Ⅰ.A hőkezelés alapfogalma.
A. A hőkezelés alapfogalma.
Ahőkezelés:
1. Meghiválás
A cél az egységes és finom austenit szerkezetének előállítása.
2. tartás
A cél annak biztosítása, hogy a munkadarab alaposan felmelegedjen, és megakadályozza a dekarburizációt és az oxidációt.
3. Hálózat
A cél az, hogy az austenitet különböző mikroszerkezetekké alakítsa.
Mikroszerkezetek hőkezelés után
A fűtés és tartás utáni hűtési folyamat során az austenit a hűtési sebességtől függően különböző mikroszerkezetekké alakul. A különböző mikroszerkezetek eltérő tulajdonságokat mutatnak.
B.A hőkezelés alapfogalma.
Osztályozás a fűtési és hűtési módszerek, valamint az acél mikroszerkezete és tulajdonságai alapján
1. Konkentrációs hőkezelés (általános hőkezelés): edzés, lágyítás, normalizálás, oltás
2. A felszínen lévő hőkezelés: Felületi kioltás, indukciós fűtés Felszíni oltás, lángfűtés felületi kioltás, elektromos érintkezési fűtés felületi oltás.
3. Kémiai hőkezelés: karburizálás, nitriding, karbonitriding.
4. Egyéb hőkezelések: Ellenőrzött légkör hőkezelés, vákuum hőkezelés, deformációs hőkezelés.
C. Az acélok kritikus hőmérséklete
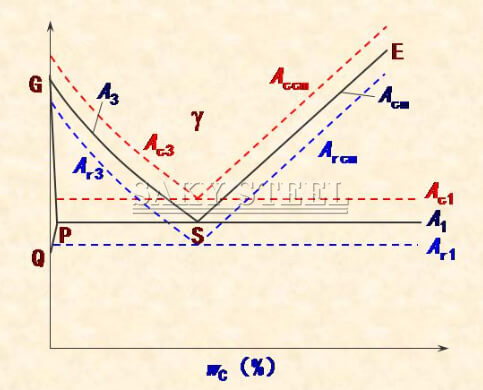
Az acél kritikus transzformációs hőmérséklete fontos alapja a fűtési, tartási és hűtési folyamatok hőkezelés során történő meghatározásához. Ezt a vas-szén fázisdiagram határozza meg.
Fő következtetés:Az acél tényleges kritikus transzformációs hőmérséklete mindig elmarad az elméleti kritikus transzformációs hőmérsékleten. Ez azt jelenti, hogy a fűtés során túlmelegedésre van szükség, és a hűtés során az alsóhűtés szükséges.
Ⅱ.
1. A lágyítás meghatározása
A lágyítás magában foglalja az acél melegítését az AC₁ kritikus pont fölött vagy alatti hőmérsékleten, amely ezen a hőmérsékleten tartja azt, majd lassan lehűti azt, általában a kemencében, hogy az egyensúlyhoz közeli szerkezetet érjen el.
2. Az izzítás célja
A megmunkálási keménység: A megmunkálható keménység elérése a HB170 ~ 230 tartományban.
② Relieve A maradék stressz: megakadályozza a deformációt vagy a repedést a következő folyamatok során.
③ A GABABAREFINÁLIS FEJLESZTÉS: Javítja a mikroszerkezetet.
④ A végső hőkezelés előkészítése: Granulált (gömb alakú) gyöngyöt kap a későbbi kioltáshoz és edzéshez.
3. A lágyítás fferoidizálására
Folyamat -előírások: A fűtési hőmérséklet az AC₁ pont közelében van.
Cél: A cementit vagy a karbidok gömbölése az acélban, granulált (gömb alakú) gyöngyöt eredményezve.
Alkalmazható tartomány: Eutektoid és hypereutectoid összetételű acélokhoz használják.
(
Folyamat -előírások: A fűtési hőmérséklet kissé alatt van a fázisdiagramon.
Cél: A szegregáció kiküszöbölése.
