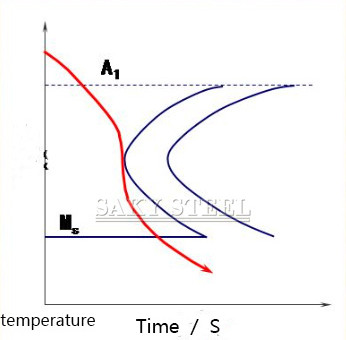
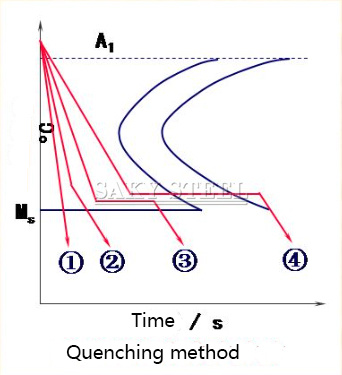
5. Metode și caracteristici ale acestora:
① Schema simplă: ușor de operat și potrivit pentru piese de lucru mici, în formă simplă. Microstructura rezultată este martensita (M).
② Scheching Double: mai complex și dificil de controlat, utilizat pentru oțel cu conținut ridicat de carbon în formă de complex și piese de lucru din oțel din aliaj mai mare. Microstructura rezultată este martensita (M).
③ Scheching: un proces mai complex, utilizat pentru piese de oțel din aliaj în formă complexă, în formă complexă. Microstructura rezultată este martensita (M).
④ Quanching: utilizat pentru piese mici, în formă de complex, cu cerințe ridicate. Microstructura rezultată este bainitul inferior (B).
6. Factorii care afectează întărirea
Nivelul de întărire depinde de stabilitatea austenitei supercoolate din oțel. Cu cât este mai mare stabilitatea austenitei supercoolate, cu atât este mai bună întărirea și invers.
Factori care influențează stabilitatea austenitei supercoolate:
Poziția curbei C: Dacă curba C se deplasează spre dreapta, rata critică de răcire pentru stingerea scade, îmbunătățind întărirea.
Concluzie cheie:
Orice factor care mută curba C la dreapta crește întărirea oțelului.
Factorul principal:
Compoziție chimică: cu excepția cobaltului (CO), toate elementele de aliere dizolvate în austenită cresc întărirea.
Cu cât conținutul de carbon este mai aproape de compoziția eutectoidă din oțelul carbon, cu atât curba C se deplasează spre dreapta și cu atât este mai mare întărirea.
7. Determinarea și reprezentarea întăririi
Test Test de întărire a stingerii: întărirea se măsoară folosind metoda testului final.
② Metoda diametrului de stingere a criticalului: diametrul critic de stingere (D₀) reprezintă diametrul maxim de oțel care poate fi întărit complet într -un mediu de stingere specific.
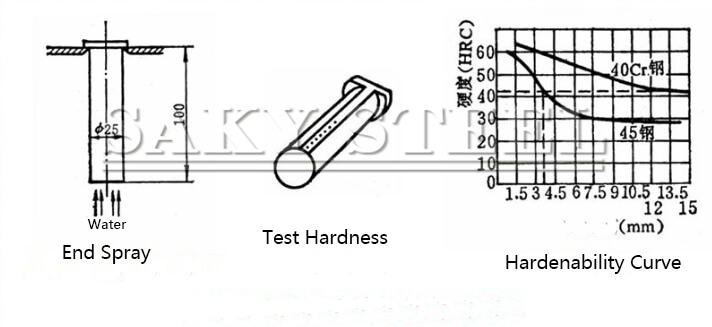
B.Tempering
1. Definiția temperamentului
Temperarea este un proces de tratare termică în care oțelul stins este reîncălzit la o temperatură sub punctul A₁, menținut la acea temperatură, apoi răcit la temperatura camerei.
2. Scopul temperamentului
Reduceți sau eliminați stresul rezidual: previne deformarea sau fisurarea piesei.
Reduceți sau eliminați austenita reziduală: stabilizați dimensiunile piesei de lucru.
Eliminați fragilitatea oțelului stins: Reglați microstructura și proprietățile pentru a satisface cerințele piesei.
Notă importantă: Oțelul trebuie temperat prompt după stingere.
