What is a Forged Shaft?
Forged steel shaft is a cylindrical metal component made from steel that has undergone the forging process. Forging involves shaping metal using compressive forces, typically by heating it to a high temperature and then applying pressure through hammering, pressing, or rolling. This process results in a shaft with enhanced mechanical properties such as improved strength, toughness, and resistance to wear compared to shafts made from cast or machined steel.
Forged steel shafts are widely used in various industrial applications where high performance and durability are essential. Their superior mechanical properties make them ideal for use in demanding environments, such as in automotive engines, aerospace systems, and heavy machinery.A forged shaft is a vital component utilized in numerous industrial applications, renowned for its exceptional strength, durability, and toughness. This type of shaft is created through a process known as forging, in which metal is shaped by applying high-pressure forces. In this article, we will explore the key characteristics and manufacturing process of forged shafts in greater detail.
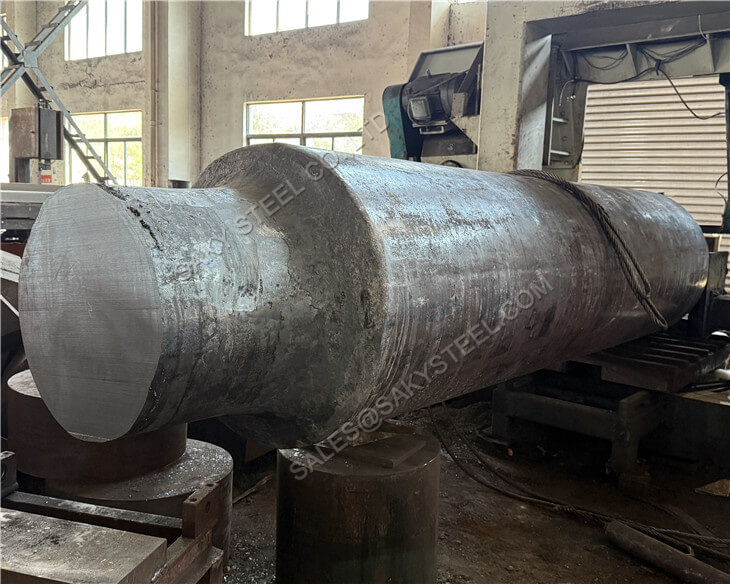
Characteristics of Forged Steel Shafts
1.Superior Strength:One of the most significant advantages of forged steel shafts is their superior strength. The forging process aligns the steel’s grain structure, making the material more compact and uniform. This results in a shaft that is more resistant to fatigue and stress, particularly under high loads and rotating conditions. Forged shafts are less likely to experience defects like porosity, which can occur in cast parts.
2.Improved Toughness:Forged steel shafts exhibit improved toughness. The forging process creates a more homogenous material with fewer internal defects, which improves its resistance to impacts, cracks, and fractures. This makes forged steel shafts suitable for applications where the component may be subject to shock or high-impact forces.
3.Increased Durability:Due to the high strength and toughness imparted during the forging process, forged steel shafts tend to last longer under wear and tear conditions. They are especially resistant to wear from friction and can maintain their integrity in harsh environments, making them ideal for rotating machinery and heavy-duty applications.
4.Fatigue Resistance:The fatigue resistance of forged steel shafts is one of their most critical features. Forging eliminates the internal voids that can weaken a part, thus reducing the risk of failure from cyclic loads. This makes forged steel shafts ideal for use in high-stress applications like drivetrain components and turbine shafts, which undergo repetitive loading during operation.
5.Corrosion Resistance:Depending on the specific alloy used in the forging process (e.g., stainless steel, alloy steel), forged steel shafts can offer excellent corrosion resistance. Steel shafts made from corrosion-resistant materials can withstand exposure to moisture, chemicals, and harsh environmental conditions, making them suitable for use in industries such as marine, chemical processing, and energy.
Types of Forged Steel Shafts
1.Hot Forged Steel Shafts
In hot forging, the steel is heated to a temperature above its recrystallization point, typically between 900°C to 1,300°C (1,650°F to 2,370°F), to allow for easy shaping. This is the most common forging method for large steel shafts, as it ensures that the material maintains strength and integrity during deformation. Hot forging is suitable for producing heavy-duty shafts used in industries such as automotive, aerospace, and construction.
2.Cold Forged Steel Shafts
Cold forging is performed at or near room temperature and typically results in a higher-strength material. The process is used for producing smaller shafts that require high dimensional accuracy, such as those used in precision machinery or in automotive components. Cold-forged shafts are often stronger and have a better surface finish compared to hot-forged shafts.
3.Isothermal Forged Steel Shafts
In isothermal forging, both the metal and the die are maintained at nearly the same temperature during the process. This method reduces thermal gradients and ensures uniform material flow, leading to better mechanical properties. Isothermal forging is particularly beneficial for high-performance alloys used in aerospace or turbine applications.
