Ⅰ. Основната концепция за топлинна обработка.
A. Основната концепция за топлинна обработка.
Основните елементи и функции натоплинна обработка:
1. Нагряване
Целта е да се получи еднаква и фина аустенитна структура.
2. Притежаване
Целта е да се гарантира, че детайлът се нагрява старателно и се предотвратява декарбуризация и окисляване.
3. охлаждане
Целта е да се трансформира аустенит в различни микроструктури.
Микроструктури след обработка на топлината
По време на процеса на охлаждане след нагряване и задържане, аустенитът се трансформира в различни микроструктури в зависимост от скоростта на охлаждане. Различните микроструктури проявяват различни свойства.
B. Основната концепция за топлинна обработка.
Класификация въз основа на методи за отопление и охлаждане, както и на микроструктурата и свойствата на стоманата
1. Конвенционална топлинна обработка (цялостна топлинна обработка): Температура, отгряване, нормализиране, гасене
2. Обработка на топлинната повърхност: Повърхностно гасене, индукционно отоплително повърхностно гасене, гасене на повърхността на отопление на пламъка, електрическо контактно отоплително повърхностно гасене.
3. Химическа топлинна обработка: карбуриране, азотиране, карбонитриране.
4. Други топлинни обработки: Третиране на топлинната атмосфера, обработка на топлината на топлината, деформация на топлинната обработка.
В. Критична температура на стоманите
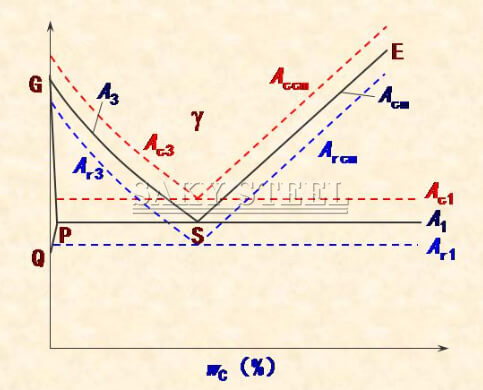
Критичната температура на трансформация на стоманата е важна основа за определяне на процесите на отопление, задържане и охлаждане по време на термична обработка. Определя се от диаграмата на желязо-въглеродния фаза.
Ключово заключение:Действителната критична температура на трансформация на стоманата винаги изостава от теоретичната критична температура на трансформация. Това означава, че по време на охлаждане е необходимо прегряване по време на отопление, а по време на охлаждане е необходимо.
Ⅱ. Отговаряне и нормализиране на стоманата
1. Определение за отгряване
Отгряването включва нагревателна стомана до температура над или под критичната точка, която я държи при тази температура, и след това бавно я охлажда, обикновено в пещта, за да се постигне структура, близка до равновесието.
2. Цел на отгряването
① Адюрт на твърдост за обработка: Постигане на твърдост на обработка в обхвата на HB170 ~ 230.
② Повпевяне на остатъчен стрес: предотвратява деформацията или напукване по време на следващите процеси.
③refine зърно структура: Подобрява микроструктурата.
④Препарация за окончателна топлинна обработка: Получава гранулиран (сфероидизиран) перлит за последващо гасене и закаляване.
3. Спероидизиращо отгряване
Спецификации на процеса: Температурата на отопление е близо до точката на AC₁.
Цел: Сфероидиране на циментита или карбидите в стоманата, което води до гранулиран (сфероидизиран) перлит.
Приложим диапазон: Използва се за стомани с евтектоидни и хиперетектоидни състави.
4. Отказ отгряване (хомогенизиращо отгряване)
Спецификации на процеса: Температурата на нагряване е малко под линията на Solvus на фазовата диаграма.
Цел: за премахване на сегрегацията.
