Ⅰ.Das grundlegendes Konzept der Wärmebehandlung.
A.Das grundlegendes Konzept der Wärmebehandlung.
Die Grundelemente und Funktionen vonWärmebehandlung:
1. Erhitzen
Ziel ist es, eine einheitliche und feine Austenitstruktur zu erhalten.
2. Holding
Ziel ist es, sicherzustellen, dass das Werkstück gründlich erhitzt wird und die Dekarburisierung und Oxidation verhindern.
3. Cooling
Ziel ist es, Austenit in verschiedene Mikrostrukturen zu verwandeln.
Mikrostrukturen nach Wärmebehandlung
Während des Kühlprozesses nach Erhitzen und Halten verwandelt sich der Austenit je nach Kühlrate in verschiedene Mikrostrukturen. Verschiedene Mikrostrukturen zeigen unterschiedliche Eigenschaften.
B. das grundlegende Konzept der Wärmebehandlung.
Klassifizierung basierend auf Heiz- und Kühlmethoden sowie der Mikrostruktur und den Eigenschaften von Stahl
1
2. Oberfläche Wärmebehandlung: Oberflächenlöschung, Induktionsheizungsoberflächenlöschung, Flammenheizungsoberflächenlöschung, elektrische Kontaktheizungsoberflächenlöschung.
3. Chemische Wärmebehandlung: Kohlensäure, Nitring, Karbonitridieren.
4. Andere Wärmebehandlungen: kontrollierte Atmosphäre -Wärmebehandlung, Vakuumwärmebehandlung, Deformationswärmebehandlung.
C. Critische Temperatur von Stählen
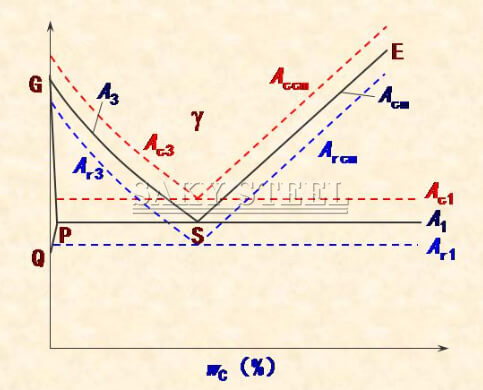
Die kritische Transformationstemperatur von Stahl ist eine wichtige Grundlage für die Bestimmung der Erwärmungs-, Halte- und Kühlprozesse während der Wärmebehandlung. Es wird durch das Eisen-Kohlenstoff-Phasendiagramm bestimmt.
Schlussfolgerung:Die tatsächliche kritische Transformationstemperatur von Stahl bleibt immer hinter der theoretischen kritischen Transformationstemperatur zurück. Dies bedeutet, dass beim Erhitzen eine Überhitzung erforderlich ist und während des Abkühlens eine Unterkühlung erforderlich ist.
Ⅱ.Annealing und Normalisierung von Stahl
1. Definition des Glühens
Das Glühen beinhaltet das Erhitzen von Stahl auf eine Temperatur über oder unter dem kritischen Punkt, das ihn bei dieser Temperatur hält, und kühlt ihn dann langsam im Ofen, um eine Struktur in der Nähe des Gleichgewichts zu erreichen.
2. Zweck des Glühens
①Anjust Härte zum Bearbeitung: Erreichen maschineller Härte im Bereich von HB170 ~ 230.
②Relief Restspannung: verhindert Deformation oder Risse während der nachfolgenden Prozesse.
③Refine Getreidestruktur: Verbessert die Mikrostruktur.
④ Vorbereitung für die endgültige Wärmebehandlung: Erhält körnige (sphäroidisierte) Perliten zum anschließenden Löschung und Temperieren.
3.Spheroidisierende Glühen
Prozessspezifikationen: Die Heiztemperatur liegt in der Nähe des AC₁ -Punktes.
Zweck: Um den Zementit oder die Carbide im Stahl zu sphäroidieren, führt er zu körnigem (sphäroidisiertem) Perlit.
Anwendbarer Bereich: Wird für Stähle mit eutektoiden und überdurchschnittlichen Zusammensetzungen verwendet.