3. Procesele de temperament
1. Temperating
Scop: reducerea stresului de stingere, îmbunătățirea durității piesei de lucru și obținerea rezistenței ridicate la duritate și uzură.
Temperatură: 150 ° C ~ 250 ° C.
Performanță: Duritate: HRC 58 ~ 64. Duritate ridicată și rezistență la uzură.
Aplicații: instrumente, matrițe, rulmenți, piese carburizate și componente întărite la suprafață.
2. Temperatura înaltă
Scop: pentru a obține o duritate ridicată, împreună cu o forță și duritate suficientă.
Temperatură: 500 ° C ~ 600 ° C.
Performanță: Duritate: HRC 25 ~ 35. Proprietăți mecanice generale bune.
Aplicații: arbori, angrenaje, tije de conectare etc.
Rafinare termică
Definiție: stingerea urmată de temperatura la temperaturi ridicate se numește rafinare termică sau pur și simplu temperarea. Oțelul tratat de acest proces are performanțe generale excelente și este utilizat pe scară largă.
Ⅳ.Surface Tratarea termică a oțelului
A. stingerea unei oțeluri
1. Definiția întăririi suprafeței
Întărirea suprafeței este un proces de tratare termică conceput pentru a consolida stratul de suprafață al unei piese de lucru prin încălzirea rapidă a acestuia pentru a transforma stratul de suprafață în austenită și apoi răcirea rapidă a acestuia. Acest proces este realizat fără a modifica compoziția chimică a oțelului sau structura de bază a materialului.
2. Materiale utilizate pentru întărirea suprafeței și structura post-întărire
Materiale utilizate pentru întărirea suprafeței
Materiale tipice: oțel cu carbon mediu și oțel din aliaj de carbon mediu.
Pre-tratament: proces tipic: temperare. Dacă proprietățile de bază nu sunt critice, normalizarea poate fi utilizată în schimb.
Structura post-întărire
Structura suprafeței: stratul de suprafață formează de obicei o structură întărită, cum ar fi martensita sau bainitul, care asigură o rezistență ridicată și rezistență la uzură.
Structura miezului: miezul oțelului își păstrează în general structura inițială, cum ar fi perla sau starea temperată, în funcție de procesul de pre-tratament și de proprietățile materialului de bază. Acest lucru asigură că miezul menține o rezistență și o forță bună.
B.Caracteristicile întăririi suprafeței inducției
1. Temperatura de încălzire înaltă și creșterea rapidă a temperaturii: întărirea suprafeței de inducție implică de obicei temperaturi ridicate de încălzire și rate de încălzire rapidă, permițând încălzirea rapidă într -un timp scurt.
2. Structura de cereale austenite în stratul de suprafață: în timpul încălzirii rapide și procesului de stingere ulterioară, stratul de suprafață formează boabe fine austenite. După stingere, suprafața constă în primul rând din martensită fină, cu duritate de obicei cu 2-3 HRC mai mare decât stingerea convențională.
3. Calitatea bună a suprafeței: Datorită timpului scurt de încălzire, suprafața piesei de prelucrat este mai puțin predispusă la oxidare și decarburizare, iar deformarea indusă de stingere este minimizată, asigurând o calitate bună a suprafeței.
4. Puterea de oboseală înaltă: Transformarea fazei martensitice în stratul de suprafață generează stres compresiv, ceea ce crește rezistența la oboseală a piesei de lucru.
5. Eficiența de producție înaltă: Întărirea suprafeței de inducție este potrivită pentru producția în masă, oferind o eficiență operațională ridicată.
C.Clasificarea tratamentului termic chimic
Carburizare, carburizare, carburizare, cromizare, siliconizare, siliconizare, siliconizare, carbonitridă, borocarburizare
D.GAS carburizare
Carburizarea gazelor este un proces în care o piesă de lucru este plasată într -un cuptor de carburizare a gazelor sigilate și încălzit la o temperatură care transformă oțelul în austenită. Apoi, un agent de carburizare este picurat în cuptor sau este introdusă direct o atmosferă de carburizare, permițând atomilor de carbon să se difuzeze în stratul de suprafață al piesei de lucru. Acest proces crește conținutul de carbon (WC%) pe suprafața piesei de prelucrat.