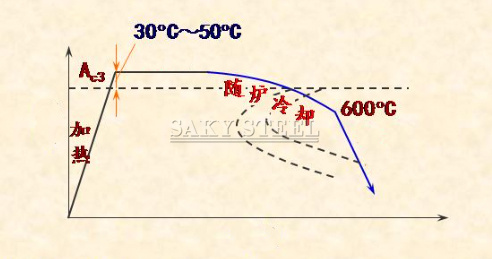
① Alacsony-szénacélMivel a széntartalom kevesebb, mint 0,25%, a normalizálás inkább az izzítás, mint előkészítő hőkezelés.
② A közepes széntartalmú acél esetében 0,25% és 0,50% közötti széntartalom, akár az izzítás, akár a normalizálás felhasználható előkészítő hőkezelésként.
③ A közepes és nagy szén-dioxid-széntartalmú acél esetében 0,50% és 0,75% között van teljes lágyítás.
④ A magas-szénacélMivel a széntartalom 0,75%-nál nagyobb, a normalizálás először a FE₃C hálózati kiküszöbölésére szolgál, amelyet a szóköz izzítás követ.
Ⅲ. Acél elküldése és edzése
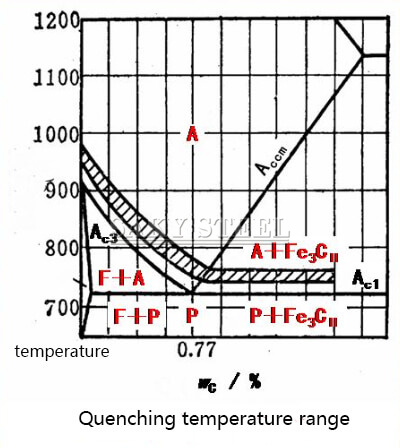
A. elrettentés
1. A kioltás meghatározása: Az oltás magában foglalja az acél melegítését egy bizonyos hőmérsékletre az AC₃ vagy AC₁ pont felett, ezen a hőmérsékleten tartva, majd a kritikus hűtési sebességnél nagyobb sebességgel hűtve.
2. A kioltás célja: Az elsődleges cél a martenzit (vagy néha alacsonyabb bainite) előállítása az acél keménységének és kopásállóságának növelése érdekében. Az oltás az acél egyik legfontosabb hőkezelési folyamata.
3.A különféle típusú acélokhoz oltási hőmérsékleteket határoz meg
Hypoeutectoid acél: AC₃ + 30 ° C - 50 ° C
Eutektoid és hyperereutectoid acél: AC₁ + 30 ° C - 50 ° C
Ötvözött acél: 50 ° C - 100 ° C a kritikus hőmérséklet felett
4. Az ideális oltó közeg hűvös tulajdonságai:
Lassú hűtés az "orr" hőmérséklete előtt: a termikus feszültség megfelelő csökkentése érdekében.
Magas hűtési képesség az "orr" hőmérséklete közelében: A nem-martenzit szerkezetek kialakulásának elkerülése érdekében.
Lassú hűtés az M₅ pont közelében: A martenzitikus transzformáció által kiváltott stressz minimalizálása érdekében.
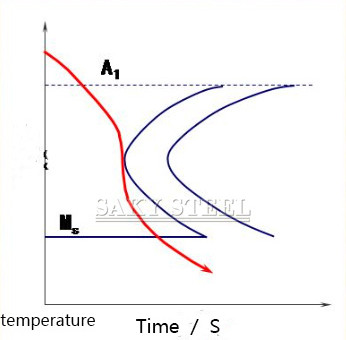
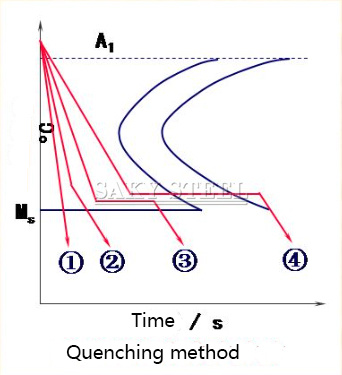
5. A módszerek és azok jellemzői kiküszöbölése:
① Egyetlen oltás: Könnyen kezelhető és alkalmas kis, egyszerű alakú munkadarabokhoz. A kapott mikroszerkezet martenzit (M).
② Double oltás: Bonyolultabb és nehezebb irányítható, komplex alakú, magas széntartalmú acélhoz és nagyobb ötvözött acél munkadarabokhoz használják. A kapott mikroszerkezet martenzit (M).
