ⅰ. مفهوم اساسی عملیات حرارتی.
A. مفهوم اساسی عملیات حرارتی.
عناصر و کارکردهای اساسیعملیات حرارتی:
1. گرم کردن
هدف این است که یک ساختار آستنیت یکنواخت و ریز بدست آورید.
2. نگهدار
هدف این است که اطمینان حاصل شود که قطعه کار کاملاً گرم شده و از دکوراسیون و اکسیداسیون جلوگیری می شود.
3. رنگ آمیزی
هدف تبدیل آستنیت به ریزساختارهای مختلف است.
ریزساختارها پس از عملیات حرارتی
در طی فرآیند خنک کننده پس از گرمایش و نگه داشتن ، آستنیت بسته به میزان خنک کننده به ریزساختارهای مختلف تبدیل می شود. ریزساختارهای مختلف خصوصیات مختلفی را نشان می دهند.
ب. مفهوم اساسی عملیات حرارتی.
طبقه بندی بر اساس روشهای گرمایش و سرمایش و همچنین ریزساختار و خصوصیات فولاد
1. عملیات حرارتی متعارف (عملیات حرارتی کلی): مزاج ، بازپخت ، عادی سازی ، فرونشست
2. درمان حرارتی: خاموش کردن سطح ، فرونشست سطح گرمایش القایی ، خاموش کردن سطح گرمایش شعله ، خاموش کردن سطح گرمایش تماس الکتریکی.
3. عملیات حرارتی شیمیایی: کاربور کردن ، نیتریدر ، کربن.
4- درمان حرارتی دیگر: عملیات حرارتی جو کنترل شده ، عملیات حرارتی خلاء ، عملیات حرارتی تغییر شکل.
ج. دمای بحرانی فولادها
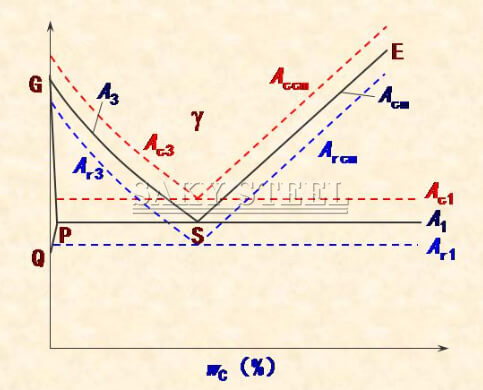
دمای تحول بحرانی فولاد مبنای مهمی برای تعیین فرآیندهای گرمایش ، نگهداری و خنک کننده در حین عملیات حرارتی است. این توسط نمودار فاز آهن-کربن تعیین می شود.
نتیجه گیری کلیدی:دمای تحول بحرانی واقعی فولاد همیشه از دمای تحول انتقادی نظری عقب مانده است. این بدان معنی است که گرمای بیش از حد در هنگام گرمایش مورد نیاز است و در هنگام خنک کننده ، زیربنایی لازم است.
.
1. تعریف آنیلایینگ
بازپرداخت شامل گرمایش فولاد به دمای بالاتر یا زیر نقطه بحرانی است که آن را در آن دما نگه می دارد و سپس به آرامی خنک می شود ، معمولاً در داخل کوره ، برای دستیابی به یک ساختار نزدیک به تعادل.
2. هدف آنیلینگ
① سختی برای ماشینکاری: دستیابی به سختی ماشینکاری در محدوده 230 HB170.
stress استرس باقیمانده: از تغییر شکل یا ترک خوردگی در طی فرآیندهای بعدی جلوگیری می کند.
ساختار دانه Refine: ریزساختار را بهبود می بخشد.
preparation برای عملیات حرارتی نهایی: مروارید گرانول (کروی) را برای فرونشست و خویشتن داری بعدی بدست می آورد.
3. بازپرداخت سود
مشخصات فرآیند: دمای گرمایش در نزدیکی نقطه AC₁ است.
هدف: برای کروی سیمانیت یا کاربیدها در فولاد ، و در نتیجه مروارید دانه ای (کروی) ایجاد می شود.
دامنه قابل اجرا: برای فولادهای دارای ترکیبات eutectoid و hypereutectoid استفاده می شود.