4. Diffusenglühen (Homogenisieren von Glühen)
Prozessspezifikationen: Die Heiztemperatur liegt geringfügig unter der Solvus -Linie im Phasendiagramm.
Zweck: Segregation zu beseitigen.
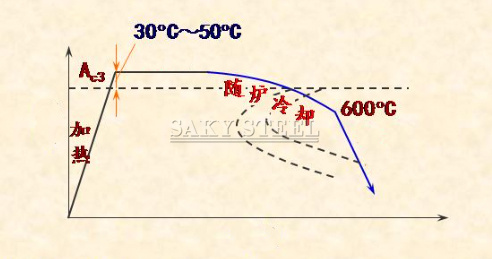
①forn-KohlenstoffstahlBei einem Kohlenstoffgehalt von weniger als 0,25%wird die Normalisierung gegenüber Tempern als vorbereitende Wärmebehandlung bevorzugt.
②Für mit mittlerem Kohlenstoffstahl mit Kohlenstoffgehalt zwischen 0,25% und 0,50%, entweder Tempern oder Normalisierung kann als vorbereitende Wärmebehandlung verwendet werden.
③ Für mittel- bis hohe Kohlenstoffstahl mit Kohlenstoffgehalt zwischen 0,50% und 0,75% wird ein volles Tempern empfohlen.
④For High-KohlenstoffstahlMit einem Kohlenstoffgehalt von mehr als 0,75%wird die Normalisierung zunächst verwendet, um das Netzwerk Fe₃C zu beseitigen, gefolgt von Sphäroidisierungsgeschäften.
Ⅲ.
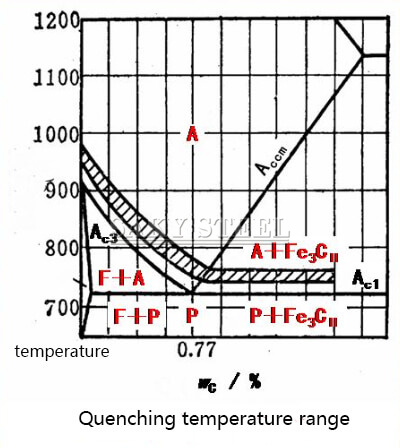
A. durchsucht
1. Definition des Löschens: Das Löschen beinhaltet das Erhitzen von Stahl auf eine bestimmte Temperatur über dem AC₃- oder AC₁ -Punkt, hält ihn bei dieser Temperatur und kühlt ihn dann mit einer Geschwindigkeit, die größer als die kritische Kühlrate zur Bildung von Martensit ist.
2. Zweck des Löschens: Das Hauptziel ist es, Martensit (oder manchmal einen niedrigeren Bainit) zu erhalten, um die Härte und den Verschleiß Widerstand des Stahls zu erhöhen. Das Löschen ist eines der wichtigsten Wärmebehandlungsprozesse für Stahl.
3. Bestimmen Sie die Ablöstentemperaturen für verschiedene Arten von Stahl
Hypoutektoidstahl: AC₃ + 30 ° C bis 50 ° C
Eutektoid und Übererblattstahl: AC₁ + 30 ° C bis 50 ° C
Legierungsstahl: 50 ° C bis 100 ° C über der kritischen Temperatur
4. Kühleigenschaften eines idealen Quenching -Mediums:
Langsames Abkühlen vor der "Nasen" -Temperatur: Um die thermische Belastung ausreichend zu reduzieren.
Hohe Kühlkapazität in der Nähe der "Nasen" -Temperatur: Um die Bildung nicht-marensitischer Strukturen zu vermeiden.
Langsame Kühlung in der Nähe von M₅ Point: Um den durch martensitischen Transformation induzierten Stress zu minimieren.
