Ⅰ. Основниот концепт на третман на топлина.
A. Основниот концепт на третман на топлина.
Основните елементи и функции наТоплински третман:
1. загревање
Целта е да се добие униформа и добра структура на аустенит.
2.Одржување
Целта е да се обезбеди работното парче темелно загреано и да се спречи депарбуризација и оксидација.
3.Полинг
Целта е да се претвори аустенит во различни микроструктури.
Микроструктури по термичка обработка
За време на процесот на ладење по загревањето и држењето, аустенитот се претвора во различни микроструктури во зависност од стапката на ладење. Различни микроструктури покажуваат различни својства.
Б. Основниот концепт на третман на топлина.
Класификација заснована на методи за греење и ладење, како и на микроструктурата и својствата на челикот
1. Конвенционален третман на топлина (целосен третман на топлина): Температирање, полнење, нормализирање, калење
2.Подјавување на топлина на површината: Калење на површината, калење на површината за греење, калење на површината за греење на пламен, калење на површината за греење на електричен контакт.
3. Хемиски третман на топлина: Карбуризирање, нитрирање, карбонитрирање.
4. Други третмани со топлина: Контролирана третман на топлина на атмосфера, третман на вакуумска топлина, третман на деформација на топлина.
C.критична температура на челици
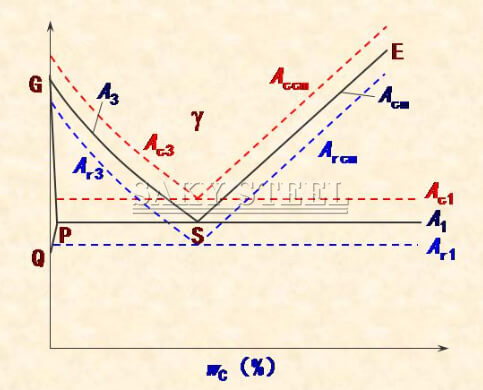
Критичната температура на трансформацијата на челикот е важна основа за одредување на процесите на греење, држење и ладење за време на третманот со топлина. Се одредува со дијаграмот на железо-јаглеродна фаза.
Клучен заклучок:Вистинската критична температура на трансформација на челик секогаш заостанува зад теоретската температура на критична трансформација. Ова значи дека е потребно прегревање за време на загревањето, а за време на ладењето е неопходно потценување.
Ⅱ.Анелинг и нормализирање на челик
1. Дефиниција на annealing
Annealing вклучува загревање на челик до температура над или под критичната точка AC₁ што го држи на таа температура, а потоа полека го лади, обично во печката, за да се постигне структура близу до рамнотежа.
2. Цел на полнење
① Подобрена цврстина за машинска обработка: Постигнување на машинска цврстина во опсег на HB170 ~ 230.
Resележи преостаната стрес: спречува деформација или пукање за време на последователните процеси.
- Рефинирана структура на жито: ја подобрува микроструктурата.
④ Подготвување за конечен третман на топлина: Добива грануларен (сфероидизиран) бисер за последователно калење и калење.
3.Сероидизирање на полнење
Спецификации на процесите: Температурата на греење е близу точката AC₁.
Цел: Да се сфероидизира цементит или карбиди во челикот, што резултира во грануларен (сфероиден) бисер.
Применлив опсег: Се користи за челици со еутектоидни и хипереутектоидни композиции.
4. Дифузирање на полнење (хомогенизирање на полнење)
Спецификации на процесите: Температурата на греење е малку под линијата на солвус на фазен дијаграм.
Цел: Да се елиминира сегрегацијата.
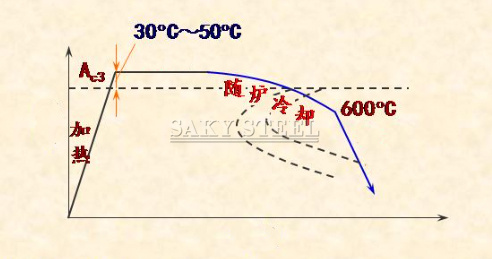
① за ниско-Јаглероден челикСо содржина на јаглерод помала од 0,25%, нормализацијата е најпосакувана над прицврстувањето како подготвителен третман на топлина.
② За средно-јаглероден челик со содржина на јаглерод помеѓу 0,25% и 0,50%, или прицврстување или нормализирање може да се користи како подготвителен третман на топлина.