4. پخت و پز (بازپرداخت همگن)
مشخصات فرآیند: دمای گرمایش کمی پایین تر از خط Solvus در نمودار فاز است.
هدف: برای از بین بردن تفکیک.
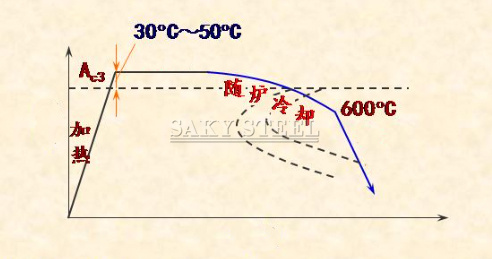
① برای پایینفولادبا توجه به میزان کربن کمتر از 0.25 ٪ ، عادی سازی نسبت به بازپخت به عنوان یک عملیات حرارتی مقدماتی ترجیح داده می شود.
② در مورد فولاد کربن متوسط با میزان کربن بین 0.25 ٪ و 0.50 ٪ ، از آنیل شدن یا عادی سازی می توان به عنوان عملیات حرارتی مقدماتی استفاده کرد.
③ برای فولاد کربن متوسط تا زیاد با میزان کربن بین 0.50 ٪ و 0.75 ٪ ، بازپرداخت کامل توصیه می شود.
④ برای بالافولادبا توجه به میزان کربن بیش از 0.75 ٪ ، برای اولین بار از عادی سازی برای از بین بردن شبکه Fe₃C استفاده می شود و پس از آن بازپخت کروی.
.
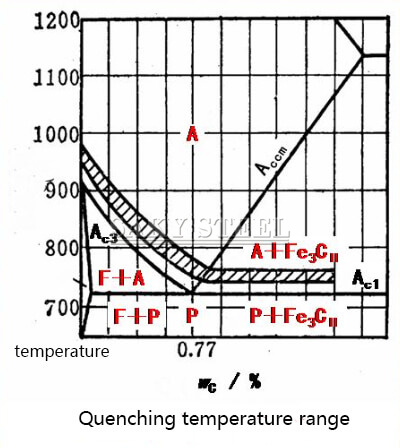
الف.
1. تعریف خاموش کردن: خاموش کردن شامل گرم کردن فولاد به دمای معینی بالاتر از نقطه ac₃ یا ac₁ ، نگه داشتن آن در آن دما ، و سپس خنک کردن آن با سرعت بیشتر از میزان خنک کننده بحرانی برای تشکیل مارتنزیت است.
2. هدف از خاموش کردن: هدف اصلی بدست آوردن مارتنزیت (یا گاهی اوقات پایین باینیت) برای افزایش سختی و مقاومت در برابر سایش فولاد است. فرونشست یکی از مهمترین فرآیندهای عملیات حرارتی برای فولاد است.
3. تعیین درجه حرارت خاموش برای انواع مختلف فولاد
فولاد هیپوئوتکتوئید: ac₃ + 30 درجه سانتیگراد تا 50 درجه سانتیگراد
فولاد eutectoid و hypereutectoid: ac₁ + 30 ° C تا 50 درجه سانتیگراد
فولاد آلیاژی: 50 درجه سانتیگراد تا 100 درجه سانتیگراد بالاتر از دمای بحرانی
4. ویژگی های اتصال یک رسانه خاموش ایده آل:
خنک کننده آهسته قبل از دمای "بینی": برای کاهش کافی استرس حرارتی.
ظرفیت خنک کننده بالا در نزدیکی دمای "بینی": برای جلوگیری از تشکیل ساختارهای غیر مارتنسیتی.
خنک کننده آهسته در نزدیکی M₅ Point: برای به حداقل رساندن استرس ناشی از تحول مارتنزیتیک.