√ agenții de carburizare:
• Gaze bogate în carbon: cum ar fi gaze de cărbune, gaze petroliere lichefiate (GPL), etc.
• Lichide organice: cum ar fi kerosenul, metanolul, benzenul etc.
√ Carburizarea parametrilor procesului:
• Temperatura de carburizare: 920 ~ 950 ° C.
• Timpul de carburizare: depinde de adâncimea dorită a stratului carburizat și de temperatura de carburizare.
E.Latare tratament după carburizare
Oțelul trebuie să fie supus unui tratament termic după carburizare.
Procesul de tratare termică după carburizare:
√quenching + temperatură scăzută la temperatură
1. STUPNEREA DIRECTĂ DUPĂ ÎNCĂRCAREA PRE-ROOLING + TIMPERAREA LIMBĂTORULUI SĂMÂNT: Piesa de prelucrat este răcită în prealabil de la temperatura de carburizare până la peste temperatura AR₁ a miezului și apoi stinsă imediat, urmată de temperatura la temperaturi scăzute la 160 ~ 180 ° C.
2. Strângerea de stingere după pre-răcire + temperatură scăzută la temperatură: după carburizare, piesa de prelucrat este răcită lent la temperatura camerei, apoi reîncălzită pentru stingere și temperatură scăzută la temperatură.
3. Împiedicarea dublă după pre-răcire + temperatură scăzută la temperatură: după carburizare și răcire lentă, piesa de prelucrat suferă două etape de încălzire și stingere, urmată de temperare scăzută la temperatură.
Ⅴ. Tratarea termică a oțelilor
1. Refinirea tratamentului termic chimic
Tratamentul termic chimic este un proces de tratare termică în care o piesă de lucru din oțel este plasată într -un mediu activ specific, încălzit și menținut la temperatură, permițând atomilor activi în mediu să se difuzeze pe suprafața piesei de lucru. Acest lucru schimbă compoziția chimică și microstructura suprafeței piesei de lucru, modificând astfel proprietățile sale.
2. Procesul bazic de tratament termic chimic
Descompunerea: în timpul încălzirii, mediul activ se descompune, eliberând atomi activi.
Absorbție: atomii activi sunt adsorbiți de suprafața oțelului și se dizolvă în soluția solidă a oțelului.
Difuzie: atomii activi absorbiți și dizolvați pe suprafața oțelului migrează în interior.
Tipuri de întărire a suprafeței de inducție
A. Încălzire cu inducție cu frecvență înaltă
Frecvența curentă: 250 ~ 300 kHz.
Adâncimea stratului întărit: 0,5 ~ 2,0 mm.
Aplicații: angrenaje de modul mediu și mici și arbori de dimensiuni mici și medii.
încălzire cu inducție de frecvență b.Medium
Frecvența curentă: 2500 ~ 8000 kHz.
Adâncimea stratului întărit: 2 ~ 10 mm.
Aplicații: arbori mai mari și viteze mari până la medii.
C. Încălzire cu inducție de frecvență
Frecvența curentă: 50 Hz.
Adâncimea stratului întărit: 10 ~ 15 mm.
Aplicații: piese de lucru care necesită un strat foarte profund întărit.
3. Întărirea suprafeței inducției
Principiul de bază al întăririi suprafeței inducției
Efectul pielii:
Atunci când curentul alternativ în bobina de inducție induce un curent pe suprafața piesei de prelucrat, majoritatea curentului indus este concentrat aproape de suprafață, în timp ce aproape niciun curent nu trece prin interiorul piesei de lucru. Acest fenomen este cunoscut sub numele de efectul pielii.
Principiul întăririi suprafeței de inducție:
Pe baza efectului pielii, suprafața piesei de lucru este încălzită rapid până la temperatura de austenitizare (crescând la 800 ~ 1000 ° C în câteva secunde), în timp ce interiorul piesei de lucru rămâne aproape neîncălzit. Piesa de prelucrat este apoi răcită prin pulverizarea apei, obținând întărirea suprafeței.