③ За средно до високо-јаглероден челик со содржина на јаглерод помеѓу 0,50% и 0,75%, се препорачува целосна прицврстување.
④ за високо-Јаглероден челикСо содржина на јаглерод поголема од 0,75%, нормализацијата прво се користи за елиминирање на мрежата FE₃C, проследено со сфероидизирање на прицврстување.
Ⅲ.
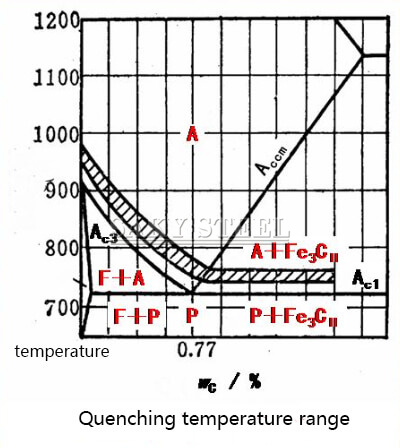
A.Quenching
1. Дефиниција на калење: Калење вклучува загревање челик на одредена температура над точката AC₃ или AC₁, држејќи го на таа температура, а потоа да се лади со брзина поголема од критичната стапка на ладење за да се формира мартинзит.
2. Цел на калење: Примарната цел е да се добие мартинзит (или понекогаш понизок баинит) за да се зголеми цврстината и отпорноста на абење на челикот. Калењето е еден од најважните процеси на третман на топлина за челик.
3. Одредување на температури на калење за различни типови челик
ХИПОЕУТЕКТИОИОТ Стил: AC₃ + 30 ° C до 50 ° C
Еутектоиден и хипереутектоиден челик: AC₁ + 30 ° C до 50 ° C
Челик од легура: 50 ° C до 100 ° C над критичната температура
4. Карактеристики на пукање на идеален медиум за калење:
Бавно ладење пред температурата на „носот“: да се намали термичкиот стрес.
Висок капацитет за ладење во близина на температурата на „носот“: да се избегне формирање на не-мартизензивни структури.
Бавно ладење во близина на M₅ Point: Да се минимизира стресот предизвикан од мартинзитичката трансформација.
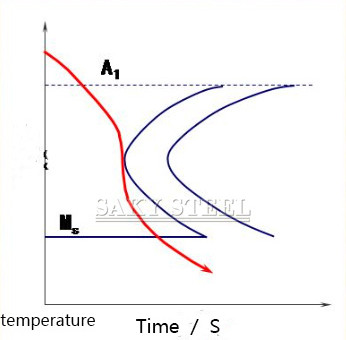
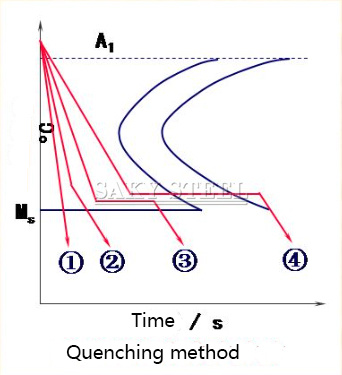
5. Методи за местење и нивните карактеристики:
-Сместено калење: Лесно се работи и погодно за мали, едноставни работни делови. Како резултат на микроструктурата е мартинзит (М).
② Думно калење: Покомплексно и тешко се контролира, се користи за комплексни облик на високо-јаглерод челик и поголеми работни парчиња од челик од легура. Како резултат на микроструктурата е мартинзит (М).
③ Брокено калење: Покомплексен процес, користен за големи, комплексни облици на легура челик. Како резултат на микроструктурата е мартинзит (М).
-Изотермално калење: Се користи за мали, сложени работни делови со високи барања. Како резултат на микроструктурата е пониска баинит (Б).
6.Фактори кои влијаат на цврстината
Нивото на цврстина зависи од стабилноста на суперкулираниот аустенит во челик. Колку е поголема стабилноста на суперкулираниот аустенит, толку е подобра цврстината и обратно.
Фактори кои влијаат на стабилноста на суперкулираниот аустенит:
Позиција на C-кривата: Ако C-кривата се префрли надесно, критичната стапка на ладење за калење се намалува, подобрувајќи ја цврстината.
Клучен заклучок:
Секој фактор што ја менува C-кривата надесно ја зголемува цврстината на челикот.
Главен фактор:
Хемиски состав: Освен кобалт (CO), сите елементи на легура растворени во аустенит ја зголемуваат зацврстуваноста.