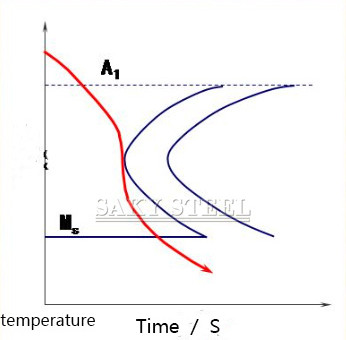
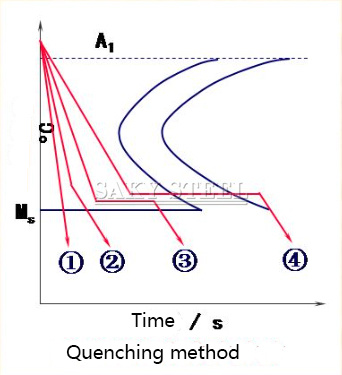
5. روشهای چرخشی و ویژگی های آنها:
-خاموش کردن ساده: کار کردن آسان و مناسب برای کارگروه های کوچک و ساده شکل. ریزساختار حاصل از مارتنزیت (M) است.
خاموش کردن: کنترل پیچیده تر و دشوارتر ، برای استفاده برای فولاد کربن بلند و پیچیده و کارگروه های بزرگ فولادی آلیاژ استفاده می شود. ریزساختار حاصل از مارتنزیت (M) است.
③ خاموش شدن broken: یک فرآیند پیچیده تر ، برای کارگروه های بزرگ و پیچیده آلیاژ به شکل فولادی استفاده می شود. ریزساختار حاصل از مارتنزیت (M) است.
④ خاموشی گرمسیری: برای قطعه های کوچک و پیچیده شکل با نیازهای زیاد استفاده می شود. ریزساختار حاصل از آن باینیت پایین تر (B) است.
6. فاکتورهای مؤثر بر سخت بودن
سطح سختگیری بستگی به پایداری آستنیت ابرقهرمانی در فولاد دارد. هرچه ثبات آستنیت ابرقهرمانان بالاتر باشد ، سختگیری بهتر می شود و برعکس.
عوامل مؤثر بر ثبات آستنیت ابرقهرمانان:
موقعیت منحنی C: اگر منحنی C به سمت راست تغییر کند ، میزان خنک کننده بحرانی برای خاموش شدن کاهش می یابد و باعث افزایش سخت شدن می شود.
نتیجه گیری کلیدی:
هر عاملی که منحنی C را به سمت راست تغییر دهد ، سخت بودن فولاد را افزایش می دهد.
عامل اصلی:
ترکیب شیمیایی: به جز کبالت (CO) ، همه عناصر آلیاژ حل شده در آستنیت باعث افزایش سخت بودن می شوند.
هرچه میزان کربن به ترکیب eutectoid در فولاد کربن نزدیکتر باشد ، منحنی C بیشتر به سمت راست تغییر می کند و سختگیری بیشتر می شود.
7. تعیین و بازنمایی سخت بودن
test تست سخت قابلیت فرونشست: سختگیری با استفاده از روش تست پایان کار اندازه گیری می شود.
روش قطر فرونشست بحرانی: قطر خفگی بحرانی (D₀) حداکثر قطر فولاد را نشان می دهد که می تواند در یک محیط خاص خاموش کردن به طور کامل سخت شود.
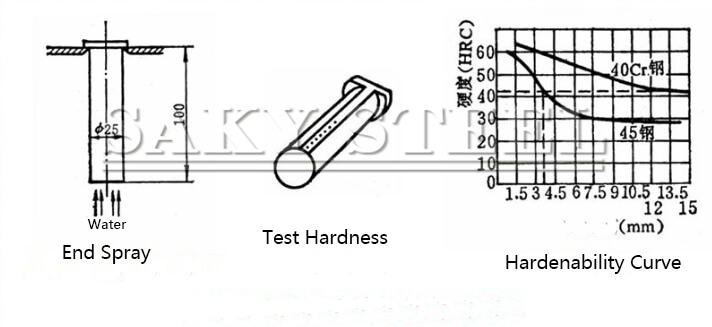
b.tempering
1. تعریف معتدل
Tempering یک فرآیند عملیات حرارتی است که در آن فولاد خاموش به دمای زیر نقطه A₁ ، که در آن دما نگه داشته می شود ، گرم می شود و سپس به دمای اتاق خنک می شود.
2. هدف از مزاج
کاهش یا از بین بردن استرس باقیمانده: از تغییر شکل یا ترک خوردگی قطعه کار جلوگیری می کند.
