Ⅰ.The basic concept of heat treatment.
A.The basic concept of heat treatment.
The basic elements and functions of heat treatment:
1.Heating
The purpose is to obtain a uniform and fine austenite structure.
2.Holding
The goal is to ensure the workpiece is thoroughly heated and to prevent decarburization and oxidation.
3.Cooling
The objective is to transform austenite into different microstructures.
Microstructures after Heat Treatment
During the cooling process after heating and holding, the austenite transforms into different microstructures depending on the cooling rate. Different microstructures exhibit different properties.
B.The basic concept of heat treatment.
Classification Based on Heating and Cooling Methods, as well as the Microstructure and Properties of Steel
1.Conventional Heat Treatment (Overall Heat Treatment):Tempering,Annealing,Normalizing,Quenching
2.Surface Heat Treatment:Surface Quenching,Induction Heating Surface Quenching,Flame Heating Surface Quenching,Electrical Contact Heating Surface Quenching.
3.Chemical Heat Treatment:Carburizing,Nitriding,Carbonitriding.
4.Other Heat Treatments:Controlled Atmosphere Heat Treatment,Vacuum Heat Treatment,Deformation Heat Treatment.
C.Critical Temperature of Steels
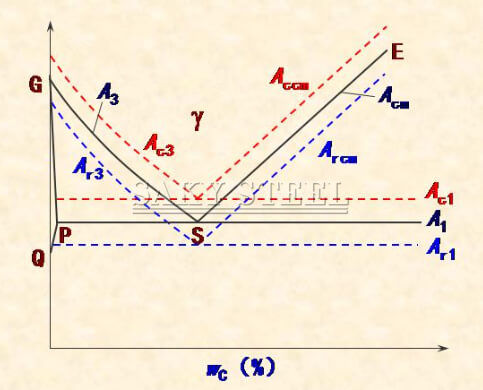
The critical transformation temperature of steel is an important basis for determining the heating, holding, and cooling processes during heat treatment. It is determined by the iron-carbon phase diagram.
Key Conclusion: The actual critical transformation temperature of steel always lags behind the theoretical critical transformation temperature. This means that overheating is required during heating, and undercooling is necessary during cooling.
Ⅱ.Annealing and Normalizing of Steel
1. Definition of Annealing
Annealing involves heating steel to a temperature above or below the critical point Ac₁ holding it at that temperature, and then slowly cooling it, usually within the furnace, to achieve a structure close to equilibrium.
2. Purpose of Annealing
①Adjust Hardness for Machining: Achieving machinable hardness in the range of HB170~230.
②Relieve Residual Stress: Prevents deformation or cracking during subsequent processes.
③Refine Grain Structure: Improves the microstructure.
④Preparation for Final Heat Treatment: Obtains granular (spheroidized) pearlite for subsequent quenching and tempering.
3.Spheroidizing Annealing
Process Specifications: Heating temperature is near the Ac₁ point.
Purpose: To spheroidize the cementite or carbides in the steel, resulting in granular (spheroidized) pearlite.
Applicable Range: Used for steels with eutectoid and hypereutectoid compositions.
4.Diffusing Annealing (Homogenizing Annealing)
Process Specifications: Heating temperature is slightly below the solvus line on the phase diagram.
Purpose: To eliminate segregation.
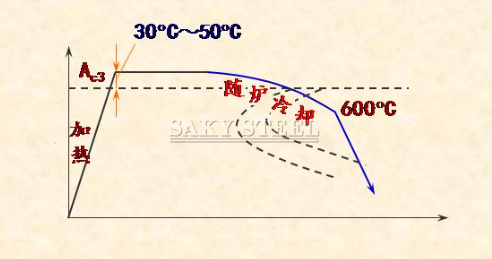
①For low-carbon steel with carbon content less than 0.25%, normalizing is preferred over annealing as a preparatory heat treatment.
②For medium-carbon steel with carbon content between 0.25% and 0.50%, either annealing or normalizing can be used as preparatory heat treatment.
③For medium- to high-carbon steel with carbon content between 0.50% and 0.75%, full annealing is recommended.
④For high-carbon steel with carbon content greater than 0.75%, normalizing is first used to eliminate the network Fe₃C, followed by spheroidizing annealing.