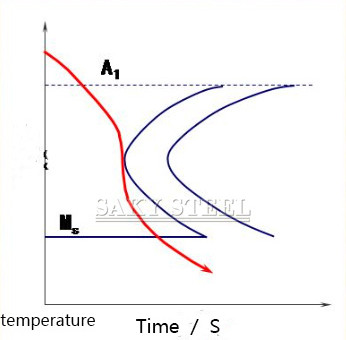
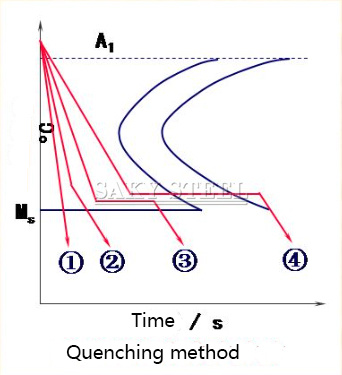
5. Methoden und deren Eigenschaften: ihre Eigenschaften:
①Simple Quenching: Einfach zu bedienen und für kleine, einfache Werkstücke geeignet. Die resultierende Mikrostruktur ist Martensit (M).
②ouble Quenching: komplexer und schwer zu kontrollierter, verwendet für komplexförmige Kohlenstoffstahl- und größere legierte Stahlwerkstücke. Die resultierende Mikrostruktur ist Martensit (M).
③broken locking: Ein komplexeres Prozess, der für große, komplexförmige legierte Stahlwerkstücke verwendet wird. Die resultierende Mikrostruktur ist Martensit (M).
④ isothermisches Quenching: Wird für kleine, komplexförmige Werkstücke mit hohen Anforderungen verwendet. Die resultierende Mikrostruktur ist ein niedrigerer Bainit (B).
6. Faktoren, die die Aushärten beeinflussen
Das Ausmaß der Härtlichkeit hängt von der Stabilität des Supercooled Austenit in Stahl ab. Je höher die Stabilität des Supercooled Austenit ist, desto besser ist die Härtbarkeit und umgekehrt.
Faktoren, die die Stabilität von Supercooled Austenit beeinflussen:
Position des C-Kurve: Wenn sich das C-Kurve nach rechts verlagert, nimmt die kritische Kühlrate für das Löschen ab und verbessert die Härterbarkeit.
Schlussfolgerung:
Jeder Faktor, der das C-Kurve nach rechts verschiebt, erhöht die Härtbarkeit des Stahls.
Hauptfaktor:
Chemische Zusammensetzung: Mit Ausnahme von Cobalt (CO) erhöhen alle in Austenit gelösten Legierungselemente die Härtebarkeit.
Je näher der Kohlenstoffgehalt der eutektoiden Zusammensetzung in Kohlenstoffstahl liegt, desto mehr verschiebt sich der C-Kurve nach rechts und desto höher ist die Härtbarkeit.
7. Bestimmung und Darstellung von Härtbarkeit
①end Quench Härtbarkeitstest: Die Härtbarkeit wird unter Verwendung der End-Treenench-Testmethode gemessen.
②kritisches Quenchdurchmesserverfahren: Der kritische Quenchdurchmesser (D₀) repräsentiert den maximalen Stahldurchmesser, der in einem bestimmten Quench -Medium vollständig verhärtet werden kann.
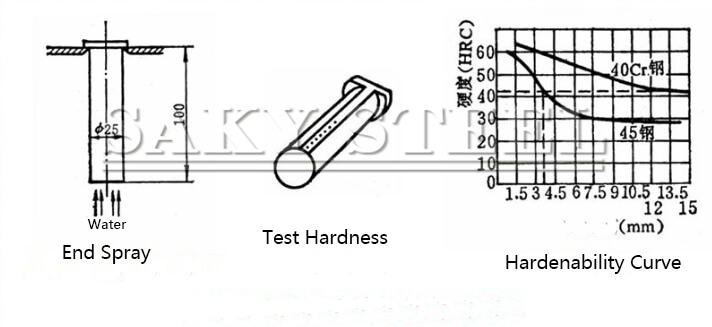
B. Tempering
1. Definition der Temperierung
Das Temperieren ist ein Wärmebehandlungsprozess, bei dem der Stahl gelöscht, auf eine Temperatur unterhalb des A₁ -Punktes erwärmt, bei dieser Temperatur gehalten und dann auf Raumtemperatur abgekühlt wird.