Колку е поблизу содржината на јаглерод е до еутектоидниот состав во јаглеродниот челик, толку повеќе се менува кривата од десно, а колку е поголема цврстината.
7. Одредување и застапеност на цврстината
-Тест за зацврстување на зацврстување на гаснење: цврстината се мери со помош на методот на тест на крајниот гас.
② Ккритичен метод на дијаметар на гаснење: Критичкиот дијаметар на гаснење (D₀) претставува максимален дијаметар на челик што може целосно да се зацврсти во специфичен медиум за калење.
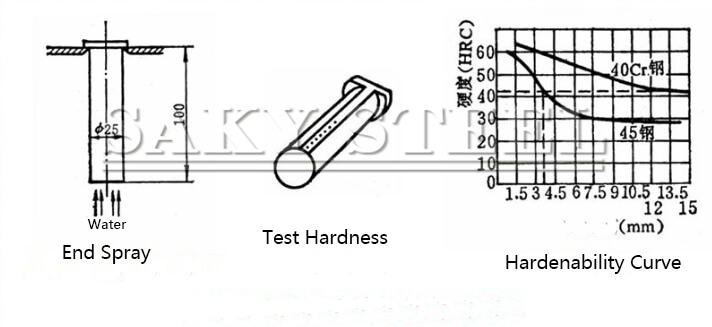
Б.Темперинг
1. Дефиниција на калење
Темперантирањето е процес на третман на топлина, каде што челичниот челик се загрева на температура под точката A₁, што се држи на таа температура, а потоа се лади на собна температура.
2 Цел на калење
Намалете го или елиминирајте го преостанатиот стрес: спречува деформација или пукање на работното парче.
Намалете или елиминирајте го преостанатиот аустенит: ги стабилизира димензиите на работното парче.
Елиминирајте ја кршливоста на калениот челик: ги прилагодува микроструктурата и својствата за да ги исполни барањата на работното парче.
Важна белешка: Челикот треба да се смири веднаш по калењето.
3. Процеси на време на работа
1. ниско калење
Цел: Да се намали стресот на калење, да се подобри цврстината на работното парче и да се постигне голема цврстина и отпорност на абење.
Температура: 150 ° C ~ 250 ° C.
Перформанси: Цврстина: HRC 58 ~ 64. Висока цврстина и отпорност на абење.
Апликации: Алатки, калапи, лежишта, карбурирани делови и компоненти зацврстени со површини.
2. високо калење
Цел: Да се постигне висока цврстина заедно со доволна сила и цврстина.
Температура: 500 ° C ~ 600 ° C.
Перформанси: Цврстина: HRC 25 ~ 35. Добри целокупни механички својства.
Апликации: Шахти, запчаници, шипки за поврзување, итн.
Термичко рафинирање
Дефиниција: Калење проследено со високо-температура на температурата се нарекува термичко рафинирање или едноставно калење. Челикот третиран од овој процес има одлични вкупни перформанси и е широко користен.
Ⅳ.
A.Surface Chainting of челици
1. Дефиниција на зацврстување на површината
Зацврстувањето на површината е процес на третман на топлина дизајниран да го зајакне површинскиот слој на работното парче со брзо загревање за да го трансформира површинскиот слој во аустенит и потоа брзо да го лади. Овој процес се спроведува без да се смени хемискиот состав на челикот или основната структура на материјалот.
2. Материјали што се користат за структура за зацврстување на површината и пост-зацврстување
Материјали што се користат за зацврстување на површината
Типични материјали: Среден јаглероден челик и средна челик од легура на јаглерод.
Пред-третман: Типичен процес: Темен. Ако основните својства не се критични, наместо тоа може да се користи нормализирање.
Структура по зацврстување
Структура на површината: Површинскиот слој обично формира зацврстена структура како што е мартинзит или баинит, кој обезбедува голема цврстина и отпорност на абење.
Основна структура: јадрото на челикот генерално ја задржува својата оригинална структура, како што е бисер или темпераментна состојба, во зависност од процесот на пред-третман и својствата на основниот материјал. Ова осигурува дека јадрото одржува добра цврстина и сила.
Б.Карктерии на стврднување на површината на индукцијата
1. Висока температура на греење и брз пораст на температурата: стврднувањето на површината на индукцијата обично вклучува високи температури на греење и брзи стапки на греење, овозможувајќи брзо загревање за кратко време.