آستنیت باقیمانده را کاهش یا از بین ببرید: ابعاد قطعه کار را تثبیت می کند.
از بین بردن شکنندگی فولاد خاموش: ریزساختار و خواص را برای پاسخگویی به نیازهای قطعه کار تنظیم می کند.
نکته مهم: فولاد باید بلافاصله پس از فرونشست دچار تسویه حساب شود.
3. فرآیندهای تحریک کننده
1. درجه حرارت
هدف: برای کاهش استرس خاموش ، بهبود سختی قطعه کار و دستیابی به سختی و مقاومت در برابر سایش.
دما: 150 درجه سانتیگراد ~ 250 درجه سانتیگراد.
عملکرد: سختی: HRC 58 ~ 64. مقاومت بالا و مقاومت در برابر سایش.
برنامه ها: ابزارها ، قالب ها ، یاتاقان ها ، قطعات کاربوریزه شده و اجزای سخت شده سطح.
2. درجه حرارت بالا
هدف: برای دستیابی به سختی زیاد در کنار قدرت و سختی کافی.
دما: 500 درجه سانتیگراد 600 درجه سانتیگراد.
عملکرد: سختی: HRC 25 ~ 35. خواص مکانیکی کلی خوب.
برنامه ها: شفت ، چرخ دنده ، میله های اتصال و غیره
تصفیه حرارتی
تعریف: خاموش شدن به دنبال آن با درجه حرارت بالا ، پالایش حرارتی یا به سادگی معتدل نامیده می شود. فولاد تحت درمان با این فرآیند عملکرد کلی بسیار خوبی دارد و به طور گسترده مورد استفاده قرار می گیرد.
ⅳ. پایماسیون حرارتی از فولاد
a.sureface خاموش کردن فولادها
1. تعریف سخت شدن سطح
سخت شدن سطح یک فرآیند تصفیه حرارتی است که برای تقویت لایه سطح یک قطعه کار با گرم کردن سریع آن برای تبدیل لایه سطح به آستنیت و سپس خنک کردن سریع آن طراحی شده است. این فرآیند بدون تغییر ترکیب شیمیایی فولاد یا ساختار اصلی مواد انجام می شود.
2. مواد مورد استفاده برای سخت شدن سطح و ساختار پس از سختگیری
مواد مورد استفاده برای سخت شدن سطح
مواد معمولی: فولاد کربن متوسط و فولاد آلیاژ کربن متوسط.
قبل از درمان: فرآیند معمولی: معتدل. اگر خواص اصلی بسیار مهم نباشد ، به جای آن می توان از عادی سازی استفاده کرد.
ساختار پس از سالخورده
ساختار سطح: لایه سطح به طور معمول یک ساختار سخت شده مانند مارتنزیت یا باینیت را تشکیل می دهد ، که سختی و مقاومت در برابر سایش را فراهم می کند.
ساختار هسته: هسته فولاد به طور کلی بسته به فرآیند قبل از درمان و خواص مواد پایه ، ساختار اصلی خود ، مانند مروارید یا حالت معتدل را حفظ می کند. این تضمین می کند که هسته سختی و قدرت خوبی را حفظ می کند.
ب - ویژگی های سخت شدن سطح القایی
1. دمای گرمایش بالا و افزایش سریع درجه حرارت: سخت شدن سطح القایی به طور معمول شامل دمای گرمایش بالا و میزان گرمایش سریع است و باعث می شود در مدت زمان کوتاهی گرمایش سریع شود.
2. ساختار دانه آستنیت در لایه سطح: در طول گرمایش سریع و فرآیند خاموش کردن متعاقب آن ، لایه سطح دانه های آستنیت ریز تشکیل می دهد. پس از خاموش شدن ، سطح در درجه اول از مارتنزیت ریز تشکیل شده است ، با سختی به طور معمول 2-3 HRC بالاتر از خاموش شدن معمولی است.
3. کیفیت سطح خوب: با توجه به زمان گرمایش کوتاه ، سطح قطعه کار کمتر در معرض اکسیداسیون و دکربول سازی قرار دارد و تغییر شکل ناشی از فرونشست به حداقل می رسد و از کیفیت سطح خوبی برخوردار است.