2. Zweck des Temperierens
Reduzieren oder beseitigen Sie die Restspannung: verhindert die Verformung oder das Knacken des Werkstücks.
Reduzieren oder beseitigen Sie den Rest -Austenit: Stabilisiert die Abmessungen des Werkstücks.
Beseitigen Sie die Bröcklichkeit von gelösten Stahl: Passt die Mikrostruktur und Eigenschaften an, um die Anforderungen des Werkstücks zu erfüllen.
Wichtiger Hinweis: Stahl sollte nach dem Löschen unverzüglich gemildert werden.
3. Temperierungsprozesse
1. Temperieren
Zweck: Reduzieren Sie den Stress ab, um die Zähigkeit des Werkstücks zu verbessern und eine hohe Härte zu erreichen und Widerstand zu tragen.
Temperatur: 150 ° C ~ 250 ° C.
Leistung: Härte: HRC 58 ~ 64. Hohe Härte und Verschleißfestigkeit.
Anwendungen: Werkzeuge, Formen, Lager, Kohlenstoffteile und oberflächenhärtete Komponenten.
2. Hochtemperament
Zweck: Um hohe Zähigkeit zusammen mit ausreichender Stärke und Härte zu erreichen.
Temperatur: 500 ° C ~ 600 ° C.
Leistung: Härte: HRC 25 ~ 35. Gute mechanische Gesamteigenschaften.
Anwendungen: Wellen, Zahnräder, Stangenverbindungsstäbe usw.
Thermische Verfeinerung
Definition: Das Löschen von Hochtemperaturtemperaturen wird als thermische Raffinierung oder einfach Temperierung bezeichnet. Stahl, der durch diesen Prozess behandelt wird, hat eine hervorragende Gesamtleistung und wird weit verbreitet.
Ⅳ. Oberflächen -Wärmebehandlung von Stahl
A. Oberflächenlöschung von Stählen
1. Definition der Oberflächenhärtung
Die Oberflächenhärtung ist ein Wärmebehandlungsprozess, um die Oberflächenschicht eines Werkstücks zu stärken, indem es schnell erhitzt wird, um die Oberflächenschicht in Austenit zu verwandeln und sie dann schnell abzukühlen. Dieser Prozess wird durchgeführt, ohne die chemische Zusammensetzung des Stahls oder die Kernstruktur des Materials zu verändern.
2. Materialien, die zur Härtung von Oberflächenhärten und nach der Härten verwendet werden
Materialien, die zur Oberflächenhärtung verwendet werden
Typische Materialien: mittlerer Kohlenstoffstahl und mittelgroßer Kohlenstofflegierungstahl.
Vorbehandlung: Typischer Prozess: Temperieren. Wenn die Kerneigenschaften nicht kritisch sind, kann stattdessen die Normalisierung verwendet werden.
Nachhärtungsstruktur
Oberflächenstruktur: Die Oberflächenschicht bildet typischerweise eine verhärtete Struktur wie Martensit oder Bainit, die eine hohe Härte und einen hohen Verschleißfestigkeit bietet.
Kernstruktur: Der Kern des Stahls behält im Allgemeinen seine ursprüngliche Struktur bei, z. Dies stellt sicher, dass der Kern eine gute Zähigkeit und Stärke beibehält.
B. Charakteristik der Härtung der Induktionsoberfläche
1. Hohe Erwärmungstemperatur und schneller Temperaturanstieg: Die Härtung der Induktionsoberfläche beinhaltet typischerweise hohe Heiztemperaturen und schnelle Heizraten, die innerhalb kurzer Zeit eine schnelle Erwärmung ermöglichen.
2. FINE Austenitkornstruktur in der Oberflächenschicht: Während des schnellen Erhitzens und des anschließenden Löschungsprozesses bildet die Oberflächenschicht feine Austenitkörner. Nach dem Löschen besteht die Oberfläche hauptsächlich aus feinem Martensit, wobei die Härte typischerweise 2-3 Stunden höher ist als das konventionelle Löschen.
