1. Virsmas mēroga atzīmes
Galvenās funkcijas: nepareiza die apstrādeBIGNIEKUMIizraisīs rupjas virsmas un zivju mēroga zīmes. Šādas neapstrādātas zivju skalas zīmes ir viegli ražotas, veidojot austenīta un martensīta nerūsējošo tēraudu.
Iemesls: Vietējā gļotāda, ko izraisa nevienmērīga eļļošana vai nepareiza eļļošanas atlase un slikta eļļas kvalitāte.
2. Kļūdas defekti
Galvenās iezīmes: Die kalšanas augšējā daļa ir nepareizi izlīdzināta attiecībā pret apakšējo daļu gar atdalīšanas virsmu.
Iemesls: Kalšanas die nav līdzsvarotas neatbilstības slēdzenes vai arī die kalšana nav uzstādīta pareizi, vai sprauga starp āmura galvu un virziena sliede ir pārāk liela.
3. Nepietiekami mirstības viltojumi
Galvenās iezīmes: Die kalšanas lielums palielinās virzienā perpendikulāri atdalīšanas virsmai. Kad lielums pārsniedz zīmējumā norādīto lielumu, notiks nepietiekama mirstības kalšana.
Iemesls: Liels izmērs, zema kalšanas temperatūra, pārmērīga die dobuma nodilums utt., Radīs nepietiekamu spiedienu vai pārmērīgu zibspuldzes tilta izturību, nepietiekamu aprīkojuma tonnāžu un pārmērīgu sagataves tilpumu.
4. Nepietiekams vietējais pildījums
Galvenās iezīmes: tas galvenokārt rodas ribās, izliektos mirušos stūros utt. Die kalnos, un piepildīšanas daļas augšdaļa vai kalnu stūri nav pietiekami piepildīti, padarot kalnu kontūru neskaidrus
Iemesls: iepriekš sagatavojošā die dobuma un aizkavējošā dobuma dobuma dizains ir nepamatots, aprīkojuma tonnāža ir maza, tukša nav pietiekami uzkarsēta un metāla plūstamība ir slikta, kas var izraisīt šo defektu.
5. Liešanas struktūras atlikums
Galvenās iezīmes: ja ir atlikušā liešanas struktūra, kalnu pagarinājums un noguruma stiprums bieži nav kvalificēts. Tā kā zemas palielināšanas testa gabalā atlikušās liešanas bloķētās daļas pilnveidotās daļas nav acīmredzamas, un ir redzami pat dendritiski produkti, kas galvenokārt parādās kalnos, izmantojot tērauda lietņus kā tukšas.
Iemesls: nepietiekama kalšanas koeficienta vai nepareizas kalšanas metodes dēļ. Šis defekts samazina kalumu veiktspēju, it īpaši izturības un noguruma īpašības.
6. Graudu neviendabīgums
Galvenās iezīmes: graudi dažās daļāsBIGNIEKUMIir īpaši rupji, savukārt graudi citās daļās ir mazāki, veidojot nevienmērīgus graudus. Augstas temperatūras sakausējumi un karstumizturīgi tēraudi ir īpaši jutīgi pret graudu neviendabīgumu.
Iemesls: Zema galīgā kalšanas temperatūra izraisa vietējo darba sacietēšanu ar augsta temperatūras sakausējuma sagatavi. Redošanas un apkures procesa laikā daži graudi stipri aug vai sākotnējā kalšanas temperatūra ir pārāk augsta, un deformācija nav pietiekama, izraisot vietējās zonas deformācijas pakāpi kritiskā deformācijā. Graudu nevienmērīgums var viegli samazināt noguruma veiktspēju un izturību.
7. Saliekošie defekti
Galvenās funkcijas: racionalizācijas ir saliektas zemas palielināšanas parauga krokās, un krokas pēc izskata ir līdzīgas plaisām. Ja tā ir plaisa, racionalizētās līnijas tiks sagrieztas divreiz. Augstas palielināšanas paraugā, atšķirībā no plaisas dibena, abas puses tiek smagi oksidētas, un salocīšanas dibens ir neass.
Iemesls: to galvenokārt izraisa pārāk maz barības, pārāk daudz samazināšanas vai pārāk maza lāpstiņa filejas rādiuss stieņu kalumu un kloķvārpstas kalumu zīmēšanas procesā. Salokošanas defekti liek oksidētajam virszemes metālam sakausēt kalšanas procesa laikā.
8. Nepareiza kalšanas racionLine Distribution
Galvenās funkcijas: racionalizējiet turbulenci, piemēram, racionline refluksa, virpuļprogramma, atvienošana un konvekcija notiek, ja kalšana ir maza jauda.
Iemesls: Nepareizs die dizains, nepareiza kalšanas metodes izvēle, nepamatota forma un sagataves lielums.
9. Sadalīta struktūra
Galvenās iezīmes: struktūra, kurā citas struktūras vai ferīta fāzes ir sadalītas joslās. Tas galvenokārt pastāv austenīta-feritiskā nerūsējošā tērauda, daļēji martensīta tērauda un eutektoīda tēraudā.
Iemesls: to izraisa deformācijas kalšana, kad līdzās pastāv divi detaļu komplekti. Tas samazina materiāla šķērseniskās plastiskuma indeksu un ir pakļauts plaisāšanai pa ferīta zonu vai robežu starp abām fāzēm.
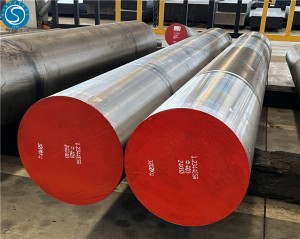
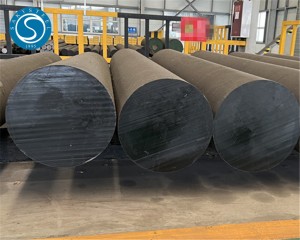
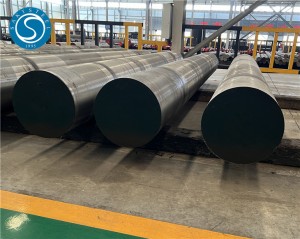
Pasta laiks: jūnijs-13-2024