Ⅲ.Quenching and Tempering of Steel
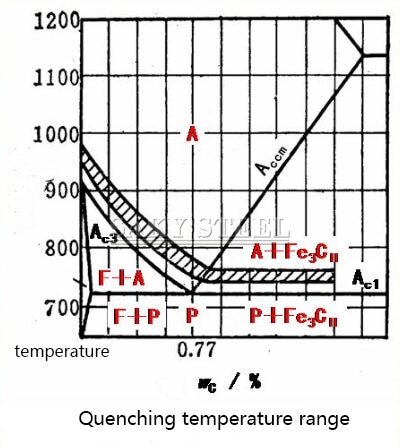
A.Quenching
1. Definition of Quenching: Quenching involves heating steel to a certain temperature above the Ac₃ or Ac₁ point, holding it at that temperature, and then cooling it at a rate greater than the critical cooling rate to form martensite.
2. Purpose of Quenching: The primary goal is to obtain martensite (or sometimes lower bainite) to increase the hardness and wear resistance of the steel. Quenching is one of the most important heat treatment processes for steel.
3.Determining Quenching Temperatures for Different Types of Steel
Hypoeutectoid Steel: Ac₃ + 30°C to 50°C
Eutectoid and Hypereutectoid Steel: Ac₁ + 30°C to 50°C
Alloy Steel: 50°C to 100°C above the critical temperature
4.Cooling Characteristics of an Ideal Quenching Medium:
Slow Cooling Before "Nose" Temperature: To sufficiently reduce thermal stress.
High Cooling Capacity Near "Nose" Temperature: To avoid the formation of non-martensitic structures.
Slow Cooling Near M₅ Point: To minimize the stress induced by martensitic transformation.
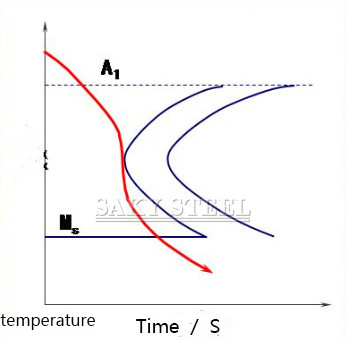

5.Quenching Methods and Their Characteristics:
①Simple Quenching: Easy to operate and suitable for small, simple-shaped workpieces. The resulting microstructure is martensite (M).
②Double Quenching: More complex and difficult to control, used for complex-shaped high-carbon steel and larger alloy steel workpieces. The resulting microstructure is martensite (M).
③Broken Quenching: A more complex process, used for large, complex-shaped alloy steel workpieces. The resulting microstructure is martensite (M).
④Isothermal Quenching: Used for small, complex-shaped workpieces with high requirements. The resulting microstructure is lower bainite (B).
6.Factors Affecting Hardenability
The level of hardenability depends on the stability of the supercooled austenite in steel. The higher the stability of the supercooled austenite, the better the hardenability, and vice versa.
Factors Influencing the Stability of Supercooled Austenite:
Position of the C-Curve: If the C-curve shifts to the right, the critical cooling rate for quenching decreases, improving hardenability.
Key Conclusion:
Any factor that shifts the C-curve to the right increases the steel's hardenability.
Main Factor:
Chemical Composition: Except for cobalt (Co), all alloying elements dissolved in austenite increase hardenability.
The closer the carbon content is to the eutectoid composition in carbon steel, the more the C-curve shifts to the right, and the higher the hardenability.
7.Determination and Representation of Hardenability
①End Quench Hardenability Test: Hardenability is measured using the end-quench test method.
②Critical Quench Diameter Method: The critical quench diameter (D₀) represents the maximum diameter of steel that can be fully hardened in a specific quenching medium.
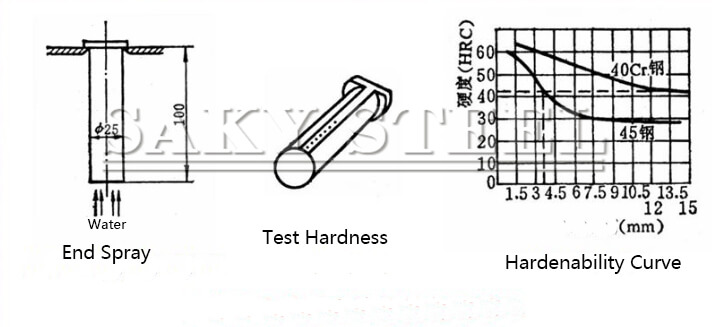
B.Tempering
1. Definition of Tempering
Tempering is a heat treatment process where quenched steel is reheated to a temperature below the A₁ point, held at that temperature, and then cooled to room temperature.