③ Töréskivágás: Egy bonyolultabb folyamat, amelyet nagy, komplex alakú ötvözött acél munkadarabokhoz használnak. A kapott mikroszerkezet martenzit (M).
④ISOTERMAL oltás: Kis, komplex alakú munkadarabokhoz használják, magas követelményekkel. A kapott mikroszerkezet az alacsonyabb bainit (B).
6. A keményíthetőséget befolyásoló tényezők
A keményíthetőség szintje az acél túlhűtött austenit stabilitásától függ. Minél magasabb a túlhűtött austenit stabilitása, annál jobb a keménység, és fordítva.
A túlhűtött austenit stabilitását befolyásoló tényezők:
A C-görbe helyzete: Ha a C-görbe jobbra változik, akkor a kioltás kritikus hűtési sebessége csökken, javítva a keményíthetőséget.
Fő következtetés:
Bármely olyan tényező, amely a C-görbét jobbra tolja, növeli az acél keménységét.
Fő tényező:
Kémiai összetétel: A kobalt (CO) kivételével az austenitben feloldott összes ötvöző elem növeli a keményíthetőséget.
Minél közelebb van a széntartalom az eutektoid összetételéhez a szénacélban, annál inkább a C-görbe jobbra változik, és annál nagyobb a keménység.
7.A keményíthetőség meghatározása és ábrázolása
①end quench keménységi teszt: A keményíthetőséget a vég-quadench teszt módszerrel mérik.
② Kritikus oltási átmérő módszer: A kritikus oltási átmérő (D₀) azt a maximális acél átmérőjét képviseli, amelyet egy adott kioltó közegben teljesen megkeményíthetünk.
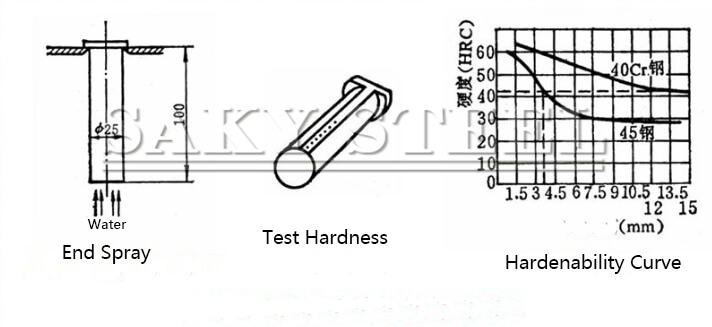
B. -tempering
1. A kedvelés meghatározása
A edzés egy olyan hőkezelési folyamat, amelyben az oltott acélt az A₁ pont alatti hőmérsékletre melegítik, ezen a hőmérsékleten tartják, majd szobahőmérsékletre lehűtik.
2.
Csökkentse vagy kiküszöbölje a maradék stressz: megakadályozza a munkadarab deformációját vagy repedését.
Csökkentse vagy kiküszöbölje a maradék austenitet: stabilizálja a munkadarab méretét.
Távolítsa el a kioltott acél törékenységét: A mikroszerkezet és a tulajdonságok beállítása a munkadarab követelményeinek való megfelelés érdekében beállítja.
Fontos megjegyzés: Az acélt azonnal meg kell edzeni.
3.Az folyamat folyamatok
1.Az edzéscsökkentés
Cél: A feszültség csökkentése, a munkadarab szilárdságának javítása, valamint a nagy keménység és a kopásállóság elérése.
Hőmérséklet: 150 ° C ~ 250 ° C.
Teljesítmény: Keménység: HRC 58 ~ 64. Nagy keménység és kopásállóság.
Alkalmazások: szerszámok, öntőformák, csapágyak, karburizált alkatrészek és felületi keményített alkatrészek.
2. A magas edzés
Cél: A nagy keménység elérése, elegendő erővel és keménységgel együtt.
Hőmérséklet: 500 ° C ~ 600 ° C.
Teljesítmény: Keménység: HRC 25 ~ 35. Jó általános mechanikai tulajdonságok.
Alkalmazások: Tengelyek, fogaskerekek, összekötő rudak stb.