4- قدرت خستگی بالا: تحول فاز مارتنزیتی در لایه سطح استرس فشاری ایجاد می کند و این باعث افزایش قدرت خستگی قطعه کار می شود.
5. بهره وری تولید بالا: سخت شدن سطح القایی برای تولید انبوه مناسب است و بهره وری عملیاتی بالایی را ارائه می دهد.
ج. طبقه بندی عملیات حرارتی شیمیایی
کاروبوریزه ، کاربوریزه کردن ، کارگروزینگ ، کروم ، سیلیکونیزاسیون ، سیلیکونیزاسیون ، سیلیکونیزاسیون ، کربنیتریدر ، بوروکربوریزه کردن
D.gas carburburing
کاروبوریزه کننده گاز فرآیندی است که در آن یک قطعه کار در یک کوره کاربرز گاز مهر و موم شده قرار می گیرد و به دما گرم می شود که فولاد را به آستنیت تبدیل می کند. سپس ، یک ماده کاربرینگ به داخل کوره ریخته می شود ، یا یک فضای کاربرینگ مستقیماً معرفی می شود و به اتم های کربن اجازه می دهد تا در لایه سطح قطعه کار پخش شوند. این فرآیند میزان کربن (WC ٪) را در سطح قطعه کار افزایش می دهد.
عوامل محور:
• گازهای غنی از کربن: مانند گاز زغال سنگ ، گاز نفتی مایع (LPG) و غیره.
• مایعات ارگانیک: مانند نفت سفید ، متانول ، بنزن و غیره.
parameters پارامترهای فرآیند:
• دمای کارگور کردن: 950 ~ 950 درجه سانتیگراد.
• زمان کاربور کردن: بستگی به عمق مورد نظر لایه کاربوریزه شده و دمای کارگور سازی دارد.
درمان E.Heat پس از کارگروه
فولاد پس از کارآزمایی باید تحت عملیات حرارتی قرار بگیرد.
فرآیند عملیات حرارتی پس از کارگروه:
recchenching + درجه حرارت درجه حرارت پایین
1. خاموش کردن مستقیم پس از خنک کننده + درجه حرارت درجه حرارت پایین: قطعه کار از دمای کاربریزاسیون تا بالاتر از دمای هسته هسته از قبل خنک می شود و سپس بلافاصله خاموش می شود ، و به دنبال آن با درجه حرارت کم درجه سانتیگراد در دمای 160 ~ 180 درجه سانتیگراد.
2. خاموش شدن پس از خنک کننده + درجه حرارت کم درجه حرارت: بعد از کارآزمایی ، قطعه کار به آرامی به دمای اتاق خنک می شود ، سپس برای خاموش شدن و درجه حرارت کم دم تر گرم می شود.
3. خاموش شدن دفع بعد از خنک شدن + درجه حرارت درجه حرارت پایین: بعد از کارآزمایی و خنک کننده آهسته ، قطعه کار طی دو مرحله گرمایش و خاموش شدن قرار می گیرد و به دنبال آن درجه حرارت کم درجه حرارت می شود.
ⅴ. عمل گرمای شیمیایی فولادها
1. تعریف عملیات حرارتی شیمیایی
عملیات حرارتی شیمیایی یک فرآیند تصفیه حرارتی است که در آن یک قطعه کار فولادی در یک محیط فعال خاص ، گرم شده و در دمای نگهدارنده قرار می گیرد و امکان اتم های فعال در محیط را فراهم می کند تا در سطح قطعه کار پخش شوند. این ترکیب شیمیایی و ریزساختار سطح قطعه کار را تغییر می دهد و از این طریق خواص آن را تغییر می دهد.
2. فرآیند عظیم عملیات حرارتی شیمیایی
تجزیه: در حین گرمایش ، محیط فعال تجزیه می شود و اتمهای فعال را آزاد می کند.
جذب: اتمهای فعال توسط سطح فولاد جذب می شوند و در محلول جامد فولاد حل می شوند.
انتشار: اتمهای فعال جذب و حل شده بر روی سطح فولاد به داخل فضای داخلی مهاجرت می کنند.