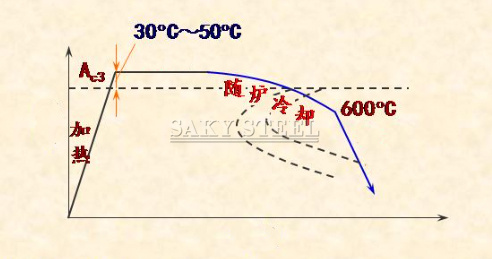
① за ниско-въглеродна стоманаСъс съдържание на въглерод по -малко от 0,25%, нормализирането се предпочита пред отгряването като подготвителна топлинна обработка.
За средновъглеродната стомана със съдържание на въглерод между 0,25% и 0,50%, отгряването или нормализирането може да се използва като подготвителна топлинна обработка.
③ За средно-въглеродна стомана със съдържание на въглерод между 0,50% и 0,75%, се препоръчва пълно отгряване.
④ за високо-въглеродна стоманаСъс съдържание на въглерод по -голямо от 0,75%, нормализирането се използва първо за елиминиране на мрежовия Fe₃c, последвано от сфероидизиране на отгряването.
Ⅲ. Впишаване и закаляване на стоманата
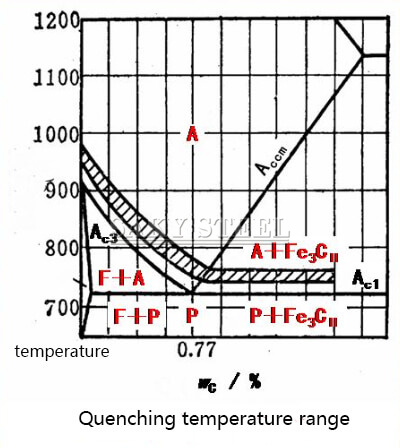
A.Перкиране
1. Определение на гасенето: гасенето включва отопление на стомана до определена температура над точката ac₃ или ac₁, като я държите при тази температура и след това я охлажда със скорост, по -голяма от критичната скорост на охлаждане, за да се образува мартензит.
2. Цел на гасенето: Основната цел е да се получи мартензит (или понякога по -нисък баинит), за да се увеличи твърдостта и устойчивостта на износване на стоманата. Угасването е един от най -важните процеси на пречистване на топлината за стомана.
3. Определяне на температурите на гасене за различни видове стомана
Хипоевтоидна стомана: Ac₃ + 30 ° C до 50 ° C
Евтектоид и хиперетектоидна стомана: ac₁ + 30 ° C до 50 ° C
Стоманена сплав: 50 ° C до 100 ° C над критичната температура
4. Охлаждащи характеристики на идеална гасеща среда:
Бавно охлаждане преди „носа“ температура: за достатъчно намаляване на топлинния стрес.
Висока охлаждаща способност в близост до температурата на носа: за да се избегне образуването на не-мартсенитни структури.
Бавно охлаждане в близост до M₅ точка: За да се сведе до минимум напрежението, предизвикано от мартензитната трансформация.
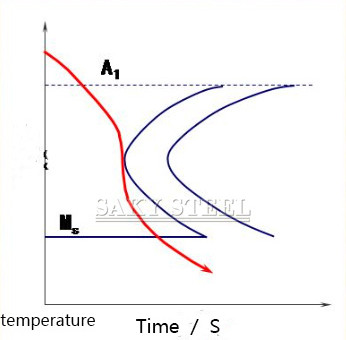
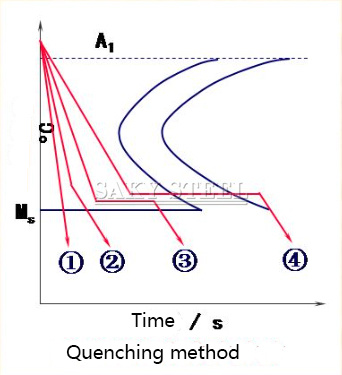
5. Методи за влагане и техните характеристики:
Simple гасене: Лесно за работа и подходящ за малки, прости форми на детайли. Получената микроструктура е мартензит (М).