Hőfinomítás
Meghatározás: Az oltást, amelyet a magas hőmérsékleten végzett edzés követi, termikus finomításnak vagy egyszerűen edzésnek nevezzük. Az ezzel a folyamat által kezelt acél teljes teljesítménye kiváló és széles körben használható.
Ⅳ. Acél felületének hőkezelése
A. Acélok felszámolása
1. A felületi edzés meghatározása
A felületi keményedés egy olyan hőkezelési folyamat, amelynek célja a munkadarab felületi rétegének erősítése azáltal, hogy gyorsan melegíti azt, hogy a felületréteget austenitré alakítsa, majd gyorsan lehűtse. Ezt a folyamatot az acél kémiai összetételének vagy az anyag magszerkezetének megváltoztatása nélkül hajtják végre.
2.
A felszíni edzéshez használt anyagok
Jellemző anyagok: Közepes szénacél és közepes szén -dioxid -ötvözött acél.
Előzetes kezelés: Tipikus folyamat: edzés. Ha az alaptulajdonságok nem kritikusak, akkor a normalizálás helyette használható.
Keményedés utáni felépítés
Felület szerkezete: A felületi réteg általában olyan edzett szerkezetet képez, mint például a martenzit vagy a bainit, amely nagy keménységet és kopásállóságot biztosít.
Magszerkezet: Az acél magja általában megtartja eredeti szerkezetét, például a gyöngyház vagy az edzett állapotot, az előkezelési eljárástól és az alapanyag tulajdonságaitól függően. Ez biztosítja, hogy a mag fenntartsa a jó keménységet és erőt.
B.A indukciós felület edzésének karaktisztikája
(
2. Feltöltse az austenit szemcsék szerkezetét a felületi rétegben: A gyors fűtési és későbbi kioltási folyamat során a felületi réteg finom austenit szemcséket képez. A kioltás után a felület elsősorban finom martenzitből áll, a keménységgel jellemzően 2-3 HRC-vel magasabb, mint a hagyományos oltás.
3. A jó felület minősége: A rövid fűtési idő miatt a munkadarab felülete kevésbé hajlamos az oxidációra és a dekarburizációra, és a kioltás által kiváltott deformációt minimalizálják, biztosítva a jó felület minőségét.
(
5. Nagy termelési hatékonyság: Az indukciós felületi keményedés alkalmas a tömegtermelésre, nagy működési hatékonyságot kínálva.
C. A kémiai hőkezelés osztályozása
Karburkolás, karburizálás, karburizálás, kromizáló, szilikonizáló, szilikonizáló, szilikonizáló, karbonitriding, borokarburizálás
D.GAS Carburizing
A gázkarburizálás olyan folyamat, amikor egy munkadarabot lezárt gázkarburizáló kemencébe helyeznek, és olyan hőmérsékletre melegítik, amely az acél austenitré alakítja. Ezután egy karburizáló szert csepegtetnek a kemencébe, vagy egy karburizációs légkört közvetlenül vezetnek be, lehetővé téve a szénatomok számára, hogy diffundálhassanak a munkadarab felületi rétegébe. Ez a folyamat növeli a széntartalmat (WC%) a munkadarab felületén.
√karburizáló szerek:
• Szénben gazdag gázok: például széngáz, cseppfolyósított kőolajgáz (LPG) stb.
• Szerves folyadékok: például petróleum, metanol, benzol stb.
√ Carburizing A folyamat paraméterek:
• Karburizációs hőmérséklet: 920 ~ 950 ° C.
• Karburkolási idő: A karburizált réteg kívánt mélységétől és a karburizációs hőmérséklettől függ.
E.Heat kezelés a karburizálás után
Az acélnak hőkezelésnek kell lennie a karburizálás után.
Hőkezelési folyamat a karburizálás után:
√quanching + alacsony hőmérsékleti edzés
1.Az irányítás az előzetes hűtés után + alacsony hőmérsékleti edzés után: A munkadarabot a karburizációs hőmérsékletről a mag AR₁ hőmérséklete fölé hűvösek, majd azonnal lefordítják, majd az alacsony hőmérsékletű edzés 160 ~ 180 ° C-on.
2. A hűvösség elrendezése az előzetes hűtés után + alacsony hőmérsékleti edzés után: A karburizálás után a munkadarabot lassan szobahőmérsékletre lehűtik, majd újra melegítik az oltás és az alacsony hőmérsékleten történő edzés céljából.