3. Gute Oberflächenqualität: Aufgrund der kurzen Heizzeit ist die Werkstückoberfläche weniger anfällig für Oxidation und Dekarburisierung, und die durch Quenching induzierte Deformation wird minimiert, was eine gute Oberflächenqualität gewährleistet.
4. Hohe Müdigkeitsstärke: Die martensitische Phasenumwandlung in der Oberflächenschicht erzeugt Druckspannung, die die Ermüdungsfestigkeit des Werkstücks erhöht.
5. Hochproduktionseffizienz: Die Härtung der Induktionsoberfläche eignet sich für die Massenproduktion und bietet eine hohe operative Effizienz.
C. Klassifizierung der chemischen Wärmebehandlung
Kohlensäure, Kohlensäure, Kohlensäure, Chromisierung, Silikonisierung, Silikonisierung, Silikonisierung, Karbonitridieren, Borokarburisierung
D.Gas Carburisierung
Gaskohlenhydrate ist ein Prozess, bei dem ein Werkstück in einen versiegelten Gasverkostofen gelegt und auf eine Temperatur erhitzt wird, die den Stahl in Austenit umwandelt. Anschließend wird ein Kohlensäuremittel in den Ofen getropft, oder es wird direkt in den Ofen eingeführt, sodass Kohlenstoffatome in die Oberflächenschicht des Werkstücks diffundieren können. Dieser Prozess erhöht den Kohlenstoffgehalt (WC%) auf der Werkstückoberfläche.
√carburisierende Agenten:
• Kohlenstoffreiche Gase: wie Kohlegas, verflüssigtes Erdölgas (LPG) usw.
• organische Flüssigkeiten: wie Kerosin, Methanol, Benzol usw.
√Carburisierungsprozessparameter:
• Kohlensäuretemperatur: 920 ~ 950 ° C.
• Zeitverschlüsse: Hängt von der gewünschten Tiefe der Kohlenhydratschicht und der Kohlensäuretemperatur ab.
E.Heat -Behandlung nach Kohlensäure
Stahl muss nach der Kohlensäure einer Wärmebehandlung unterzogen werden.
Wärmebehandlungsprozess nach Kohlensäure:
√ durchdringte + niedrige Temperaturtemperatur
1. Löschung nach Vorkühlung + Temperatur mit niedrigem Temperatur: Das Werkstück wird von der Kohlenhydrat-Temperatur bis knapp über der AR₁-Temperatur des Kerns und dann sofort gelöscht, gefolgt von Temperaturen mit niedriger Temperatur bei 160 ~ 180 ° C.
2. SINGLE-Löschen nach Vorkühlung + Temperaturtemperaturen mit niedrigem Temperatur: Nach dem Kohlensäure wird das Werkstück langsam auf Raumtemperatur abgekühlt und dann zum Quenchieren und Temperatur mit niedriger Temperatur aufgewärmt.
3. Nach dem Vorkühlung + Temperaturtemperatur: Nach dem Kohlensäure und langsamer Abkühlung wird das Werkstück zwei Stufen des Erhitzens und Quenchierens erfüllt, gefolgt von Temperaturen mit niedrigem Temperatur.
Ⅴ.chemische Wärmebehandlung von Stählen
1. Definition der chemischen Wärmebehandlung
Die chemische Wärmebehandlung ist ein Wärmebehandlungsprozess, bei dem ein Stahlwerkstück in ein spezifisches aktives Medium gelegt, erhitzt und bei Temperatur gehalten wird, wodurch die aktiven Atome im Medium in die Oberfläche des Werkstücks diffundieren können. Dies verändert die chemische Zusammensetzung und Mikrostruktur der Oberfläche des Werkstücks und verändert damit ihre Eigenschaften.
2. Grund für chemische Wärmebehandlung
Zersetzung: Während des Erhitzens zersetzt sich das aktive Medium, die aktive Atome freisetzen.
Absorption: Die aktiven Atome werden von der Oberfläche des Stahls adsorbiert und in die feste Lösung des Stahls auflösen.
Diffusion: Die aktiven und auf der Oberfläche des Stahls gelösten aktiven Atome wandern in den Innenraum.