انواع سخت شدن سطح القایی
گرمایش القایی با فرکانس بالا
فرکانس فعلی: 300 k هرتز 250.
عمق لایه سخت: 2.0 ~ 2.0 میلی متر.
برنامه ها: چرخ دنده های ماژول متوسط و کوچک و شفت های کوچک و متوسط.
گرمایش القایی فرکانس B.Medium
فرکانس فعلی: 2500 ~ 8000 کیلوهرتز.
عمق لایه سخت: 2 ~ 10 میلی متر.
برنامه ها: شفت های بزرگتر و چرخ دنده های ماژول بزرگ و متوسط.
ج. گرمایش القایی فرکانس قدرت
فرکانس فعلی: 50 هرتز.
عمق لایه سخت: 15 ~ 15 میلی متر.
برنامه ها: قطعات کاری که به یک لایه سخت شده بسیار عمیق نیاز دارند.
3. سخت شدن سطح القایی
اصل اساسی سخت شدن سطح القایی
اثر پوستی:
هنگامی که جریان متناوب در سیم پیچ القایی باعث ایجاد جریان در سطح قطعه کار می شود ، اکثر جریان ناشی از آن در نزدیکی سطح متمرکز می شود ، در حالی که تقریباً هیچ جریان از قسمت داخلی قطعه کار عبور نمی کند. این پدیده به عنوان اثر پوست شناخته می شود.
اصل سخت شدن سطح القایی:
بر اساس اثر پوست ، سطح قطعه کار به سرعت در دمای آستنیتاسیون گرم می شود (در چند ثانیه به 800 ~ 1000 درجه سانتیگراد افزایش می یابد) ، در حالی که قسمت داخلی قطعه کار تقریباً گرم نشده است. سپس قطعه کار با پاشیدن آب خنک می شود و به سخت شدن سطح می رسد.
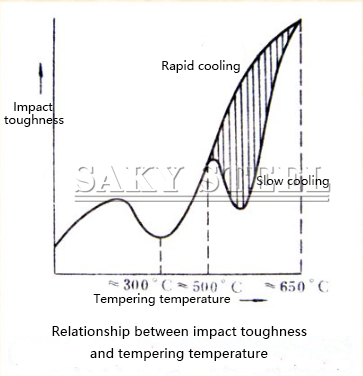
4.Temper Brittleness
شکنندگی معتدل در فولاد خاموش
شستشوی خویشاوند به پدیده ای اشاره دارد که در آن چقرمگی ضربه فولاد خاموش به طور قابل توجهی در هنگام دمای خاص کاهش می یابد.
نوع اول شکنندگی معتدل
دامنه دما: 250 درجه سانتیگراد تا 350 درجه سانتیگراد.
ویژگی ها: اگر فولاد خاموش در این محدوده دما فشرده شود ، به احتمال زیاد این نوع شکنندگی معتدل را توسعه می دهد ، که نمی تواند از بین برود.
راه حل: از فولاد خاموش شده در این محدوده دما خودداری کنید.
نوع اول شکنندگی معتدل همچنین به عنوان شکنندگی با درجه حرارت پایین یا شستشوی معتدل غیر قابل برگشت شناخته می شود.
tempering
1.Tempering یک فرآیند عملیات حرارتی نهایی است که از خاموش شدن پیروی می کند.
چرا فولادهای خاموش نیاز به معتدل دارند؟
ریزساختار پس از خاموش کردن: پس از خاموش شدن ، ریزساختار فولاد به طور معمول از مارتنزیت و آستنیت باقیمانده تشکیل شده است. هر دو فازهای قابل استفاده هستند و تحت شرایط خاصی دگرگون می شوند.
خواص مارتنزیت: مارتنزیت با سختی زیاد بلکه شستشوی زیاد (به ویژه در مارتنزیت سوزن کربن مانند) مشخص می شود ، که نیازهای عملکرد بسیاری را برای بسیاری از برنامه ها برآورده نمی کند.
ویژگی های تحول مارتنزیتیک: تبدیل به مارتنزیت خیلی سریع اتفاق می افتد. پس از خاموش شدن ، قطعه کار دارای فشارهای داخلی باقیمانده است که می تواند منجر به تغییر شکل یا ترک خوردگی شود.