3. Kettős oltás az előzetes hűtés után + alacsony hőmérsékleti edzés után: A karburizálás és a lassú hűtés után a munkadarab két szakaszon megy keresztül a fűtés és a kioltás, majd az alacsony hőmérsékleten edzés.
Ⅴ. Acélok kémiai hőkezelése
1. A kémiai hőkezelés meghatározása
A kémiai hőkezelés olyan hőkezelési eljárás, amelyben az acél munkadarabot egy adott aktív közegbe helyezik, melegítik és hőmérsékleten tartják, lehetővé téve a tápközegben lévő aktív atomok diffundálását a munkadarab felületére. Ez megváltoztatja a munkadarab felületének kémiai összetételét és mikroszerkezetét, ezáltal megváltoztatva annak tulajdonságait.
2. A kémiai hőkezelés alapvető folyamata
Bomlás: Fűtés közben az aktív közepes bomlik, az aktív atomok felszabadítása.
Abszorpció: Az aktív atomokat az acél felülete adszorbeálja, és feloldja az acél szilárd oldatába.
Diffúzió: Az acél felületén felszívódott és feloldott aktív atomok vándorolnak a belső térbe.
Az indukciós felület megkeményedésének típusai
A.Hight frekvenciájú indukciós fűtés
Jelenlegi frekvencia: 250 ~ 300 kHz.
Keményített rétegmélység: 0,5 ~ 2,0 mm.
Alkalmazások: Közepes és kis modul fogaskerekek és kis és közepes méretű tengelyek.
B.Medium-frekvenciájú indukciós fűtés
Jelenlegi frekvencia: 2500 ~ 8000 kHz.
Keményített réteg mélysége: 2 ~ 10 mm.
Alkalmazások: Nagyobb tengelyek és nagy és közepes modul fogaskerekek.
C. Power-frekvenciájú indukciós fűtés
Jelenlegi frekvencia: 50 Hz.
Keményített réteg mélysége: 10 ~ 15 mm.
Alkalmazások: Nagyon mélyen megkeményedett réteget igénylő munkadarabok.
3. Indukciós felület megkeményedése
Az indukciós felület megkeményedésének alapelve
Bőrhatás:
Ha az indukciós tekercs váltakozó árama az áramot indukálja a munkadarab felületén, az indukált áram nagy része a felület közelében koncentrálódik, míg szinte egyetlen áram sem halad át a munkadarab belsejében. Ezt a jelenséget bőrhatásnak nevezik.
Az indukciós felület megkeményedésének elve:
A bőrhatás alapján a munkadarab felületét gyorsan melegítik az austenitizáló hőmérsékletre (néhány másodperc alatt 800 ~ 1000 ° C -ra emelkedik), míg a munkadarab belseje szinte fűtött. A munkadarabot ezután vízpermetezéssel hűtik, a felületi edzés elérésével.
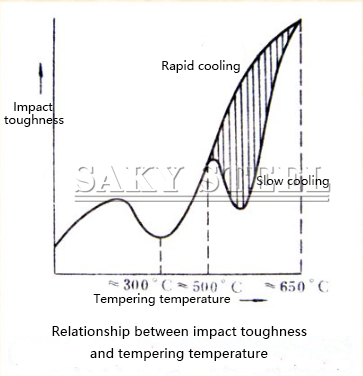
4.Am -féle törékenység
A britosság edzése az oltott acélban
A britosság edzése arra a jelenségre utal, amikor a leoltott acél ütési szilárdsága jelentősen csökken, ha bizonyos hőmérsékleten edzik.
Az első típusú edzési törékenység
Hőmérsékleti tartomány: 250 ° C - 350 ° C.
Jellemzők: Ha az oltott acél ezen a hőmérsékleti tartományon belül van enyhítve, akkor nagy valószínűséggel fejleszti ki az ilyen típusú edzési törékenységet, amelyet nem lehet kiküszöbölni.
Megoldás: Kerülje el az oltott acél edzését ezen a hőmérsékleti tartományon belül.
Az első típusú edzési törékenységet az alacsony hőmérsékletű edzéses törésnek vagy a visszafordíthatatlan edzési törékenységnek is nevezik.
