1. Surface scale marks
Main features: Improper processing of die forgings will cause rough surfaces and fish scale marks. Such rough fish scale marks are easily produced when forging austenitic and martensitic stainless steel.
Cause: Local mucous membrane caused by uneven lubrication or improper lubrication selection and poor quality of lubricating oil.
2. Error defects
Main features: The upper part of the die forging is misaligned relative to the lower part along the parting surface.
Cause: There is no balanced misalignment lock on the forging die, or the die forging is not installed correctly, or the gap between the hammer head and the guide rail is too large.
3. Insufficient die forging defects
Main features: The size of the die forging increases in the direction perpendicular to the parting surface. When the size exceeds the size specified in the drawing, insufficient die forging will occur.
Cause: Large size, low forging temperature, excessive wear of the die cavity, etc. will lead to insufficient pressure or excessive resistance of the flash bridge, insufficient equipment tonnage, and excessive billet volume.
4. Insufficient local filling
Main features: It mainly occurs in the ribs, convex dead corners, etc. of the die forgings, and the top of the filling part or the corners of the forgings are not filled enough, making the outline of the forgings unclear
Reason: The design of the preforming die cavity and the blanking die cavity is unreasonable, the equipment tonnage is small, the blank is not heated enough, and the metal fluidity is poor, which may cause this defect.
5. Casting structure residue
Main features: If there is residual casting structure, the elongation and fatigue strength of the forgings are often unqualified. Because on the low-magnification test piece, the streamlines of the blocked part of the residual casting are not obvious, and even dendritic products can be seen, which mainly appear in forgings using steel ingots as blanks.
Reason: Due to insufficient forging ratio or improper forging method. This defect reduces the performance of the forgings, especially the impact toughness and fatigue properties.
6. Grain inhomogeneity
Main features: The grains in some parts of the forgings are particularly coarse, while the grains in other parts are smaller, forming uneven grains. High-temperature alloys and heat-resistant steels are particularly sensitive to grain inhomogeneity.
Cause: The low final forging temperature causes local work hardening of the high-temperature alloy billet. During the quenching and heating process, some grains grow severely or the initial forging temperature is too high, and the deformation is insufficient, causing the deformation degree of the local area to fall into critical deformation. The unevenness of the grains can easily lead to a decrease in fatigue performance and durability.
7. Folding defects
Main features: The streamlines are bent at the folds of the low-magnification specimen, and the folds are similar in appearance to the cracks. If it is a crack, the streamlines will be cut twice. On the high-magnification specimen, unlike the bottom of the crack, the two sides are severely oxidized and the fold bottom is blunt.
Cause: It is mainly caused by too little feed, too much reduction or too small anvil fillet radius during the drawing process of rod forgings and crankshaft forgings. Folding defects cause the oxidized surface metal to fuse together during the forging process.
8. Improper forging streamline distribution
Main features: Streamline turbulence such as streamline reflux, eddy current, disconnection, and convection occurs when the forging is low power.
Cause: Improper die design, improper selection of forging method, unreasonable shape and billet size.
9. Banded structure
Main features: A structure in which other structures or ferrite phases in forgings are distributed in bands. It mainly exists in austenitic-ferritic stainless steel, semi-martensitic steel and eutectoid steel.
Cause: This is caused by forging deformation when two sets of parts coexist. It reduces the transverse plasticity index of the material and is prone to cracking along the ferrite zone or the boundary between the two phases.
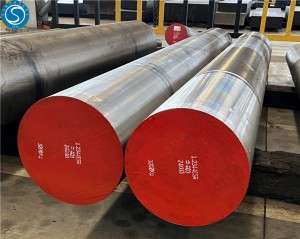
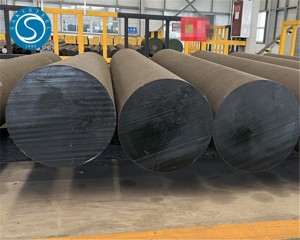

Post time: Jun-13-2024