② Двойно гасене: по-сложни и трудни за управление, използвани за сложна форма с високо съдържание на въглеродни и по-големи лети стоманени детайли. Получената микроструктура е мартензит (М).
③BROKEN WALECHING: По-сложен процес, използван за големи сложни сплави стоманени детайли. Получената микроструктура е мартензит (М).
④isothermal гасене: Използва се за малки, сложни детайли с високи изисквания. Получената микроструктура е по -нисък баинит (В).
6. Факторите, влияещи върху втвърдяване
Нивото на втвърдяване зависи от стабилността на свръхохладения аустенит в стоманата. Колкото по -висока е стабилността на свръхохладения аустенит, толкова по -добра е втвърдителност и обратно.
Фактори, влияещи върху стабилността на свръхохлаждания аустенит:
Позиция на C-кривата: Ако C-кюрвата се измести вдясно, критичната скорост на охлаждане за гасене намалява, подобрявайки втвърдяването.
Ключово заключение:
Всеки фактор, който измества C-кривата вдясно, увеличава втвърдимостта на стоманата.
Основен фактор:
Химичен състав: С изключение на кобалт (CO), всички легиращи елементи, разтворени в аустенит, увеличават втвърдяването.
Колкото по-близо е съдържанието на въглерод към евтектоидния състав в въглеродната стомана, толкова повече C-Curve се измества вдясно и толкова по-голяма е втвърдимостта.
7. Определяне и представяне на втвърдяване
①end Тест за втвърдяване на гасенето: Втвърдимост се измерва с помощта на метода на тест за крайно отслабване.
② Критичен метод на диаметър на гасенето: Критичният диаметър на гасенето (D₀) представлява максималния диаметър на стоманата, който може да бъде напълно втвърден в специфична гасираща среда.
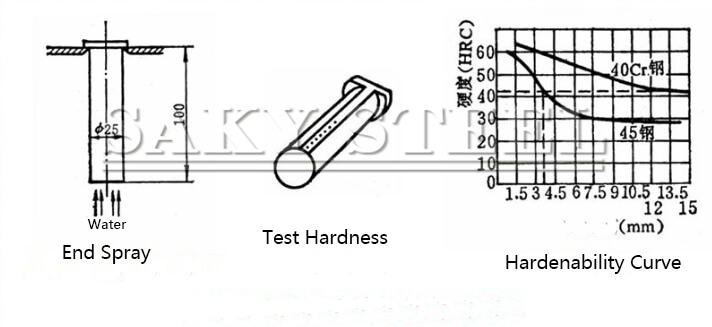
B. Намаляване
1. Определение на закаляването
Темпорането е процес на обработка на топлината, при който гасената стомана се претоплява до температура под точката на A₁, задържана при тази температура и след това се охлажда до стайна температура.
2. Цел на закаляването
Намаляване или елиминиране на остатъчния стрес: предотвратява деформацията или напукване на детайла.
Намалете или елиминирайте остатъчния аустенит: стабилизира размерите на детайла.
Елиминирайте бритлетието на гасената стомана: Настройва микроструктурата и свойствата, за да отговори на изискванията на детайла.
Важна забележка: Стоманата трябва да се закали незабавно след гасенето.
3. Процеси на натискане
1. слабо темпериране
Цел: За да се намали стресът на гасенето, да се подобри здравината на детайла и да се постигне висока твърдост и устойчивост на износване.
Температура: 150 ° C ~ 250 ° C.
Производителност: Твърда: HRC 58 ~ 64. Висока твърдост и устойчивост на износване.
Приложения: Инструменти, плесени, лагери, карбуризирани части и повърхностни компоненти.
2. Високо темпериране
Цел: Да се постигне висока здравина, заедно с достатъчна сила и твърдост.
Температура: 500 ° C ~ 600 ° C.