Ⅵ.
1.Aztatás a végleges hőkezelési folyamat, amely az oltást követi.
Miért kell az eloltott acéloknak edzeni?
Mikrostruktúra a kioltás után: A kioltás után az acél mikroszerkezete általában martenzitből és maradék austenitből áll. Mindkettő metastabil fázis, és bizonyos körülmények között átalakul.
A martenzit tulajdonságai: A martenzitet nagy keménység, de a nagy törékenység jellemzi (különösen a nagy szén-dioxid-szén-dioxid-szerű martenzitben), amely sok alkalmazás teljesítményigényének nem felel meg.
A martenzitikus transzformáció jellemzői: A martenzitré történő transzformáció nagyon gyorsan megtörténik. Az oltás után a munkadarab maradék belső feszültségekkel rendelkezik, amelyek deformációhoz vagy repedéshez vezethetnek.
Következtetés: A munkadarab nem használható közvetlenül a kioltás után! A belső feszültségek csökkentése és a munkadarab szilárdságának javítása érdekében edzésre van szükség, így a használatra alkalmas.
2. A keményíthetőség és a keményedési képesség közötti különbség:
Keményíthetőség:
A keményíthetőség arra utal, hogy az acél azon képessége, hogy a kiküszöbölés után bizonyos mélységű edzést (az edzett réteg mélységét) elérje. Ez az acél összetételétől és szerkezetétől függ, különös tekintettel az ötvözet elemeitől és az acél típusától. A keményíthetőség annak mértéke, hogy az acél mennyire képes megszilárdítani az egész vastagságát az oltási folyamat során.
Keménység (keményedési képesség):
A keménység vagy a keményedési képesség arra a maximális keménységre utal, amelyet az acélban el lehet érni a kioltás után. Ezt nagymértékben befolyásolja az acél széntartalma. A magasabb széntartalom általában nagyobb potenciális keménységhez vezet, de ezt korlátozhatja az acél ötvöző elemei és a kioltási folyamat hatékonysága.
3.A acél megítélhetősége
√ A keményíthetőség megfogalmazása
A keményíthetőség arra utal, hogy az acél azon képessége, hogy elérje a martenzitikus edzés bizonyos mélységét, miután az austenitizáló hőmérsékleten kioltották. Egyszerűbb értelemben az acél képessége, hogy martenzitet képezzen az oltás során.
A keménység mérése
A keményíthetőség méretét a megkeményedett réteg mélysége jelzi, amelyet meghatározott körülmények között kaptak a kioltás után.
Keményített rétegmélység: Ez a mélység a munkadarab felületétől a régióig, ahol a szerkezet fél martenzit.
Közös oltó média:
•Víz
Jellemzők: Gazdaságos, erős hűtési képességgel, de magas hűtési sebességgel rendelkezik a forráspont közelében, ami túlzott hűtéshez vezethet.
Alkalmazás: Általában a szén acélokhoz használják.
Sós víz: A vízben lévő só- vagy lúgos oldat, amely magasabb hűtési képességgel rendelkezik, magas hőmérsékleten a vízhez képest, így a szén acélokhoz alkalmas.
•Olaj
Jellemzők: Lassabb hűtési sebességet biztosít alacsony hőmérsékleten (a forráspont közelében), amely hatékonyan csökkenti a deformáció és a repedés tendenciáját, de alacsony hőmérsékleten alacsonyabb hűtési képességgel rendelkezik.
Alkalmazás: Alkalmas ötvözött acélokhoz.
Típusok: Tartalmazza az olaj, a gépi olaj és a dízelüzemanyag kioltását.
Fűtési idő
A fűtési idő mind a fűtési sebességből (a kívánt hőmérséklet eléréséhez szükséges idő), mind a tartási időből (a célhőmérsékleten fenntartott idő) áll.
A fűtési idő meghatározásának alapelvei: Biztosítsa az egységes hőmérsékleti eloszlást a munkadarab egész területén, mind belül, mind kívül.
Gondoskodjon a teljes austenitizációról, és hogy a képződött austenit egyenletes és finom.
A fűtési idő meghatározásának alapja: Általában empirikus képletek felhasználásával vagy kísérletezéssel határoznak meg.