2. Purpose of Tempering
Reduce or Eliminate Residual Stress: Prevents deformation or cracking of the workpiece.
Reduce or Eliminate Residual Austenite: Stabilizes the dimensions of the workpiece.
Eliminate Brittleness of Quenched Steel: Adjusts the microstructure and properties to meet the workpiece’s requirements.
Important Note: Steel should be tempered promptly after quenching.
3.Tempering Processes
1.Low Tempering
Purpose: To reduce quenching stress, improve the toughness of the workpiece, and achieve high hardness and wear resistance.
Temperature: 150°C ~ 250°C.
Performance: Hardness: HRC 58 ~ 64. High hardness and wear resistance.
Applications: Tools, molds, bearings, carburized parts, and surface-hardened components.
2.High Tempering
Purpose: To achieve high toughness along with sufficient strength and hardness.
Temperature: 500°C ~ 600°C.
Performance: Hardness: HRC 25 ~ 35. Good overall mechanical properties.
Applications: Shafts, gears, connecting rods, etc.
Thermal Refining
Definition: Quenching followed by high-temperature tempering is called thermal refining, or simply tempering. Steel treated by this process has excellent overall performance and is widely used.
Ⅳ.Surface Heat Treatment of Steel
A.Surface Quenching of Steels
1. Definition of Surface Hardening
Surface hardening is a heat treatment process designed to strengthen the surface layer of a workpiece by rapidly heating it to transform the surface layer into austenite and then quickly cooling it. This process is carried out without altering the steel's chemical composition or the core structure of the material.
2. Materials Used for Surface Hardening and Post-Hardening Structure
Materials Used for Surface Hardening
Typical Materials: Medium carbon steel and medium carbon alloy steel.
Pre-Treatment:Typical Process: Tempering. If the core properties are not critical, normalizing can be used instead.
Post-Hardening Structure
Surface Structure: The surface layer typically forms a hardened structure such as martensite or bainite, which provides high hardness and wear resistance.
Core Structure: The core of the steel generally retains its original structure, such as pearlite or tempered state, depending on the pre-treatment process and the properties of the base material. This ensures that the core maintains good toughness and strength.
B.Characteristics of induction surface hardening
1.High Heating Temperature and Rapid Temperature Rise: Induction surface hardening typically involves high heating temperatures and rapid heating rates, allowing for quick heating within a short time.
2.Fine Austenite Grain Structure in the Surface Layer: During the rapid heating and subsequent quenching process, the surface layer forms fine austenite grains. After quenching, the surface primarily consists of fine martensite, with hardness typically 2-3 HRC higher than conventional quenching.
3.Good Surface Quality: Due to the short heating time, the workpiece surface is less prone to oxidation and decarburization, and quenching-induced deformation is minimized, ensuring good surface quality.
4.High Fatigue Strength: The martensitic phase transformation in the surface layer generates compressive stress, which increases the fatigue strength of the workpiece.
5.High Production Efficiency: Induction surface hardening is suitable for mass production, offering high operational efficiency.
C.Classification of chemical heat treatment
Carburizing,Carburizing,Carburizing,Chromizing,Siliconizing,Siliconizing,Siliconizing,Carbonitriding,Borocarburizing
D.Gas Carburizing
Gas Carburizing is a process where a workpiece is placed in a sealed gas carburizing furnace and heated to a temperature that transforms the steel into austenite. Then, a carburizing agent is dripped into the furnace, or a carburizing atmosphere is directly introduced, allowing carbon atoms to diffuse into the surface layer of the workpiece. This process increases the carbon content (wc%) on the workpiece surface.
√Carburizing Agents:
•Carbon-rich Gases: Such as coal gas, liquefied petroleum gas (LPG), etc.
•Organic Liquids: Such as kerosene, methanol, benzene, etc.
√Carburizing Process Parameters:
•Carburizing Temperature: 920~950°C.
•Carburizing Time: Depends on the desired depth of the carburized layer and the carburizing temperature.
E.Heat Treatment After Carburizing
Steel must undergo heat treatment after carburizing.
Heat Treatment Process After Carburizing:
√Quenching + Low-Temperature Tempering
1.Direct Quenching After Pre-Cooling + Low-Temperature Tempering: The workpiece is pre-cooled from the carburizing temperature to just above the core's Ar₁ temperature and then immediately quenched, followed by low-temperature tempering at 160~180°C.
2.Single Quenching After Pre-Cooling + Low-Temperature Tempering: After carburizing, the workpiece is slowly cooled to room temperature, then reheated for quenching and low-temperature tempering.