Производителност: Твърда: HRC 25 ~ 35. Добри общи механични свойства.
Приложения: валове, зъбни колела, свързващи пръти и т.н.
Термично рафиниране
Определение: Гасенето, последвано от високотемпературно закаляване, се нарича термично рафиниране или просто закаляване. Стоманената, обработена от този процес, има отлична цялостна производителност и се използва широко.
Ⅳ. Третирана топлинна обработка на стомана
A.Surface гасене на стомани
1. Определение на повърхностното втвърдяване
Повърхностното втвърдяване е процес на обработка на топлината, предназначен да укрепи повърхностния слой на детайла чрез бързо го нагрява, за да трансформира повърхностния слой в аустенит и след това бързо да го охлади. Този процес се осъществява, без да се променя химичния състав на стоманата или основната структура на материала.
2. Материали, използвани за повърхностно втвърдяване и структура след втвърдяване
Материали, използвани за повърхностно втвърдяване
Типични материали: Средно въглеродна стомана и стомана със среден въглеродна сплав.
Предварително лечение: Типичен процес: Темпорация. Ако основните свойства не са критични, вместо това може да се използва нормализиране.
Структура след втвърдяване
Повърхностна структура: Повърхностният слой обикновено образува втвърдена структура като мартензит или баинит, което осигурява висока твърдост и устойчивост на износване.
Основна структура: Ядрото на стоманата обикновено запазва първоначалната си структура, като перлит или закалено състояние, в зависимост от процеса на предварително лечение и свойствата на основния материал. Това гарантира, че ядрото поддържа добра здравина и сила.
B. Характеристики на втвърдяването на повърхностната повърхност
1. Висока температура на нагряване и бързо повишаване на температурата: Индукционното втвърдяване на повърхността обикновено включва високи температури на отопление и бързи скорости на нагряване, което позволява бързо отопление за кратко време.
2. ФИННА СТРУКТУРА НА ЗЪРНИЯТ АУСТЕНИТ В ПЪРВИЯТ СЛЕД: По време на бързото нагряване и последващия процес на гасене повърхностният слой образува фини аустенитни зърна. След гасене повърхността се състои предимно от фин мартензит, с твърдост обикновено 2-3 HRC по-висока от конвенционалното гасене.
3. Добро качество на повърхността: Поради краткото време на нагряване повърхността на детайла е по-малко предразположена към окисляване и декарбуризация, а индуцираната от гасене деформация е сведена до минимум, като се гарантира добро качество на повърхността.
4. МАГА СИЛА: Трансформацията на мартензитната фаза в повърхностния слой генерира натиск на напрежение, което увеличава силата на умората на детайла.
5. Висока ефективност на производството: Втвърдяването на повърхността на индукцията е подходящо за масово производство, предлагайки висока оперативна ефективност.
C. Класификация на химическата топлинна обработка
Карбуризационни, карбуризиращи, карбуризиращи, хромизиращи, силиконизиращи, силиконизиращи, силиконизиращи, карбонитридиране, борокарбуризиращи
D.Gas карбуризиране
Газовото карбуризиране е процес, при който детайлът се поставя в запечатана газова карбурираща пещ и се нагрява до температура, която превръща стоманата в аустенит. След това в пещта се въвежда карбуризиращ агент или директно се въвежда карбурираща атмосфера, което позволява на въглеродните атоми да дифундират в повърхностния слой на детайла. Този процес увеличава съдържанието на въглерод (WC%) на повърхността на детайла.
√ Карбуриращи агенти:
• Богати на въглерод газове: като въглищен газ, втечнен нефтен газ (пропан-бутан) и др.
• Органични течности: като керосин, метанол, бензен и др.
√ Карбуриране на параметрите на процеса:
• Температура на карбуриране: 920 ~ 950 ° C.
• Време за карбуризиране: Зависи от желаната дълбочина на карбуризирания слой и температурата на карбуризацията.