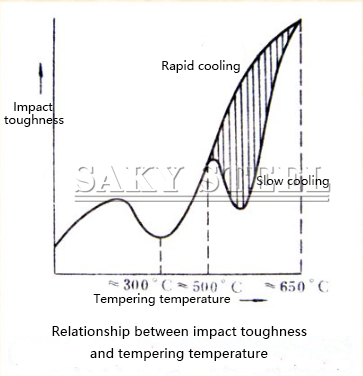
4. Grățire
Temperamentul fragmentului în oțel stins
Temperating Brittleness se referă la fenomenul în care rezistența la impact a oțelului stins scade semnificativ atunci când este temperat la anumite temperaturi.
Primul tip de tărie temperatură
Interval de temperatură: 250 ° C până la 350 ° C.
Caracteristici: Dacă oțelul stins este temperat în acest interval de temperatură, este foarte probabil să dezvolte acest tip de fragilitate temperată, care nu poate fi eliminată.
Soluție: Evitați temperarea oțelului stins în acest interval de temperatură.
Primul tip de tărie temperatură este, de asemenea, cunoscut sub numele de fragilitate temperatură scăzută sau de temperament ireversibil.
Ⅵ.Tempering
1. Temperarea este un proces final de tratare a căldurii care urmează stingerea.
De ce oțelurile stinse au nevoie de temperare?
Microstructura după stingere: După stingere, microstructura oțelului constă de obicei din martensit și austenită reziduală. Ambele sunt faze metastabile și se vor transforma în anumite condiții.
Proprietățile martensitei: martensitul se caracterizează prin duritate ridicată, dar și o fragilitate ridicată (în special în martensitul cu ac de mare carbon), care nu îndeplinește cerințele de performanță pentru multe aplicații.
Caracteristicile transformării martensitice: transformarea în martensită are loc foarte rapid. După stingere, piesa de lucru are tensiuni interne reziduale care pot duce la deformare sau fisurare.
Concluzie: Piesa de lucru nu poate fi folosită direct după stingere! Temperarea este necesară pentru a reduce tensiunile interne și pentru a îmbunătăți duritatea piesei, ceea ce o face potrivită pentru utilizare.
2. Diferența dintre întăribilitate și capacitatea de întărire:
Întăribilitate:
Întărirea se referă la capacitatea oțelului de a obține o anumită adâncime de întărire (adâncimea stratului întărit) după stingere. Depinde de compoziția și structura oțelului, în special de elementele sale de aliere și de tipul de oțel. Întărirea este o măsură a cât de bine se poate întări oțelul de -a lungul grosimii sale în timpul procesului de stingere.
Duritate (capacitate de întărire):
Duritatea sau capacitatea de întărire se referă la duritatea maximă care poate fi obținută în oțel după stingere. Este influențat în mare măsură de conținutul de carbon al oțelului. Conținutul mai mare de carbon duce, în general, la o duritate potențială mai mare, dar acest lucru poate fi limitat de elementele de aliere ale oțelului și de eficacitatea procesului de stingere.
3.Hardenabilitatea oțelului
√concept de întărire
Întărirea se referă la capacitatea oțelului de a obține o anumită adâncime de întărire martensitică după ce s -a stins de la temperatura de austenitizare. În termeni mai simpli, este capacitatea de oțel de a forma martensit în timpul stingerii.
Măsurarea întăririi
Mărimea întăririi este indicată de adâncimea stratului întărit obținut în condiții specificate după stingere.
Adâncimea stratului întărit: Aceasta este adâncimea de la suprafața piesei de prelucrat până la regiunea în care structura este pe jumătate martensită.
Media de stingere comună:
•Apă
Caracteristici: economic cu o capacitate puternică de răcire, dar are o rată de răcire ridicată în apropierea punctului de fierbere, ceea ce poate duce la răcire excesivă.
Aplicație: utilizat de obicei pentru oțelurile de carbon.
Apa sărată: o soluție de sare sau alcalin în apă, care are o capacitate de răcire mai mare la temperaturi ridicate în comparație cu apa, ceea ce o face potrivită pentru oțelurile de carbon.
•Ulei
Caracteristici: oferă o rată de răcire mai lentă la temperaturi scăzute (aproape de punctul de fierbere), ceea ce reduce efectiv tendința de deformare și fisurare, dar are o capacitate de răcire mai mică la temperaturi ridicate.
Aplicație: Potrivit pentru oțelurile din aliaj.
Tipuri: Include ulei de stingere, ulei de mașină și combustibil diesel.