Arten von Induktionsoberflächenhärten
A.HOH-Frequenz-Induktionsheizung
Stromfrequenz: 250 ~ 300 kHz.
Härtete Schichttiefe: 0,5 ~ 2,0 mm.
Anwendungen: mittlere und kleine Modul Zahnräder und kleine bis mittelgroße Wellen.
B.Medium-Frequenz-Induktionsheizung
Stromfrequenz: 2500 ~ 8000 kHz.
Härtete Schichttiefe: 2 ~ 10 mm.
Anwendungen: Größere Wellen und große bis mittlere Modulgänge.
C. Power-Frequenz-Induktionsheizung
Stromfrequenz: 50 Hz.
Härtete Schichttiefe: 10 ~ 15 mm.
Anwendungen: Werkstücke, die eine sehr tief gehärtete Schicht benötigen.
3. Härtung der Induktionsoberfläche
Grundprinzip der Härtung der Induktionsoberfläche
Hautwirkung:
Wenn der Wechselstrom in der Induktionsspule einen Strom auf der Oberfläche des Werkstücks induziert, wird der Großteil des induzierten Stroms in der Nähe der Oberfläche konzentriert, während fast kein Strom durch das Innere des Werkstücks fließt. Dieses Phänomen ist als Hauteffekt bekannt.
Prinzip der Härtung der Induktionsoberfläche:
Basierend auf dem Hauteffekt wird die Oberfläche des Werkstücks schnell auf die Austenitisierungstemperatur erhitzt (steigt in wenigen Sekunden auf 800 ~ 1000 ° C), während das Innere des Werkstücks fast nicht geschafft bleibt. Das Werkstück wird dann durch Wassersprühen abgekühlt, wodurch Oberflächenhärtung erreicht wird.
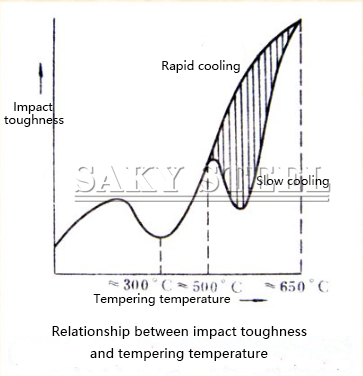
4. Tempere Brödelheit
Sprödigkeit in gequenchter Stahl temperiert
Temperierende Brödigkeit räumen auf das Phänomen, bei dem die Aufprallzählung von gelösten Stahl bei bestimmten Temperaturen signifikant abnimmt.
Erste Art der Temperierung der Sprödigkeit
Temperaturbereich: 250 ° C bis 350 ° C.
Merkmale: Wenn der Stahl in diesem Temperaturbereich gemildert ist, entwickelt es sehr wahrscheinlich, dass diese Art von temperamentvoller Sprödigkeit nicht beseitigt werden kann.
Lösung: Vermeiden Sie das Temperaturstahl in diesem Temperaturbereich.
Die erste Art der Temperierung ist auch als Temperatur mit niedrigem Temperatur oder irreversible Temperaturbrötchen bekannt.
Ⅵ.Tempering
1. Tempering ist ein endgültiger Wärmebehandlungsprozess, der das Löschen folgt.
Warum brauchen Quench -Stähle Temperierung?
Mikrostruktur nach dem Löschen: Nach dem Löschen besteht die Mikrostruktur des Stahls typischerweise aus Martensit und Restenit. Beide sind metastabile Phasen und transformieren unter bestimmten Bedingungen.
Eigenschaften von Martensit: Martensit ist durch hohe Härte, aber auch hohe Sprödigkeit gekennzeichnet (insbesondere in mit hohem Kohlenstoffnadelardersit), was den Leistungsanforderungen für viele Anwendungen nicht entspricht.
Merkmale der martensitischen Transformation: Die Transformation in Martensit tritt sehr schnell auf. Nach dem Löschen weist das Werkstück verbleibende interne Belastungen auf, die zu Verformungen oder Rissen führen können.