3.Double Quenching After Pre-Cooling + Low-Temperature Tempering: After carburizing and slow cooling, the workpiece undergoes two stages of heating and quenching, followed by low-temperature tempering.
Ⅴ.Chemical Heat Treatment of Steels
1.Definition of Chemical Heat Treatment
Chemical heat treatment is a heat treatment process in which a steel workpiece is placed in a specific active medium, heated, and held at temperature, allowing the active atoms in the medium to diffuse into the surface of the workpiece. This changes the chemical composition and microstructure of the workpiece's surface, thereby altering its properties.
2.Basic Process of Chemical Heat Treatment
Decomposition: During heating, the active medium decomposes, releasing active atoms.
Absorption: The active atoms are adsorbed by the surface of the steel and dissolve into the solid solution of the steel.
Diffusion: The active atoms absorbed and dissolved on the surface of the steel migrate into the interior.
Types of Induction Surface Hardening
a.High-Frequency Induction Heating
Current Frequency: 250~300 kHz.
Hardened Layer Depth: 0.5~2.0 mm.
Applications: Medium and small module gears and small to medium-sized shafts.
b.Medium-Frequency Induction Heating
Current Frequency: 2500~8000 kHz.
Hardened Layer Depth: 2~10 mm.
Applications: Larger shafts and large to medium module gears.
c.Power-Frequency Induction Heating
Current Frequency: 50 Hz.
Hardened Layer Depth: 10~15 mm.
Applications: Workpieces requiring a very deep hardened layer.
3. Induction Surface Hardening
Basic Principle of Induction Surface Hardening
Skin Effect:
When alternating current in the induction coil induces a current on the surface of the workpiece, the majority of the induced current is concentrated near the surface, while almost no current passes through the interior of the workpiece. This phenomenon is known as the skin effect.
Principle of Induction Surface Hardening:
Based on the skin effect, the surface of the workpiece is rapidly heated to the austenitizing temperature (rising to 800~1000°C in a few seconds), while the interior of the workpiece remains almost unheated. The workpiece is then cooled by water spraying, achieving surface hardening.
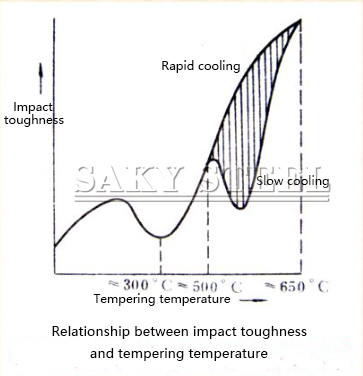
4.Temper Brittleness
Tempering Brittleness in Quenched Steel
Tempering brittleness refers to the phenomenon where the impact toughness of quenched steel significantly decreases when tempered at certain temperatures.
First Type of Tempering Brittleness
Temperature Range: 250°C to 350°C.
Characteristics: If quenched steel is tempered within this temperature range, it is highly likely to develop this type of tempering brittleness, which cannot be eliminated.
Solution: Avoid tempering quenched steel within this temperature range.
The first type of tempering brittleness is also known as low-temperature tempering brittleness or irreversible tempering brittleness.
Ⅵ.Tempering
1.Tempering is a final heat treatment process that follows quenching.
Why Do Quenched Steels Need Tempering?
Microstructure After Quenching:After quenching, the microstructure of steel typically consists of martensite and residual austenite. Both are metastable phases and will transform under certain conditions.
Properties of Martensite:Martensite is characterized by high hardness but also high brittleness (especially in high-carbon needle-like martensite), which does not meet the performance requirements for many applications.
Characteristics of Martensitic Transformation:The transformation to martensite occurs very rapidly. After quenching, the workpiece has residual internal stresses that can lead to deformation or cracking.
Conclusion:The workpiece cannot be used directly after quenching! Tempering is necessary to reduce internal stresses and improve the toughness of the workpiece, making it suitable for use.
2.Difference Between Hardenability and Hardening Capacity:
Hardenability :
Hardenability refers to the ability of steel to achieve a certain depth of hardening (the depth of the hardened layer) after quenching. It depends on the steel's composition and structure, particularly its alloying elements and the type of steel. Hardenability is a measure of how well the steel can harden throughout its thickness during the quenching process.