E. Намесете лечение след карбуризиране
Стоманата трябва да претърпи топлинна обработка след карбуризиране.
Процес на топлинна обработка след карбуризиране:
√quenching + нискотемпературно закаляване
1. Насочено гасене след предварително охлаждане + нискотемпературно темпериране: детайлът се охлажда предварително от температурата на карбуризацията до малко над температурата на AR₁ на ядрото и след това веднага се угасва, последвано от нискотемпературно темпериране при 160 ~ 180 ° C.
2.Сингъл гасене след предварително охлаждане + нискотемпературно закаляване: След карбуризиране, детайлът бавно се охлажда до стайна температура, след което се затоплява за гасене и нискотемпературно темпериране.
3. Двойно гасене след предварително охлаждане + нискотемпературно закаляване: След карбуриране и бавно охлаждане, детайлът претърпява два етапа на отопление и гасене, последвано от нискотемпературно темпериране.
Ⅴ. Чимична топлинна обработка на стомани
1. Определяне на химическата топлинна обработка
Химическата топлинна обработка е процес на обработка на топлината, при който стоманен детайл се поставя в специфична активна среда, нагрява се и се държи при температура, което позволява активните атоми в средата да дифундират в повърхността на детайла. Това променя химичния състав и микроструктурата на повърхността на детайла, като по този начин променя свойствата му.
2.Бозния процес на химическа топлинна обработка
Разлагане: По време на нагряване активната средна се разлага, освобождавайки активни атоми.
Абсорбция: Активните атоми се адсорбират от повърхността на стоманата и се разтварят в твърдия разтвор на стоманата.
Дифузия: Активните атоми се абсорбират и разтварят върху повърхността на стоманата мигрират във вътрешността.
Видове втвърдяване на повърхността на индукцията
A. Високо-честотна индукция отопление
Текуща честота: 250 ~ 300 kHz.
Втвърден дълбочина на слоя: 0,5 ~ 2,0 мм.
Приложения: Средни и малки модулни зъбни колела и малки до средни валове.
B.Медиево-честотно индукционно отопление
Текуща честота: 2500 ~ 8000 kHz.
Втвърден дълбочина на слоя: 2 ~ 10 mm.
Приложения: По -големи валове и големи до средни модулни предавки.
C. Нагряване на мощност-честота
Текуща честота: 50 Hz.
Втвърден дълбочина на слоя: 10 ~ 15 мм.
Приложения: Работни части, изискващи много дълбок втвърден слой.
3. Втвърдяване на повърхностната повърхност
Основен принцип на втвърдяване на повърхността на индукцията
Кожен ефект:
Когато редуващият се ток в индукционната намотка индуцира ток на повърхността на детайла, по -голямата част от индуцирания ток е концентрирана близо до повърхността, докато почти нито един ток не преминава през вътрешността на детайла. Това явление е известно като ефект на кожата.
Принцип на втвърдяване на повърхността на индукция:
Въз основа на ефекта на кожата, повърхността на детайла бързо се нагрява до аустенитизиращата температура (нарастваща до 800 ~ 1000 ° C за няколко секунди), докато вътрешността на детайла остава почти неотопляна. След това детайлът се охлажда чрез пръскане на вода, постигайки повърхностно втвърдяване.
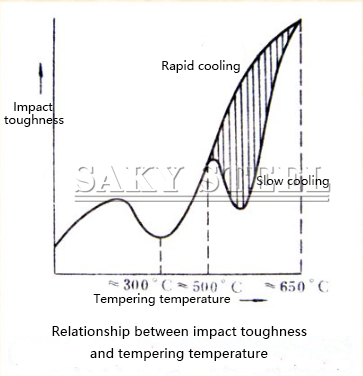
4. Темпер Бритълс
Темпорация на бритота в гасената стомана
Темурингът се отнася до явлението, при което въздействието на издръжливостта на гасената стомана значително намалява при темпериране при определени температури.