نتیجه گیری: قطعه کار نمی تواند مستقیماً پس از خاموش شدن استفاده شود! برای کاهش فشارهای داخلی و بهبود سختی قطعه کار ، مزاج لازم است و آن را برای استفاده مناسب می کند.
2. اختلاف بین سخت بودن و ظرفیت سخت شدن:
سختگیری:
سخت افزاری به توانایی فولاد در دستیابی به عمق خاصی از سخت شدن (عمق لایه سخت شده) پس از خاموش شدن اشاره دارد. این بستگی به ترکیب و ساختار فولاد ، به ویژه عناصر آلیاژ آن و نوع فولاد دارد. سخت افزاری اندازه گیری است که چگونه فولاد می تواند در طول فرآیند فرونشست ضخامت خود را سخت کند.
سختی (ظرفیت سخت شدن):
سختی یا ظرفیت سخت شدن ، به حداکثر سختی که می تواند در فولاد پس از فرونشست حاصل شود ، اشاره دارد. این ماده تا حد زیادی تحت تأثیر میزان کربن فولاد است. میزان کربن بالاتر به طور کلی منجر به سختی بالقوه بالاتر می شود ، اما این می تواند توسط عناصر آلیاژ فولاد و اثربخشی روند فرونشست محدود شود.
3.HARDERABLITY فولاد
√ تداخل سخت بودن
سخت افزاری به توانایی فولاد در دستیابی به عمق خاصی از سخت شدن مارتنزیتیک پس از خاموش شدن از دمای آبشویی اشاره دارد. به عبارت ساده تر ، این توانایی فولاد برای تشکیل مارتنزیت در هنگام خاموش کردن است.
اندازه گیری سختگیری
اندازه سخت بودن با عمق لایه سخت شده به دست آمده در شرایط مشخص پس از خاموش کردن نشان داده شده است.
عمق لایه سخت: این عمق از سطح قطعه کار به منطقه ای است که ساختار آن نیمی از مارتنزیت است.
رسانه های فروپاشی مشترک:
• آب
ویژگی ها: اقتصادی با قابلیت خنک کننده قوی ، اما در نزدیکی نقطه جوش ، میزان خنک کننده بالایی دارد که می تواند منجر به خنک کننده بیش از حد شود.
کاربرد: به طور معمول برای فولادهای کربن استفاده می شود.
آب نمکی: محلول نمک یا قلیایی در آب ، که از ظرفیت خنک کننده بالاتری در دماهای بالا در مقایسه با آب برخوردار است ، و آن را برای فولادهای کربن مناسب می کند.
• روغن
ویژگی ها: میزان خنک کننده کندتر در دماهای پایین (در نزدیکی نقطه جوش) را فراهم می کند ، که به طور موثری تمایل به تغییر شکل و ترک خوردگی را کاهش می دهد ، اما توانایی خنک کننده کمتری را در دماهای بالا دارد.
کاربرد: مناسب برای فولادهای آلیاژ.
انواع: شامل روغن خاموش ، روغن دستگاه و سوخت دیزل.
زمان گرمایشی
زمان گرمایش شامل هر دو میزان گرمایش (زمان لازم برای رسیدن به دمای مورد نظر) و زمان نگهدارنده (زمان نگهداری در دمای هدف) است.
اصول تعیین زمان گرمایش: از توزیع دمای یکنواخت در طول قطعه ، چه در داخل و چه در خارج اطمینان حاصل کنید.
اطمینان حاصل کنید که از آستنیت کامل و اینکه آستنیت تشکیل شده یکنواخت و خوب است.
مبنای تعیین زمان گرمایش: معمولاً با استفاده از فرمولهای تجربی تخمین زده می شود یا از طریق آزمایش تعیین می شود.
رسانه های خاموش
دو جنبه اصلی:
A.COOLING نرخ: نرخ خنک کننده بالاتر باعث شکل گیری مارتنزیت می شود.