A média eloltása
Két fő szempont:
A. Hálózati sebesség: A magasabb hűtési sebesség elősegíti a martenzit képződését.
B. Reziduális stressz: A magasabb hűtési sebesség növeli a maradék feszültséget, ami nagyobb tendenciát okozhat a deformációra és a munkadarab repedésére.
Ⅶ.normalizálás
1. A normalizálás meghatározása
A normalizálás egy olyan hőkezelési folyamat, amelyben az acélt 30 ° C-50 ° C hőmérsékletre melegítik az AC3 hőmérséklete felett, ezen a hőmérsékleten tartva, majd léghűtéssel, hogy mikroszerkezetet kapjunk az egyensúlyi állapot közelében. Az izzításhoz képest a normalizálás gyorsabb hűtési sebességgel rendelkezik, ami finomabb gyöngyházszerkezetet (P), valamint nagyobb szilárdságot és keménységet eredményez.
2. A normalizálás célja
A normalizálás célja hasonló a lágyításhoz.
3. Normalizálás alkalmazásai
• Távolítsa el a hálózatba kötött másodlagos cementitet.
• Az alacsonyabb követelményekkel rendelkező alkatrészek végső hőkezelése.
• Az alacsony és közepes szénszerkezeti acél előkészítő hőkezelése a megmunkálhatóság javítása érdekében.
4. Az izzítás típusát
Első típusú lágyítás:
Cél és funkció: A cél nem a fázisátalakítás indukálása, hanem az acél kiegyensúlyozatlan állapotból történő átmenete kiegyensúlyozott állapotba.
Típusok:
• Diffúziós lágyítás: Célja a kompozíció homogenizálására a szegregáció kiküszöbölésével.
• Átkristályosítás Az izzítás: Helyezze vissza a rugalmasságot a munka edzésének hatásainak kiküszöbölésével.
• Stressz -enyhítés lágyítás: Csökkenti a belső feszültségeket a mikroszerkezet megváltoztatása nélkül.
A lágyítás második típusa:
Cél és funkció: Célja a mikroszerkezet és a tulajdonságok megváltoztatása, a gyöngyház által dominált mikroszerkezet elérése. Ez a típus biztosítja azt is, hogy a gyöngyház, a ferrit és a karbidok eloszlása és morfológiája megfeleljen a konkrét követelményeknek.
Típusok:
• Teljes lágyítás: Melegíti az acélt az AC3 hőmérséklete fölött, majd lassan lehűti, hogy egyenletes gyöngyszerkezetet hozzon létre.
• Hiányos lágyítás: Az acélt melegíti az AC1 és AC3 hőmérséklete között, hogy a szerkezetet részben átalakítsa.
• Izotermikus lágyítás: Az acélt az AC3 fölé melegíti, majd a gyors hűtést izotermikus hőmérsékletre és tartás a kívánt szerkezet elérése érdekében.
• Szűrőidáló lágyítás: Gömb alakú karbid szerkezetet hoz létre, javítva a megmunkálhatóságot és a keménységet.
Ⅷ.1. A hőkezelés meghatározása
A hőkezelés olyan folyamatra utal, amelyben a fém melegítik, egy meghatározott hőmérsékleten tartják, majd szilárd állapotban lehűtik, hogy megváltoztassák belső szerkezetét és mikroszerkezetét, ezáltal elérve a kívánt tulajdonságokat.
2. A hőkezelés karaktisztikája
A hőkezelés nem változtatja meg a munkadarab alakját; Ehelyett megváltoztatja az acél belső szerkezetét és mikroszerkezetét, ami viszont megváltoztatja az acél tulajdonságait.
3.A hőkezelés elterjedése
A hőkezelés célja az acél (vagy munkadarabok) mechanikai vagy feldolgozási tulajdonságainak javítása, az acél potenciáljának teljes felhasználása, a munkadarab minőségének javítása és a szolgáltatási élettartam meghosszabbítása.
4. Kísérleti következtetés
Az, hogy az anyag tulajdonságai a hőkezelés révén javíthatók -e, kritikusan függ attól, hogy a fűtési és hűtési folyamat során megváltozik -e annak mikroszerkezete és szerkezete.
A postai idő: augusztus-19-24.