1. overfladeskala -mærker
Hovedfunktioner: Forkert behandling af døsmedevil forårsage ru overflader og fiskeskala. Sådanne ru fiskeskala mærker produceres let, når man smeder austenitisk og martensitisk rustfrit stål.
Årsag: Lokal slimhinde membran forårsaget af ujævn smøring eller forkert valg af smøring og dårlig kvalitet af smøreolie.
2. fejlfejl
Hovedfunktioner: Den øverste del af smedningen er forkert justeret i forhold til den nedre del langs afskedningsoverfladen.
Årsag: Der er ingen afbalanceret forkert justeringslås på smedning af matrisen, eller matricen er ikke installeret korrekt, eller kløften mellem hammerhovedet og guide -skinnen er for stor.
3. Utilstrækkelig matrismedningsfejl
Hovedfunktioner: Størrelsen på den matricering øges i retningen vinkelret på afskedsfladen. Når størrelsen overstiger den størrelse, der er angivet på tegningen, vil der ikke være tilstrækkelig matricing.
Årsag: Stor størrelse, lav smedningstemperatur, overdreven slid af diehulrummet osv. Vil føre til utilstrækkelig tryk eller overdreven modstand på flashbroen, utilstrækkelig udstyrstonnage og overdreven billetvolumen.
4. Utilstrækkelig lokal fyldning
Hovedfunktioner: Det forekommer hovedsageligt i ribbenene, konvekse døde hjørner osv. Af matricerne, og toppen af fylddelen eller hjørnerne af smedningerne er ikke fyldt nok, hvilket gør konturet af smedningerne uklare
Årsag: Designet af præformering af hulrummet og blanking af hulhulen er urimelig, udstyret tonnage er lille, det tomme er ikke opvarmet nok, og metalfluiditeten er dårlig, hvilket kan forårsage denne defekt.
5. Støbningsstrukturrester
Hovedfunktioner: Hvis der er resterende støbestruktur, er forringelsens forlængelse og træthed ofte ukvalificerede. Fordi på lavmagnificeringsteststykket er strømlinjerne af den blokerede del af den resterende støbning ikke indlysende, og endda dendritiske produkter kan ses, som hovedsageligt vises i smedning ved hjælp af stålingotter som emner.
Årsag: På grund af utilstrækkelig smedningsforhold eller forkert smedningsmetode. Denne defekt reducerer ydelsen af smedningerne, især påvirkningssejhed og træthedsegenskaber.
6. Korninhomogenitet
Hovedfunktioner: kornene i nogle dele afsmedeer især grove, mens kornene i andre dele er mindre og danner ujævne korn. Legeringer med høj temperatur og varmebestandige stål er især følsomme over for korninhomogenitet.
Årsag: Den lave finale smedningstemperatur forårsager lokal arbejdshærdning af billet med høj temperaturlegering. Under sluknings- og opvarmningsprocessen vokser nogle korn alvorligt, eller den indledende smedningstemperatur er for høj, og deformationen er utilstrækkelig, hvilket får deformationsgraden af lokalområdet til at falde i kritisk deformation. Korns ujævnhed kan let føre til et fald i træthedens ydeevne og holdbarhed.
7. Foldede defekter
Hovedfunktioner: Strømlinjerne er bøjet ved foldene af lavmagnificeringsprøven, og foldene er ens i udseendet som revnerne. Hvis det er en revne, vil strømlinjerne blive skåret to gange. På højmagnificeringsprøven, i modsætning til bunden af revnen, oxideres de to sider alvorligt, og foldbunden er stump.
Årsag: Det er hovedsageligt forårsaget af for lidt foder, for meget reduktion eller for lille amboltfiletradius under tegningsprocessen med stangmedlemmer og krumtapaksel. Foldningsdefekter får det oxiderede overflademetal til at smelte sammen under smedningsprocessen.
8. Forkert smedning strømline distribution
Hovedfunktioner: Streamline -turbulens såsom strømlinje tilbagesvaling, hvirvelstrøm, afbrydelse og konvektion opstår, når smedningen er lav effekt.
Årsag: Forkert die -design, forkert valg af smedningsmetode, urimelig form og billetstørrelse.
9. Båndet struktur
Hovedfunktioner: En struktur, hvor andre strukturer eller ferritfaser i smedninger distribueres i bånd. Det eksisterer hovedsageligt i austenitisk-ferritisk rustfrit stål, semi-martensitisk stål og eutektoid stål.
Årsag: Dette er forårsaget af smedning af deformation, når to sæt dele sameksisterer. Det reducerer materialets tværgående plasticitetsindeks og er tilbøjelig til at revne langs ferritzonen eller grænsen mellem de to faser.
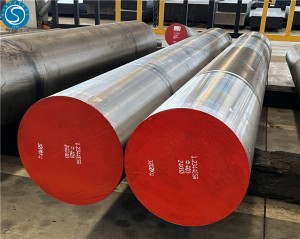
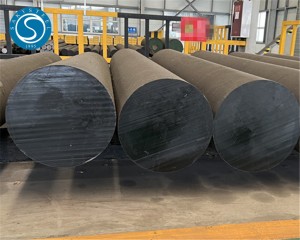
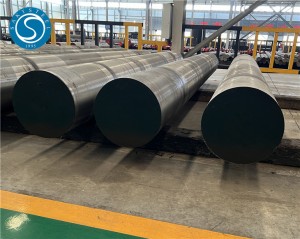
Posttid: juni-13-2024