Schlussfolgerung: Das Werkstück kann nicht direkt nach dem Löschen verwendet werden! Temperierung ist erforderlich, um interne Belastungen zu reduzieren und die Zähigkeit des Werkstücks zu verbessern, wodurch es für den Einsatz geeignet ist.
2. Unterscheidung zwischen Härtbarkeit und Härtungskapazität:
Härtbarkeit:
Die Härtbarkeit bezieht sich auf die Fähigkeit von Stahl, nach dem Löschen eine gewisse Härtungstiefe (die Tiefe der gehärteten Schicht) zu erreichen. Es hängt von der Zusammensetzung und Struktur des Stahls ab, insbesondere ihren Legierungselementen und der Art des Stahls. Härtbarkeit ist ein Maß dafür, wie gut der Stahl während seiner Dicke während des Löschvorgangs härten kann.
Härte (Härtungskapazität):
Härte oder Härtungskapazität bezieht sich auf die maximale Härte, die nach dem Löschen im Stahl erreicht werden kann. Es wird größtenteils vom Kohlenstoffgehalt des Stahls beeinflusst. Ein höherer Kohlenstoffgehalt führt im Allgemeinen zu einer höheren potenziellen Härte, dies kann jedoch durch die Legierungselemente des Stahls und die Wirksamkeit des Quenching -Prozesses begrenzt werden.
3. Hardenbarkeit von Stahl
√konzept der Härtbarkeit
Die Härtbarkeit bezieht sich auf die Fähigkeit von Stahl, nach dem Löschen der Austenit -Temperatur eine bestimmte martensitische Härtung zu erreichen. Einfacher ist es die Fähigkeit von Stahl, beim Löschen Martensit zu bilden.
Messung der Härtbarkeit
Die Größe der Härten wird durch die Tiefe der gehärteten Schicht angezeigt, die nach dem Löschen unter bestimmten Bedingungen erhalten wurde.
Härtete Schichttiefe: Dies ist die Tiefe von der Oberfläche des Werkstücks bis zur Region, in der die Struktur halb Martensit ist.
Gemeinsame Quenching -Medien:
•Wasser
Eigenschaften: Wirtschaftlich mit starker Kühlfähigkeit, haben jedoch eine hohe Kühlrate in der Nähe des Siedepunkts, was zu einer übermäßigen Kühlung führen kann.
Anwendung: In der Regel für Kohlenstoffstähle verwendet.
Salzwasser: Eine Lösung von Salz oder Alkali in Wasser, das eine höhere Kühlkapazität bei hohen Temperaturen im Vergleich zu Wasser aufweist, wodurch es für Kohlenstoffstähle geeignet ist.
•Öl
Merkmale: Bietet eine langsamere Kühlrate bei niedrigen Temperaturen (in der Nähe des Siedepunkts), was die Tendenz zur Verformung und zum Knacken effektiv verringert, jedoch bei hohen Temperaturen eine geringere Kühlfähigkeit aufweist.
Anwendung: Geeignet für Legierungsstähle.
Typen: Beinhaltet das Löschen von Öl, Maschinenöl und Dieselkraftstoff.
Heizzeit
Die Heizzeit besteht sowohl aus der Heizrate (Zeit, die benötigt wird, um die gewünschte Temperatur zu erreichen) als auch aus der Haltezeit (die Zeit bei der Zieltemperatur gehalten).
Prinzipien zur Bestimmung der Heizzeit: Gewährleisten Sie eine gleichmäßige Temperaturverteilung im gesamten Werkstück, sowohl innerhalb als auch nach außen.
Stellen Sie sicher, dass die vollständige Austenitisierung und der gebildete Austenit einheitlich und fein ist.
Basis zur Bestimmung der Heizzeit: In der Regel unter Verwendung von empirischen Formeln geschätzt oder durch Experimentieren bestimmt.
Medien löschen
Zwei Schlüsselaspekte:
A.Cooling -Rate: Eine höhere Kühlrate fördert die Bildung von Martensit.
B. Residual Stress: Eine höhere Kühlrate erhöht die Restspannung, was zu einer größeren Tendenz zur Verformung und zum Riss im Werkstück führen kann.