Timp de încălzire
Timpul de încălzire constă atât din rata de încălzire (timpul necesar pentru a atinge temperatura dorită), cât și timpul de menținere (timpul menținut la temperatura țintă).
Principiile pentru determinarea timpului de încălzire: asigurați distribuția uniformă a temperaturii în întreaga piesă, atât în interior, cât și în exterior.
Asigurați -vă austenitizarea completă și că austenita formată este uniformă și fină.
Baza pentru determinarea timpului de încălzire: de obicei estimat folosind formule empirice sau determinate prin experimentare.
Stingerea mass -media
Două aspecte cheie:
A. Viteza de răcire: o rată de răcire mai mare promovează formarea martensitei.
B. Stresul rezidual: o rată de răcire mai mare crește stresul rezidual, ceea ce poate duce la o tendință mai mare de deformare și fisură în piesa de lucru.
Ⅶ.normalizare
1. Definiția normalizării
Normalizarea este un proces de tratare termică în care oțelul este încălzit la o temperatură de la 30 ° C până la 50 ° C deasupra temperaturii AC3, menținută la acea temperatură și apoi răcită cu aer pentru a obține o microstructură aproape de starea de echilibru. În comparație cu recoacerea, normalizarea are o rată de răcire mai rapidă, rezultând o structură mai fină a perlelor (P) și o rezistență și o duritate mai mare.
2. Scopul normalizării
Scopul normalizării este similar cu cel al recoacerii.
3. Aplicații de normalizare
• Eliminați cimentul secundar în rețea.
• Serviți ca tratament termic final pentru piese cu cerințe mai mici.
• Acționează ca un tratament termic pregătitor pentru oțel structural cu conținut scăzut și mediu de carbon pentru a îmbunătăți mașina.
4. Tipuri de recoacere
Primul tip de recoacere:
Scopul și funcția: Scopul nu este de a induce transformarea fazelor, ci de a tranziția oțelului de la o stare dezechilibrată la o stare echilibrată.
Tipuri:
• Recuperarea difuziei: își propune să omogenizeze compoziția prin eliminarea segregării.
• Recrisuri de recristalizare: restabilește ductilitatea prin eliminarea efectelor întăririi muncii.
• Recuperarea de reducere a tensiunii: reduce tensiunile interne fără a modifica microstructura.
Al doilea tip de recoacere:
Scopul și funcția: își propune să schimbe microstructura și proprietățile, obținând o microstructura dominată de perle. Acest tip asigură, de asemenea, că distribuția și morfologia perlelor, feritei și carburilor îndeplinesc cerințele specifice.
Tipuri:
• Recuperare completă: încălzește oțelul deasupra temperaturii AC3 și apoi îl răcește încet pentru a produce o structură uniformă de perle.
• Recuperare incompletă: încălzește oțelul între temperaturile AC1 și AC3 pentru a transforma parțial structura.
• Recuperare izotermă: încălzește oțelul până la AC3, urmată de răcirea rapidă la o temperatură izotermă și menținerea pentru a atinge structura dorită.
• Recuperare sferoidizantă: produce o structură de carbură sferoidă, îmbunătățind mașina și duritatea.
Ⅷ.1.definirea tratamentului termic
Tratamentul termic se referă la un proces în care metalul este încălzit, menținut la o temperatură specifică și apoi răcit în timp ce se află într -o stare solidă pentru a -și modifica structura internă și microstructura, obținând astfel proprietățile dorite.
2. Procteristici ale tratamentului termic
Tratamentul termic nu schimbă forma piesei de prelucrat; În schimb, modifică structura internă și microstructura oțelului, care la rândul său modifică proprietățile oțelului.
3. Schimbarea tratamentului termic
Scopul tratării termice este îmbunătățirea proprietăților mecanice sau de procesare ale oțelului (sau pieselor de lucru), să utilizeze pe deplin potențialul oțelului, să îmbunătățească calitatea piesei de lucru și să -și prelungească durata de viață.
4. CONCLUZIE DE SCURTĂ
Dacă proprietățile unui material pot fi îmbunătățite prin tratamentul termic depinde în mod critic de faptul că există modificări ale microstructurii și structurii sale în timpul procesului de încălzire și răcire.
Timpul post: 19-19-2024