Първи тип нахлуване
Температурен диапазон: 250 ° C до 350 ° C.
Характеристики: Ако гасената стомана е темперирана в този температурен диапазон, е много вероятно да развие този тип нахлуване, което не може да бъде елиминирано.
Решение: Избягвайте темперирането на гасената стомана в този температурен диапазон.
Първият вид нахлуване на закаляване е известен още като нискотемпературна темпериране на прилепност или необратима темперираща бритълност.
Ⅵ
1. Напускането е краен процес на обработка на топлината, който следва гасенето.
Защо гасените стомани се нуждаят от закаляване?
Микроструктура след гасене: След гасене микроструктурата на стоманата обикновено се състои от мартензит и остатъчен аустенит. И двете са метастабилни фази и ще се трансформират при определени условия.
Свойства на мартензит: Мартензитът се характеризира с висока твърдост, но също така и висока бритълност (особено при високовъглероден игла, подобен на мартензит), което не отговаря на изискванията за производителност за много приложения.
Характеристики на мартензитната трансформация: Трансформацията в мартензит се осъществява много бързо. След гасенето, детайлът има остатъчни вътрешни напрежения, които могат да доведат до деформация или напукване.
Заключение: Работата не може да се използва директно след гасене! Темпорането е необходимо за намаляване на вътрешните натоварвания и подобряване на здравината на детайла, което го прави подходящ за употреба.
2. Откриване между втвърдяване и капацитет за втвърдяване:
Втвърдителност:
Втвърдимостта се отнася до способността на стоманата да постигне определена дълбочина на втвърдяване (дълбочината на втвърдения слой) след гасенето. Зависи от състава и структурата на стоманата, по -специално неговите легиращи елементи и вида на стоманата. Втвърдимостта е мярка за това колко добре стоманата може да се втвърди през цялата си дебелина по време на процеса на гасене.
Твърда (капацитет за втвърдяване):
Твърдостта или капацитета за втвърдяване се отнася до максималната твърдост, която може да бъде постигната в стоманата след гасене. Той до голяма степен се влияе от съдържанието на въглерод в стоманата. По -високото съдържание на въглерод обикновено води до по -висока потенциална твърдост, но това може да бъде ограничено от легиращите елементи на стоманата и ефективността на процеса на гасене.
3. МАРДАРТИВНОСТ НА Стоманата
√Concept на втвърдяване
Втвърдимостта се отнася до способността на стоманата да постигне известна дълбочина на мартензитичното втвърдяване след гасене от температурата на аустенитизиране. По -просто казано, способността на стоманата да образува мартензит по време на гасене.
Измерване на втвърдяване
Размерът на втвърдяване се обозначава с дълбочината на втвърдения слой, получен при определени условия след гасенето.
Втвърдена дълбочина на слоя: Това е дълбочината от повърхността на детайла към региона, където структурата е наполовина мартензит.
Често срещани медии:
• Вода
Характеристики: Икономично със силна способност за охлаждане, но има висока скорост на охлаждане в близост до точката на кипене, което може да доведе до прекомерно охлаждане.
Приложение: Обикновено се използва за въглеродни стомани.
Солена вода: разтвор на сол или алкали във вода, който има по -голям капацитет за охлаждане при високи температури в сравнение с водата, което го прави подходящ за въглеродни стомани.
• Масло
Характеристики: осигурява по -бавна скорост на охлаждане при ниски температури (близо до точката на кипене), което ефективно намалява тенденцията за деформация и напукване, но има по -ниска способност за охлаждане при високи температури.
Приложение: Подходящо за алуминиеви стомани.
Видове: Включва гасене на масло, машинно масло и дизелово гориво.
Време за отопление
Времето за отопление се състои както от скоростта на отопление (времето, необходимо за достигане на желаната температура), така и от времето на задържане (време, поддържано при целевата температура).