Ⅶ..normalisieren
1. Definition der Normalisierung
Die Normalisierung ist ein Wärmebehandlungsprozess, bei dem Stahl auf eine Temperatur von 30 ° C bis 50 ° C über der AC3-Temperatur erhitzt, bei dieser Temperatur gehalten und dann luftkühlt, um eine Mikrostruktur in der Nähe des Gleichgewichtszustands zu erhalten. Im Vergleich zum Glühen hat die Normalisierung eine schnellere Kühlrate, was zu einer feineren Perlitstruktur (P) und einer höheren Festigkeit und Härte führt.
2. Zweck der Normalisierung
Der Zweck der Normalisierung ähnelt dem von Tempern.
3. Normalisierungsanwendungen
• Beseitigen Sie vernetzte Sekundärzementit.
• dienen als endgültige Wärmebehandlung für Teile mit geringeren Anforderungen.
• Wir wirken als vorbereitende Wärmebehandlung für niedrige und mittelgroße Kohlenstoffstruktur, um die Bearbeitbarkeit zu verbessern.
4. Typen des Tempers
Erste Art des Glühens:
Zweck und Funktion: Ziel ist es nicht, die Phasenumwandlung zu induzieren, sondern den Stahl von einem unausgeglichenen Zustand in einen ausgewogenen Zustand zu wechseln.
Typen:
• Diffusionsglühen: Ziel ist es, die Zusammensetzung durch Eliminierung der Segregation zu homogenisieren.
• Rekristallisation Annealing: Stellt die Duktilität wieder her, indem die Auswirkungen der Arbeitenhärten beseitigt werden.
• Stressabbau Glühen: Reduziert die inneren Belastungen, ohne die Mikrostruktur zu verändern.
Zweite Art des Glühens:
Zweck und Funktion: Ziel, die Mikrostruktur und Eigenschaften zu ändern und eine von Pearlit dominierte Mikrostruktur zu erreichen. Dieser Typ stellt auch sicher, dass die Verteilung und Morphologie von Pearlit, Ferrit und Carbiden den spezifischen Anforderungen entspricht.
Typen:
• Volles Glühen: Erhitzt den Stahl über der AC3 -Temperatur und kühlt ihn dann langsam ab, um eine gleichmäßige Perlitstruktur zu erzeugen.
• Unvollständiges Glühen: Erhitzt den Stahl zwischen AC1- und AC3 -Temperaturen, um die Struktur teilweise zu transformieren.
• Isothermisches Glühen: Erhitzt den Stahl auf oberhalb von AC3, gefolgt von einer schnellen Abkühlung auf eine isotherme Temperatur und Halten, um die gewünschte Struktur zu erreichen.
• Sphäroidisierende Glühen: Erzeugt eine kugelförmige Carbidstruktur, die die Bearbeitung und Zähigkeit verbessert.
Ⅷ.1.Definition der Wärmebehandlung
Die Wärmebehandlung bezieht sich auf ein Prozess, bei dem Metall erhitzt, bei einer bestimmten Temperatur gehalten und dann in einem festen Zustand gekühlt wird, um seine innere Struktur und Mikrostruktur zu verändern, wodurch die gewünschten Eigenschaften erreicht werden.
2. Charakteristik der Wärmebehandlung
Die Wärmebehandlung verändert nicht die Form des Werkstücks. Stattdessen verändert es die innere Struktur und Mikrostruktur des Stahls, was wiederum die Eigenschaften des Stahls verändert.
3. Wärmebehandlung einsetzen
Der Zweck der Wärmebehandlung besteht darin, die mechanischen oder verarbeitenden Eigenschaften von Stahl (oder Werkstücken) zu verbessern, das Potenzial des Stahls vollständig zu nutzen, die Qualität des Werkstücks zu verbessern und die Lebensdauer zu verlängern.
4. Key -Schlussfolgerung
Ob die Eigenschaften eines Materials durch die Wärmebehandlung verbessert werden können, hängt kritisch davon ab, ob sich während des Erhitzen- und Kühlprozesses Änderungen in der Mikrostruktur und Struktur gibt.
Postzeit: August-2024