2. Финална структура на жито од Остенит во површинскиот слој: За време на брзото загревање и последователното калење, површинскиот слој формира фини зрна од аустенит. По калењето, површината првенствено се состои од фин мартинзит, со цврстина обично 2-3 HRC повисока од конвенционалното калење.
3.Добразен квалитет на површината: Поради краткото време на греење, површината на работното парче е помалку склона кон оксидација и депарбуризација, а деформацијата предизвикана од гаснење е минимизирана, обезбедувајќи добар квалитет на површината.
4. Висока јачина на замор: Трансформацијата на мартинзитичката фаза во површинскиот слој генерира компресивен стрес, што ја зголемува јачината на замор на работното парче.
.
C.classification на хемиска термичка обработка
Карбуризирачки, карбуризирачки, карбурирачки, хромизирани, силиконизирачки, силиконизирачки, силиконизираат, карбонитрирање, борокарбуризирање
D.Gas Carburiting
Гасниот карбуризирање е процес каде што работното парче се става во запечатена печка за карбуризирана гас и се загрева на температура што го претвора челикот во аустенит. Потоа, директно се воведува агент за карбуризација во печката или директно се воведува карбуризирачка атмосфера, дозволувајќи им на јаглеродните атоми да се распрснат во површинскиот слој на работното парче. Овој процес ја зголемува содржината на јаглерод (WC%) на површината на работното парче.
√ Карбуризирачки агенти:
• Гасови богати со јаглерод: како што се гас од јаглен, течен нафтен гас (LPG), итн.
• Органски течности: како што се керозин, метанол, бензен, итн.
Paramters Carburizing Process Parameters:
• Температура на карбуризација: 920 ~ 950 ° C.
• Време на карбуризација: Зависи од посакуваната длабочина на карбурализираниот слој и карбуризирачката температура.
Третман на загревање по карбуризирање
Челикот мора да претрпи термички третман по карбуризирање.
Процес на третман на топлина по карбуризирање:
√ Квање + калење со ниска температура
1. Директни калење по пред-ладење + калење со ниска температура: Работното парче е претходно оладено од карбурирачката температура до нешто над температурата на AR₁ на јадрото и потоа веднаш се гаси, проследено со ниско-температура на температура на 160 ~ 180 ° C.
2.Сингл калење по пред-ладење + калење со ниска температура: После карбуризирање, работното парче полека се лади на собна температура, а потоа се загрева за калење и калење со ниска температура.
3. Добивање на калење по пред-ладење + калење со ниска температура: После карбуризирање и бавно ладење, работното парче се подложува на две фази на греење и калење, проследено со калење со ниска температура.
Ⅴ. Хемиски термички третман на челици
1. Дефинирање на хемиски третман на топлина
Хемиска термичка обработка е процес на третман на топлина во кој челично работно парче се става во специфичен активен медиум, загреан и се држи на температура, дозволувајќи им на активните атоми во медиумот да се дифузираат во површината на работното парче. Ова го менува хемискиот состав и микроструктурата на површината на работното парче, а со тоа ги менува неговите својства.
2. Базичен процес на хемиски третман на топлина
Распаѓање: За време на загревањето, активниот медиум се распаѓа, ослободувајќи активни атоми.
Апсорпција: Активните атоми се adsorbed од површината на челикот и се раствораат во цврстиот раствор на челикот.
Дифузија: Активните атоми апсорбирани и растворени на површината на челикот мигрираат во внатрешноста.
Видови на стврднување на површината на индукција
A. High-фреквенција индукција за греење
Тековна фреквенција: 250 ~ 300 kHz.
Длабочина на зацврстен слој: 0,5 ~ 2,0 мм.
Апликации: Средни и мали модули запчаници и мали и средни вратила.
Б.МЕДИМИУМ-ФЕККЕНЦИЈА Индукција за греење
Тековна фреквенција: 2500 ~ 8000 kHz.
Зацврстена длабочина на слојот: 2 ~ 10 mm.
Апликации: Поголеми шахти и големи и средни запчаници.
Ц.
Тековна фреквенција: 50 Hz.
Зацврстена длабочина на слојот: 10 ~ 15 мм.
Апликации: Работни парчиња за кои е потребно многу длабок зацврстен слој.