Принципи за определяне на времето за отопление: Осигурете равномерно разпределение на температурата през целия детайл, както отвътре, така и отвън.
Осигурете пълна аустенитация и че образуваният аустенит е равномерен и фин.
Основа за определяне на времето за отопление: обикновено се оценява с помощта на емпирични формули или определено чрез експериментиране.
Учистване на медиите
Два ключови аспекта:
А. Скорост на охлаждане: По -високата скорост на охлаждане насърчава образуването на мартензит.
B. РЕСИДУАЛЕН СЛЕД: По -високата скорост на охлаждане увеличава остатъчния стрес, което може да доведе до по -голяма тенденция за деформация и напукване в детайла.
Ⅶ. Ненормализиране
1. Определение за нормализиране
Нормализирането е процес на обработка на топлината, при който стоманата се нагрява до температура 30 ° C до 50 ° C над температурата на AC3, задържана при тази температура и след това се охлажда, за да се получи микроструктура, близо до състоянието на равновесие. В сравнение с отгряването, нормализирането има по -бърза скорост на охлаждане, което води до по -фина перлитна структура (P) и по -висока якост и твърдост.
2. Цел на нормализирането
Целта на нормализирането е подобна на тази на отгряването.
3. Приложения за нормализиране
• Елиминирайте мрежовия вторичен циментит.
• Служи като окончателна топлинна обработка за части с по -ниски изисквания.
• Действайте като подготвителна топлинна обработка на ниско и средно въглеродна конструктивна стомана за подобряване на обработваемостта.
4.Типове отгряване
Първи тип отгряване:
Цел и функция: Целта не е да се предизвиква фазова трансформация, а да се премине стоманата от небалансирано състояние в балансирано състояние.
Типове:
• Отгряване на дифузия: Цели хомогенизирането на състава чрез елиминиране на сегрегацията.
• Отгряване на прекристализация: Възстановява пластичността чрез елиминиране на ефектите от втвърдяването на работата.
• Отгряване на облекчаване на стреса: Намалява вътрешните напрежения, без да променя микроструктурата.
Втори тип отгряване:
Цел и функция: Цели да се промени микроструктурата и свойствата, постигайки микроструктура, доминирана от перлит. Този тип също така гарантира, че разпределението и морфологията на перлит, ферит и карбиди отговарят на специфичните изисквания.
Типове:
• Пълно отгряване: Загрява стоманата над температурата на AC3 и след това бавно я охлажда, за да се получи равномерна перлитна конструкция.
• Непълно отгряване: Затопва стоманата между температурите на AC1 и AC3, за да трансформира частично конструкцията.
• Изотермично отгряване: Затопва стоманата до над AC3, последвано от бързо охлаждане до изотермична температура и задържане за постигане на желаната структура.
• Сфероидизиращо отгряване: произвежда сфероидна карбидна структура, подобрявайки обработваемостта и здравината.
Ⅷ.1. Определяне на топлинната обработка
Топлинната обработка се отнася до процес, при който металът се нагрява, задържа се при определена температура и след това се охлажда, докато е в твърдо състояние, за да се промени вътрешната му структура и микроструктура, като по този начин постига желаните свойства.
2. Характеристика на топлинната обработка
Топлинната обработка не променя формата на детайла; Вместо това тя променя вътрешната структура и микроструктурата на стоманата, което от своя страна променя свойствата на стоманата.
3. Определяне на топлинната обработка
Целта на топлинната обработка е да се подобрят механичните или обработващите свойства на стоманата (или детайлите), да използват напълно потенциала на стоманата, да повишат качеството на детайла и да удължат експлоатационния си живот.
4. Ключово заключение
Дали свойствата на материала могат да бъдат подобрени чрез топлинна обработка, зависи критично от това дали има промени в неговата микроструктура и структура по време на процеса на отопление и охлаждане.
Време за публикация: 19 август-2024