B.Residual Stress: میزان خنک کننده بالاتر باعث افزایش استرس باقیمانده می شود ، که می تواند منجر به تمایل بیشتر برای تغییر شکل و ترک خوردگی در قطعه کار شود.
ⅶ. normalizing
1. تعریف عادی سازی
عادی سازی یک فرآیند تصفیه حرارتی است که در آن فولاد در دمای 30 درجه سانتیگراد تا 50 درجه سانتیگراد بالاتر از دمای AC3 گرم می شود ، در آن دما نگه داشته می شود و سپس برای بدست آوردن ریزساختار نزدیک به حالت تعادل ، خنک می شود. در مقایسه با بازپخت ، عادی سازی سرعت خنک کننده سریع تری دارد و در نتیجه یک ساختار مروارید ظریف (P) و قدرت و سختی بالاتر ایجاد می شود.
2. هدف عادی سازی
هدف از عادی سازی شبیه به روش آنیل شدن است.
3. برنامه های عادی سازی
• سیمانیت ثانویه شبکه را از بین ببرید.
• به عنوان عملیات حرارتی نهایی برای قطعاتی که نیازهای کمتری دارند ، خدمت کنید.
• به عنوان یک عملیات حرارتی مقدماتی برای فولاد سازه کربن کم و متوسط برای بهبود ماشینکاری عمل کنید.
4. نوع آنیونی
نوع اول آنیل:
هدف و عملکرد: هدف این نیست که تحول فاز را القا کنیم بلکه انتقال فولاد از حالت نامتعادل به حالت متعادل است.
انواع:
• پخت انتشار: با هدف از بین بردن تفکیک ، همگن سازی ترکیب.
• بازپرداخت تبلور مجدد: با از بین بردن اثرات سخت افزاری کار ، انعطاف پذیری را بازیابی می کند.
• بازپخت تسکین استرس: بدون تغییر ریزساختار ، تنش های داخلی را کاهش می دهد.
نوع دوم آنیل:
هدف و عملکرد: با هدف تغییر ریزساختار و خصوصیات ، دستیابی به ریزساختار تحت سلطه مروارید. این نوع همچنین تضمین می کند که توزیع و مورفولوژی مروارید ، فریت و کاربیدها نیازهای خاصی را برآورده می کنند.
انواع:
• بازپخت کامل: فولاد را بالاتر از دمای AC3 گرم می کند و سپس به آرامی آن را خنک می کند تا یک ساختار مروارید یکنواخت تولید کند.
• بازپخت ناقص: فولاد را بین دمای AC1 و AC3 گرم می کند تا تا حدی ساختار را تغییر دهد.
• بازپخت ایزوترمال: فولاد را به بالای AC3 گرم می کند و به دنبال آن خنک کننده سریع به دمای ایزوترمال و نگه داشتن برای دستیابی به ساختار مورد نظر می رسد.
• پخت کروی: یک ساختار کاربید کروی تولید می کند و باعث بهبود ماشینکاری و چقرمگی می شود.
ⅷ.1. تعریف عملیات حرارتی
عملیات حرارتی به فرایندی اشاره دارد که در آن فلز گرم می شود ، در دمای خاصی نگه داشته می شود و سپس در حالت جامد خنک می شود تا ساختار داخلی و ریزساختار آن را تغییر دهد و از این طریق به خواص مورد نظر دست یابد.
2. ویژگی های عملیات حرارتی
عملیات حرارتی شکل قطعه کار را تغییر نمی دهد. در عوض ، ساختار داخلی و ریزساختار فولاد را تغییر می دهد ، که به نوبه خود خصوصیات فولاد را تغییر می دهد.
3. هدف از عملیات حرارتی
هدف از عملیات حرارتی بهبود خصوصیات مکانیکی یا پردازش فولاد (یا قطعات کاری) ، استفاده کامل از پتانسیل فولاد ، افزایش کیفیت قطعه کار و افزایش عمر خدمات آن است.
4. نتیجه گیری کلید
این که آیا خواص یک ماده از طریق عملیات حرارتی قابل بهبود است ، بستگی به این امر دارد که آیا تغییراتی در ریزساختار و ساختار آن در طی فرآیند گرمایش و سرمایش وجود دارد.
زمان پست: اوت 19-2024