3. Индукциско зацврстување на површината
Основен принцип на стврднување на површината на индукција
Ефект на кожата:
Кога наизменичната струја во индукциската калем предизвикува струја на површината на работното парче, поголемиот дел од индуцираната струја е концентрирана во близина на површината, додека скоро ниту една струја поминува низ внатрешноста на работното парче. Овој феномен е познат како ефект на кожата.
Принцип на стврднување на површината на индукција:
Врз основа на ефектот на кожата, површината на работното парче брзо се загрева на температурата на аустенитизирање (се искачува на 800 ~ 1000 ° C за неколку секунди), додека внатрешноста на работното парче останува скоро незагреана. Работното парче потоа се лади со прскање на вода, постигнувајќи зацврстување на површината.
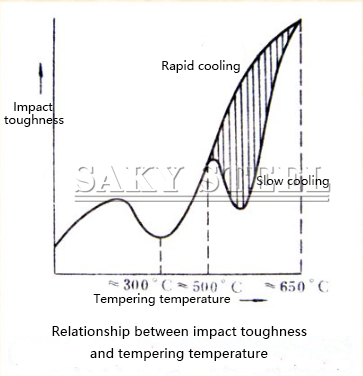
4.Temper Brittlence
Темничка кршливост во челичен челик
Темничката кршливост се однесува на феноменот каде што цврстината на влијанието на калениот челик значително се намалува кога се смирува на одредени температури.
Прв вид на умерено кршливост
Опсег на температура: 250 ° C до 350 ° C.
Карактеристики: Ако челичниот челик се смирува во овој температурен опсег, голема е веројатноста да се развие овој вид на калем на кршење, што не може да се елиминира.
Решение: Избегнувајте каленат челик со калење во овој опсег на температура.
Првиот вид на температура на температурата е исто така познат како ниска температура на температурата или неповратна температура на кршливоста.
Ⅵ.tempering
1.Теминг е конечен процес на третман на топлина што следи калење.
Зошто на чекорите на челење им е потребно умерено?
Микроструктура по калење: По калењето, микроструктурата на челик обично се состои од мартинзит и преостанат аустенит. И двете се метастабилни фази и ќе се трансформираат под одредени услови.
Својства на мартинзит: Мартинзитот се карактеризира со голема цврстина, но исто така и висока кршливост (особено кај мартинзит сличен на иглата со висока јаглерод), што не ги исполнува барањата за перформанси за многу апликации.
Карактеристики на мартинзитичката трансформација: Трансформацијата во мартинзит се јавува многу брзо. По калењето, работното парче има преостанати внатрешни стресови што можат да доведат до деформација или пукање.
Заклучок: Работното парче не може да се користи директно по калењето! Темперантирањето е неопходно за да се намалат внатрешните стресови и да се подобри цврстината на работното парче, што го прави погоден за употреба.
2.Постанок помеѓу цврстината и капацитетот на зацврстување:
Цврстина:
Зацврстеноста се однесува на можноста на челикот да постигне одредена длабочина на зацврстување (длабочината на зацврстениот слој) по калењето. Тоа зависи од составот и структурата на челикот, особено неговите легури на елементи и видот на челикот. Зацврстеноста е мерка за тоа колку добро челикот може да се зацврсти во текот на својата дебелина за време на процесот на калење.
Цврстина (капацитет на зацврстување):
Цврстината, или капацитетот на зацврстување, се однесува на максималната цврстина што може да се постигне во челикот по калењето. Во голема мерка е под влијание на содржината на јаглерод на челикот. Повисоката содржина на јаглерод генерално доведува до поголема потенцијална цврстина, но ова може да биде ограничено со легурите на челикот и ефективноста на процесот на калење.
3. Harderability на челик
√ Концепт на цврстина
Хардебилноста се однесува на можноста на челикот да постигне одредена длабочина на мартинзитичко зацврстување по калењето од аустинитационата температура. Во поедноставни термини, тоа е можност за челик да формира мартинзит за време на калењето.
Мерење на цврстината
Големината на цврстината е означена со длабочината на зацврстениот слој добиен под одредени услови по калењето.
Завртена длабочина на слојот: Ова е длабочина од површината на работното парче до регионот каде што структурата е половина мартинзит.
Вообичаени медиуми за калење:
• Вода
Карактеристики: Економичен со силна способност за ладење, но има висока стапка на ладење во близина на точката на вриење, што може да доведе до прекумерно ладење.
Апликација: Обично се користи за челици со јаглерод.