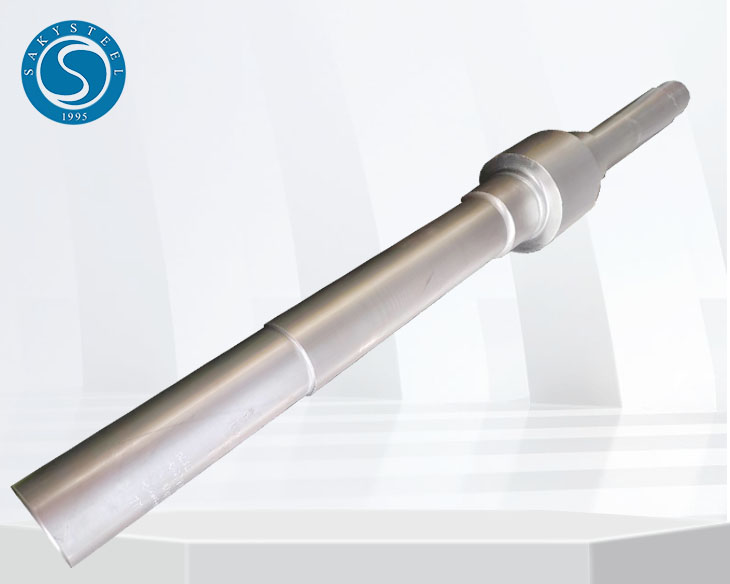
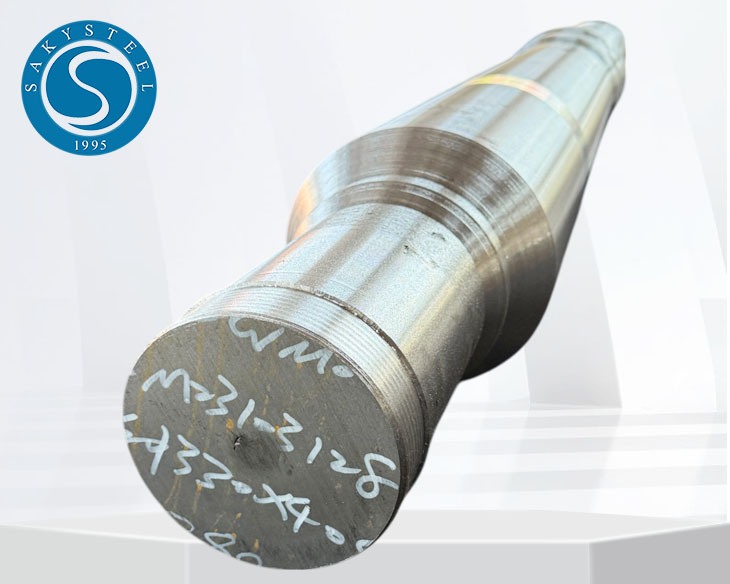
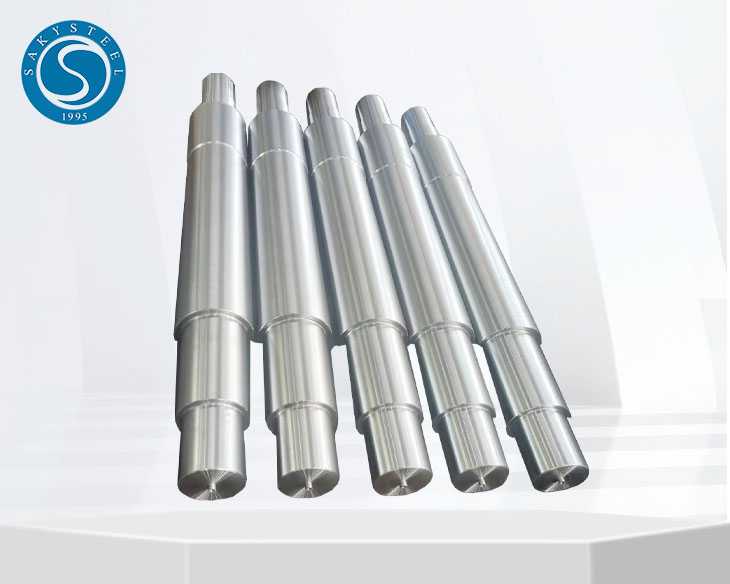
Applications of Forged Steel Shafts
1.Automotive Industry
Forged steel shafts are essential in the drivetrain, including components such as crankshafts, axles, drive shafts, and differentials.
2.Aerospace Industry
In the aerospace sector, forged steel shafts are used in turbine engines, landing gear, and other vital parts that must operate under extreme temperatures and rotational speeds.
3.Heavy Machinery
Forged steel shafts are widely used in heavy machinery for components such as gear shafts, spindles, and crankshafts.
4.Energy Sector
Forged steel shafts are used in turbines, generators, and other power generation equipment.
5.Marine Industry
Forged steel shafts are used in propeller shafts, pump shafts, and other marine components.
6.Mining and Construction
In industries like mining and construction, forged steel shafts are used in equipment such as crushers, conveyors, and excavators.
Advantages of Forged Steel Shafts Over Cast or Machined Shafts
1.Better Structural Integrity: Forging eliminates internal defects like porosity, ensuring that forged steel shafts have fewer weaknesses than cast or machined parts.
2.Higher Strength-to-Weight Ratio: Forged steel shafts are often stronger yet lighter than cast counterparts, making them more efficient in high-performance applications.
3.Improved Fatigue and Wear Resistance: The forging process aligns the material’s grain structure, which enhances the shaft's ability to withstand repetitive loads and resistance to wear from friction.
4.Cost-Efficiency: Forged steel shafts require less material wastage compared to casting, which can lead to cost savings in high-volume production.
Post time: Dec-11-2024