Hardness (Hardening Capacity):
Hardness, or hardening capacity, refers to the maximum hardness that can be achieved in the steel after quenching. It is largely influenced by the carbon content of the steel. Higher carbon content generally leads to higher potential hardness, but this can be limited by the steel's alloying elements and the effectiveness of the quenching process.
3.Hardenability of Steel
√Concept of Hardenability
Hardenability refers to the ability of steel to achieve a certain depth of martensitic hardening after quenching from the austenitizing temperature. In simpler terms, it is the capability of steel to form martensite during quenching.
Measurement of Hardenability
The size of hardenability is indicated by the depth of the hardened layer obtained under specified conditions after quenching.
Hardened Layer Depth: This is the depth from the surface of the workpiece to the region where the structure is half martensite.
Common Quenching Media:
•Water
Characteristics: Economical with strong cooling capability, but has a high cooling rate near the boiling point, which can lead to excessive cooling.
Application: Typically used for carbon steels.
Salt Water: A solution of salt or alkali in water, which has a higher cooling capacity at high temperatures compared to water, making it suitable for carbon steels.
•Oil
Characteristics: Provides a slower cooling rate at low temperatures (near the boiling point), which effectively reduces the tendency for deformation and cracking, but has lower cooling capability at high temperatures.
Application: Suitable for alloy steels.
Types: Includes quenching oil, machine oil, and diesel fuel.
Heating Time
Heating time consists of both the heating rate (time taken to reach the desired temperature) and the holding time (time maintained at the target temperature).
Principles for Determining Heating Time:Ensure uniform temperature distribution throughout the workpiece, both inside and outside.
Ensure complete austenitization and that the austenite formed is uniform and fine.
Basis for Determining Heating Time:Usually estimated using empirical formulas or determined through experimentation.
Quenching Media
Two Key Aspects:
a.Cooling Rate: A higher cooling rate promotes the formation of martensite.
b.Residual Stress: A higher cooling rate increases residual stress, which can lead to a greater tendency for deformation and cracking in the workpiece.
Ⅶ.Normalizing
1. Definition of Normalizing
Normalizing is a heat treatment process in which steel is heated to a temperature 30°C to 50°C above the Ac3 temperature, held at that temperature, and then air-cooled to obtain a microstructure close to the equilibrium state. Compared to annealing, normalizing has a faster cooling rate, resulting in a finer pearlite structure (P) and higher strength and hardness.
2. Purpose of Normalizing
The purpose of normalizing is similar to that of annealing.
3. Applications of Normalizing
•Eliminate networked secondary cementite.
•Serve as the final heat treatment for parts with lower requirements.
•Act as a preparatory heat treatment for low and medium carbon structural steel to improve machinability.
4.Types of Annealing
First Type of Annealing:
Purpose and Function: The goal is not to induce phase transformation but to transition the steel from an unbalanced state to a balanced state.
Types:
•Diffusion Annealing: Aims to homogenize the composition by eliminating segregation.
•Recrystallization Annealing: Restores ductility by eliminating the effects of work hardening.
•Stress Relief Annealing: Reduces internal stresses without altering the microstructure.
Second Type of Annealing:
Purpose and Function: Aims to change the microstructure and properties, achieving a pearlite-dominated microstructure. This type also ensures that the distribution and morphology of pearlite, ferrite, and carbides meet specific requirements.
Types:
•Full Annealing: Heats the steel above the Ac3 temperature and then slowly cools it to produce a uniform pearlite structure.
•Incomplete Annealing: Heats the steel between Ac1 and Ac3 temperatures to partially transform the structure.
•Isothermal Annealing: Heats the steel to above Ac3, followed by rapid cooling to an isothermal temperature and holding to achieve the desired structure.
•Spheroidizing Annealing: Produces a spheroidal carbide structure, improving machinability and toughness.
Ⅷ.1.Definition of Heat Treatment
Heat treatment refers to a process in which metal is heated, held at a specific temperature, and then cooled while in a solid state to alter its internal structure and microstructure, thereby achieving desired properties.
2.Characteristics of Heat Treatment
Heat treatment does not change the shape of the workpiece; instead, it alters the internal structure and microstructure of the steel, which in turn changes the steel's properties.
3.Purpose of Heat Treatment
The purpose of heat treatment is to improve the mechanical or processing properties of steel (or workpieces), fully utilize the potential of the steel, enhance the quality of the workpiece, and extend its service life.
4.Key Conclusion
Whether a material's properties can be improved through heat treatment depends critically on whether there are changes in its microstructure and structure during the heating and cooling process.
Post time: Aug-19-2024