Солена вода: Раствор со сол или алкал во вода, кој има поголем капацитет за ладење на високи температури во споредба со водата, што го прави погоден за челици со јаглерод.
• Масло
Карактеристики: Овозможува побавна стапка на ладење на ниски температури (во близина на точката на вриење), што ефикасно ја намалува тенденцијата за деформација и пукање, но има помала способност за ладење на високи температури.
Апликација: Погоден за челици од легура.
Видови: Вклучува масло за калење, машинско масло и дизел гориво.
Време на греење
Времето за греење се состои и од стапката на греење (потребно време за да се достигне посакуваната температура) и времето на држење (време што се одржува на целната температура).
Принципи за утврдување на времето за греење: Обезбедете униформа дистрибуција на температурата во текот на работното парче, и внатре и надвор.
Обезбедете целосна аустенитизација и дека формираниот аустенит е униформа и добро.
Основа за утврдување на времето за греење: Обично се проценува со употреба на емпириски формули или утврдени преку експериментирање.
Калење медиуми
Два клучни аспекти:
A. Cooling стапка: Повисока стапка на ладење промовира формирање на мартинзит.
Б. Резидуален стрес: Повисока стапка на ладење го зголемува преостанатиот стрес, што може да доведе до поголема тенденција за деформација и пукање во работното парче.
Ⅶ.normalizing
1. Дефиниција на нормализирање
Нормализацијата е процес на третман на топлина во кој челикот се загрева на температура од 30 ° C до 50 ° C над температурата AC3, што се одржува на таа температура, а потоа и ладење на воздухот за да се добие микроструктура близу до состојбата на рамнотежата. Во споредба со annealing, нормализацијата има побрза стапка на ладење, што резултира во пофина структура на бисер (P) и поголема јачина и цврстина.
2 Цел на нормализирање
Целта на нормализирање е слична на онаа на annealing.
3. Апликации за нормализирање
• Елиминирајте го мрежниот секундарен цементит.
• Послужете како последен третман на топлина за делови со пониски барања.
• Дејствува како подготвителна термичка обработка на низок и среден јаглероден структурен челик за подобрување на машината.
4.Types of Annealing
Прв вид на annealing:
Цел и функција: Целта не е да се предизвика фаза на трансформација, туку да се транзитира челикот од неурамнотежена состојба во избалансирана состојба.
Видови:
• Дифузија за полнење: има за цел да го хомогенизира составот со елиминирање на сегрегацијата.
• Рекристализација на полнење: ја обновува еластичноста со елиминирање на ефектите од зацврстувањето на работата.
• Аналирање на олеснување на стресот: ги намалува внатрешните стресови без да ја промените микроструктурата.
Втор вид на annealing:
Цел и функција: има за цел да ги промени микроструктурата и својствата, постигнување на микроструктура во која доминира бисер. Овој вид исто така гарантира дека дистрибуцијата и морфологијата на бисер, ферит и карбиди исполнуваат специфични барања.
Видови:
• Целосно полнење: Го загрева челикот над температурата AC3 и потоа полека го лади за да се произведе униформа структура на бисер.
• Нецелосно полнење: Загрева челик помеѓу температурите AC1 и AC3 за делумно да се трансформира структурата.
• Изотермално полнење: го загрева челикот до над AC3, проследено со брзо ладење на изотермална температура и држење за да се постигне посакуваната структура.
• Сфероидизирање на annealing: произведува сфероидна структура на карбид, подобрување на машината и цврстината.
Ⅷ.1. Дефинирање на термичка обработка
Третманот со топлина се однесува на процес во кој металот се загрева, се држи на одредена температура, а потоа се лади додека е во цврста состојба за да се смени внатрешната структура и микроструктурата, со што се постигнуваат посакувани својства.
2. Карактеристики на термичка обработка
Третманот со топлина не ја менува формата на работното парче; Наместо тоа, ја менува внатрешната структура и микроструктурата на челикот, што пак ги менува својствата на челикот.
3.Проза на третман на топлина
Целта на третманот со топлина е да се подобрат механичките или својствата на обработка на челик (или работни парчиња), целосно да се искористи потенцијалот на челикот, да се подобри квалитетот на работното парче и да се прошири животниот век на услугата.
4.Кек заклучок
Дали својствата на материјалот може да се подобрат преку третман на топлина, критички зависи од тоа дали има промени во неговата микроструктура и структура за време на процесот на греење и ладење.
Време на пост: август-19-2024 година